The same rotational molding product but with 40% less energy thanks to Icorene 1490
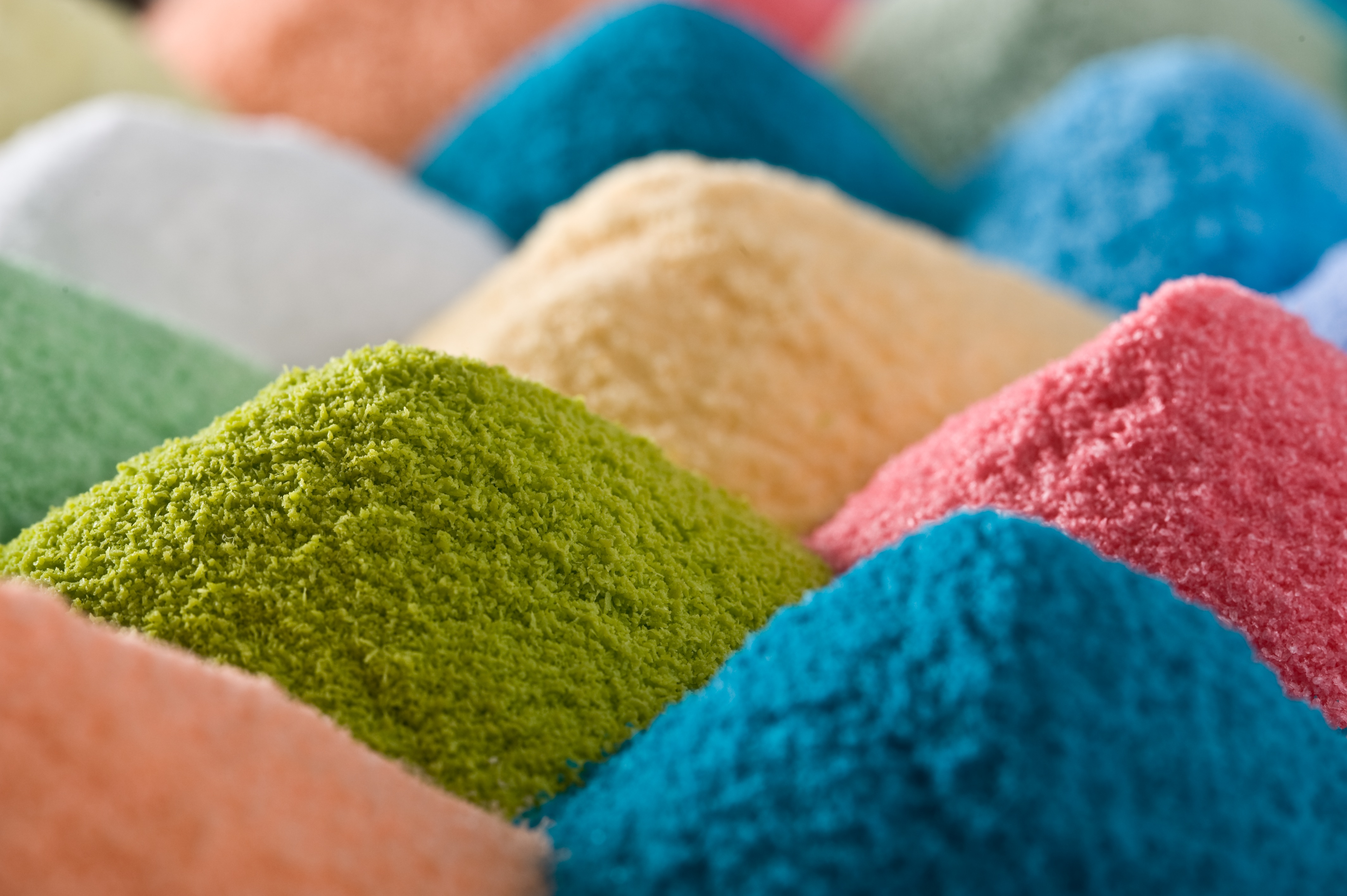
At Pentas, we are continuously committed to making our rotational molding process more sustainable and efficient. We achieve this by embracing new technologies, among other methods. Over the past few years, LyondellBasell has been working on a new material called Icorene 1490. We have tested this material in practice with them, which ultimately led to very impressive results. The material requires much less energy to melt into a quality product, which not only reduces our ecological footprint but also improves the quality and efficiency of our production.
Icorene 1490 is an advanced plastic, part of the medium density linear polyethylene category. This means it is made from chains of polyethylene with a medium density, making the material strong and versatile.
