The future of recycling in the rotational moulding industry: challenges, innovations, and sustainability
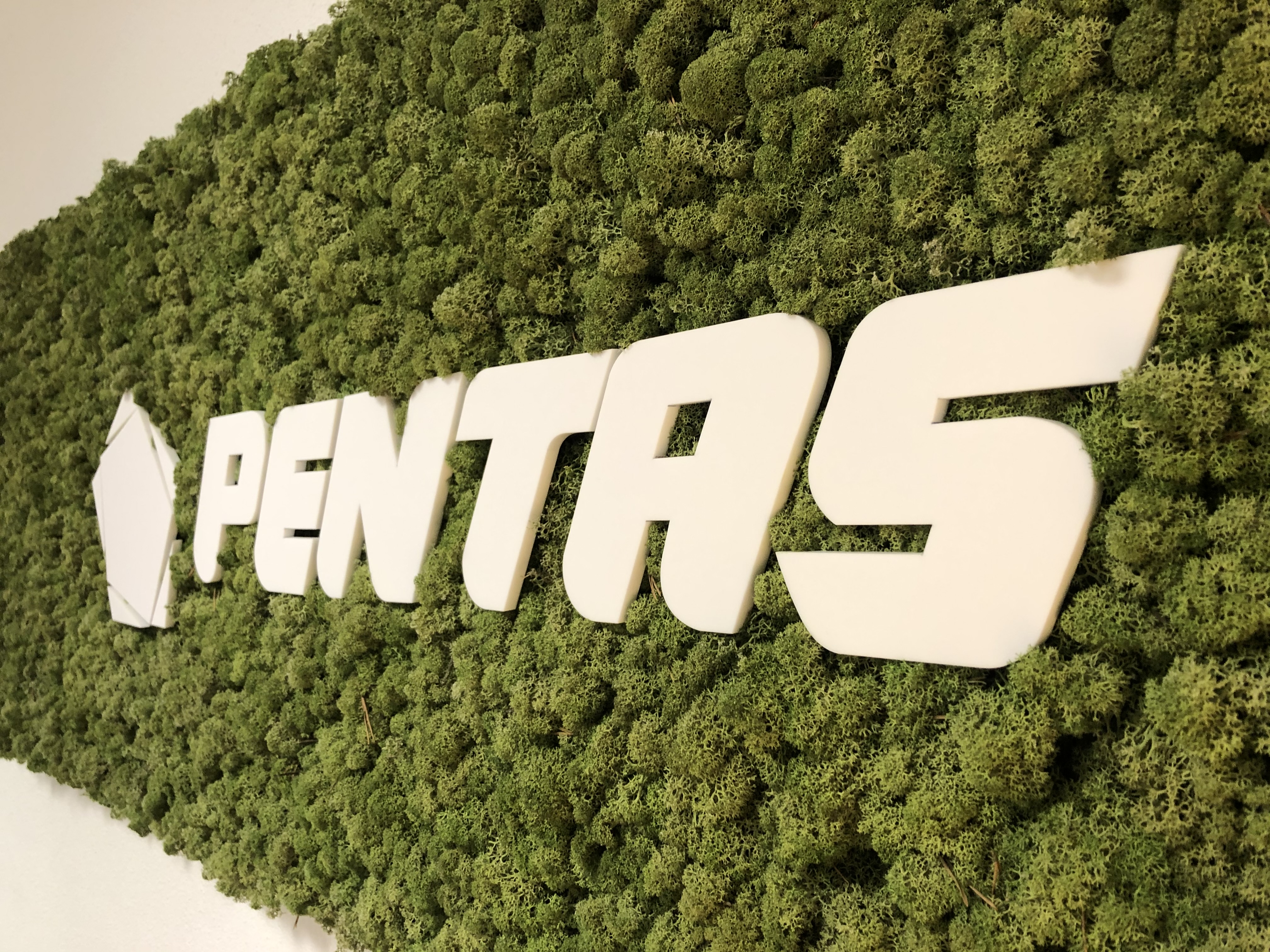
The plastics industry is facing significant changes, as the assumption of using virgin materials for manufacturing products is shifting. This change is driven by increasing environmental awareness and the need to reduce the consumption of new raw materials. There is an urgent demand for smart ways to reuse and recycle plastic waste, with reference to the Waste Framework Directive (WFD) within European regulations.
This framework states that recycling involves processing waste to create new products, materials, or substances. These can serve the same purpose as the original or a different one. The idea is to use fewer new raw materials by reusing waste, which is beneficial for the environment and helps in creating a circular economy.
To advance collectively, new regulations have been established, which we will further elaborate on in this article, along with the challenges and obstacles in the path to sustainability.
From linear to circular economy
The transition from a linear to a circular economy represents a fundamental shift in how we think about and deal with our resources, products, and waste. In a linear economy, we follow the path of 'take, make, use, dispose,' where raw materials are converted into products that are discarded at the end of their lifespan. This model is not sustainable in the long term, given the finite nature of our resources and increasing environmental pressures.
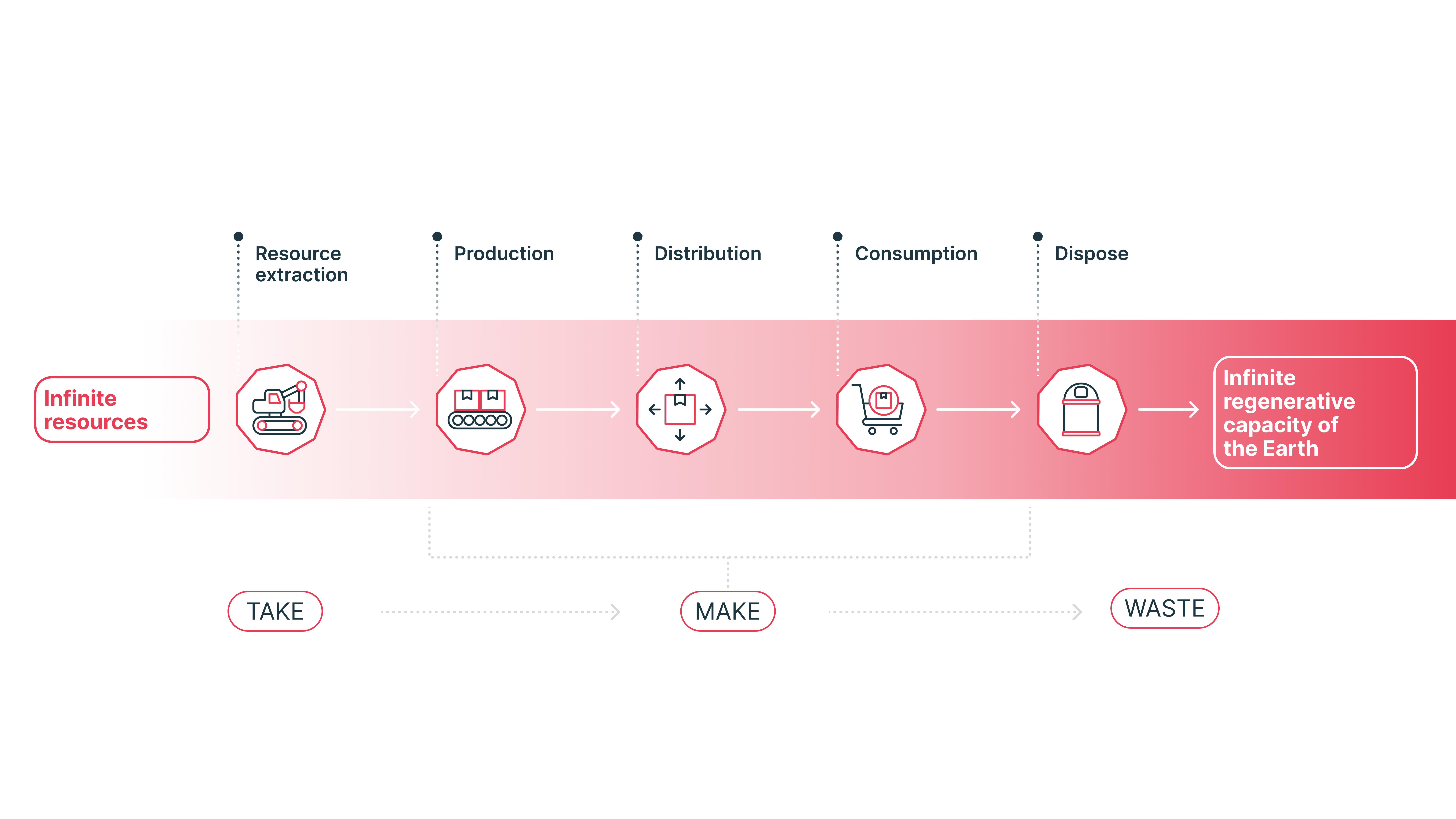
In contrast, a circular economy emphasizes keeping products and materials in use for as long as possible, maximizing their value during use, and then restoring and regenerating them at the end of their lifecycle. This model aims to minimize waste through reuse, repair, refurbishment, and recycling. In a circular economy, products are designed and produced with future reuse and recycling in mind, leading to more sustainable resource utilization.