A key feature of Icorene 1490 is its excellent resistance to crack growth under stress (ESCR), indicating that the material is very resistant to cracks caused by external factors such as chemicals or extreme weather conditions. Additionally, Icorene 1490 has a high impact strength at low temperatures, down to -40°C, making it exceptionally durable, even in cold environments.
A significant advantage of Icorene 1490 is that it can be processed quickly, resulting in shorter cycle times and high performance. This means we can save time and energy during the production process, leading to greater efficiency and cost-effectiveness.
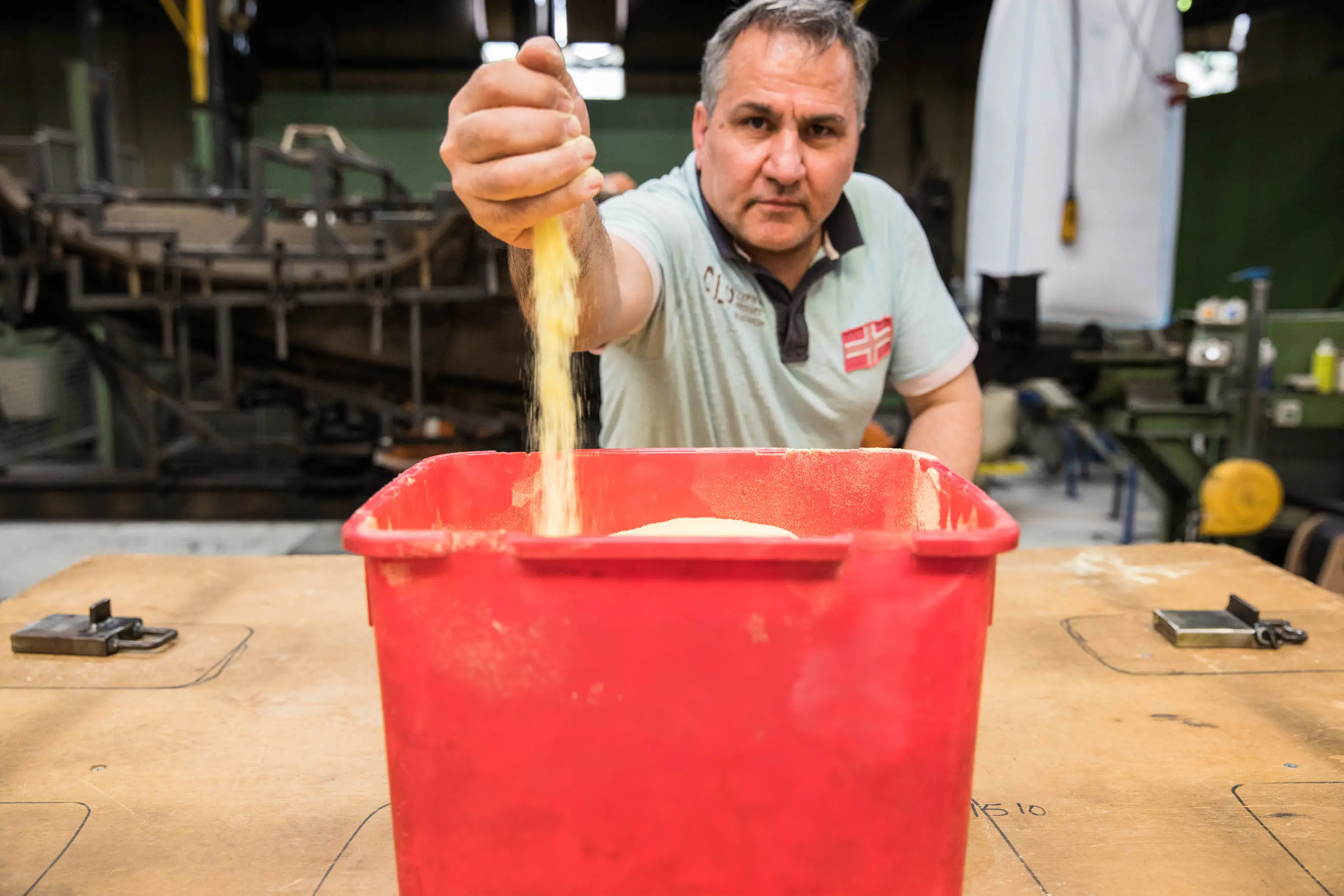
At Pentas, we see the benefits of Icorene 1490 daily, such as in the production of our 110-liter gray water tank, where we observe a considerable reduction in production time. The quality and durability of products made with Icorene 1490 are impressive. They are not only high in quality of finish but also exhibit excellent resistance to impacts, which is essential for our customers in the recreational vehicle sector.