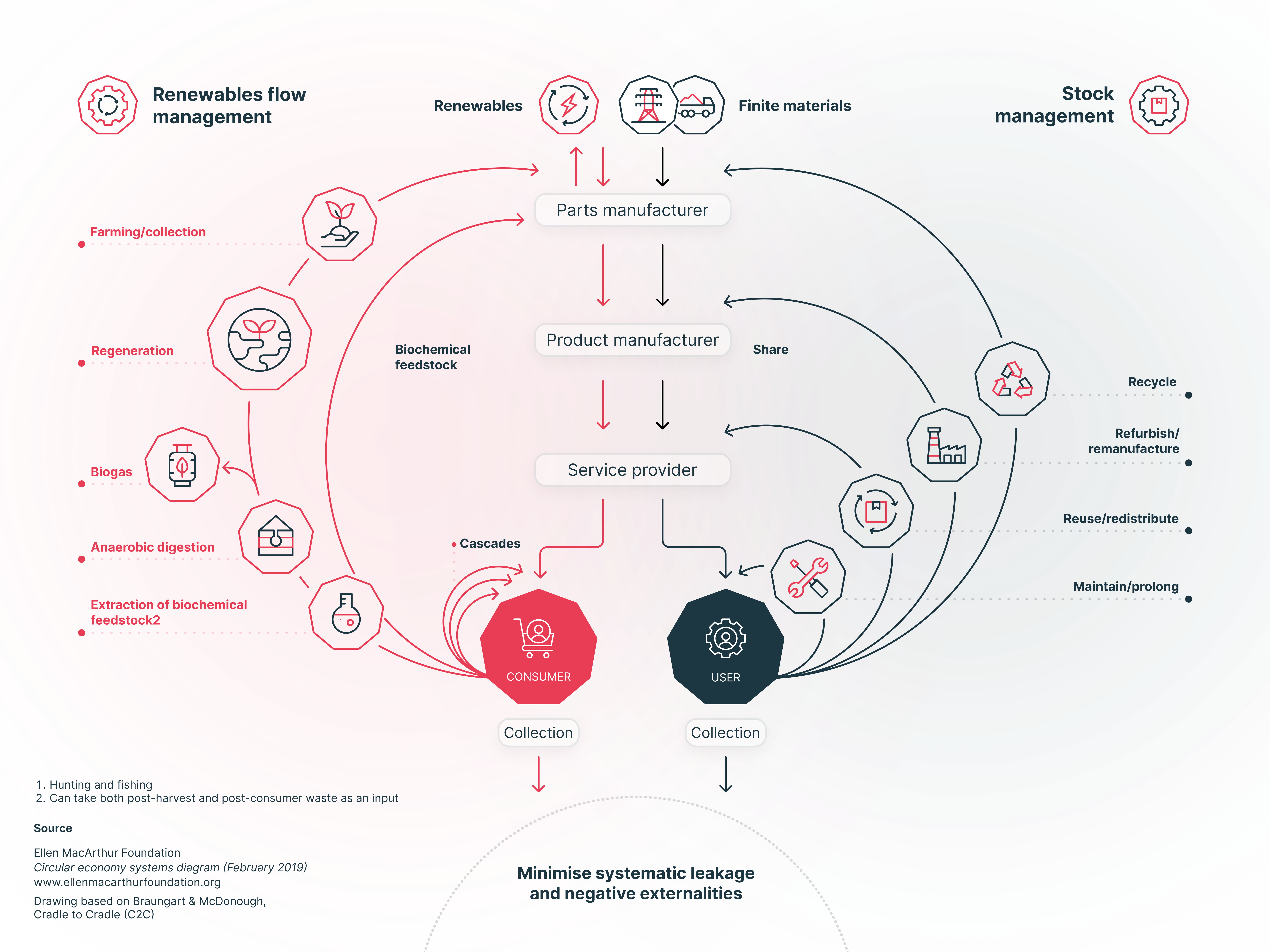
Rotational moulding in the circular industry
Rotational moulding is a unique production process (constituting approximately 3% of plastic processing techniques) for manufacturing pressureless plastic products. This process imposes specific requirements on the materials used, limiting the types of plastics suitable for it. Most products in our industry are made from polyethylene (PE) or polypropylene (PP). These materials are also chemically optimized specifically for rotational molding, meaning not every type of PE or PP is suitable for use in this process. This specificity poses a challenge to using recycled materials for producing high-quality products within the rotational molding industry.