Normally, our standard material requires a processing time of at least 18 minutes in a 300°C oven. Afterward, we cool it for 20 minutes, which brings our total rotation time to 20 minutes, and we produce a part every 7 minutes. Now that we have switched to Icorene 1490, we can reduce the oven temperature to 270°C and shorten the rotation time to 11 minutes, allowing us to produce a part every 4 minutes.
This improvement in efficiency supports us in our ongoing effort to reduce our ecological footprint. Another initiative we have undertaken in this context is the installation of 1660 solar panels on our roof, and we produce products with a sustainable character for industries such as the wind turbine industry.
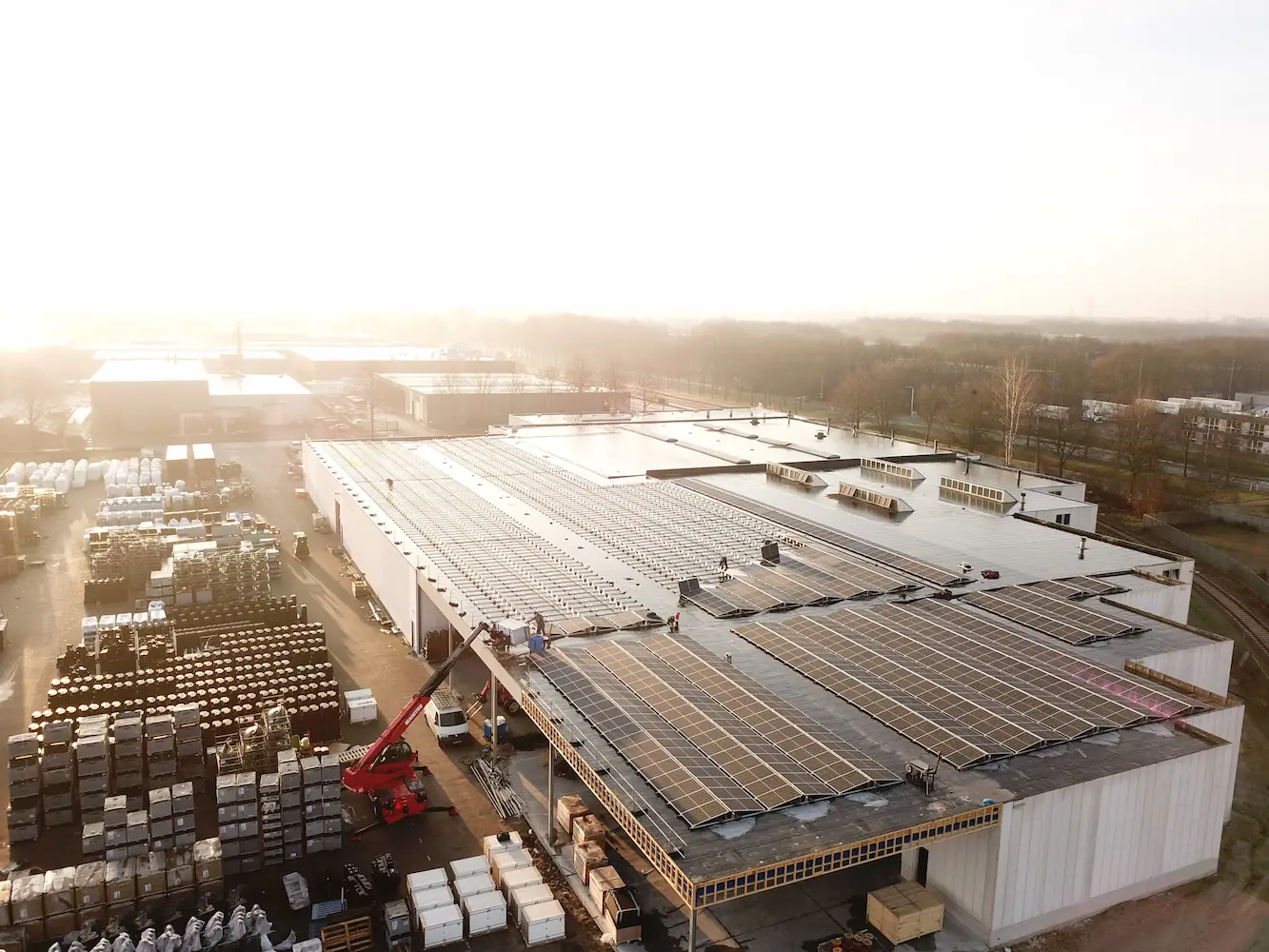