Three types of waste streams are distinguished in the market:
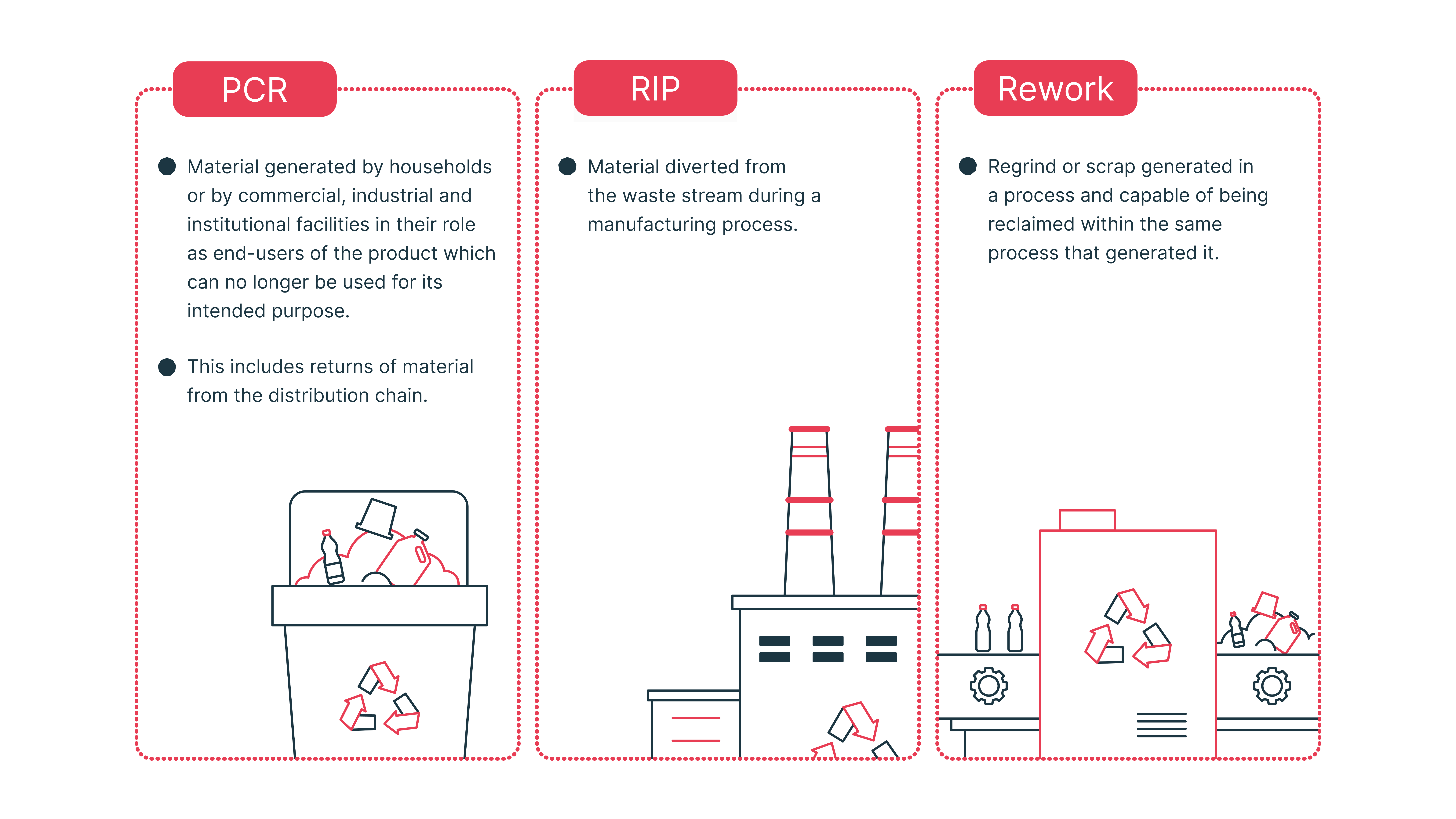
Different types of recycled materials in rotational moulding:
The rotational moulding industry actively seeks ways to integrate recycling into its production processes, particularly through the reuse of polyethylene (PE), a commonly used material in this field. Below is how the industry deals with recycling PE for rotational moulding:
The process from used product to new material:
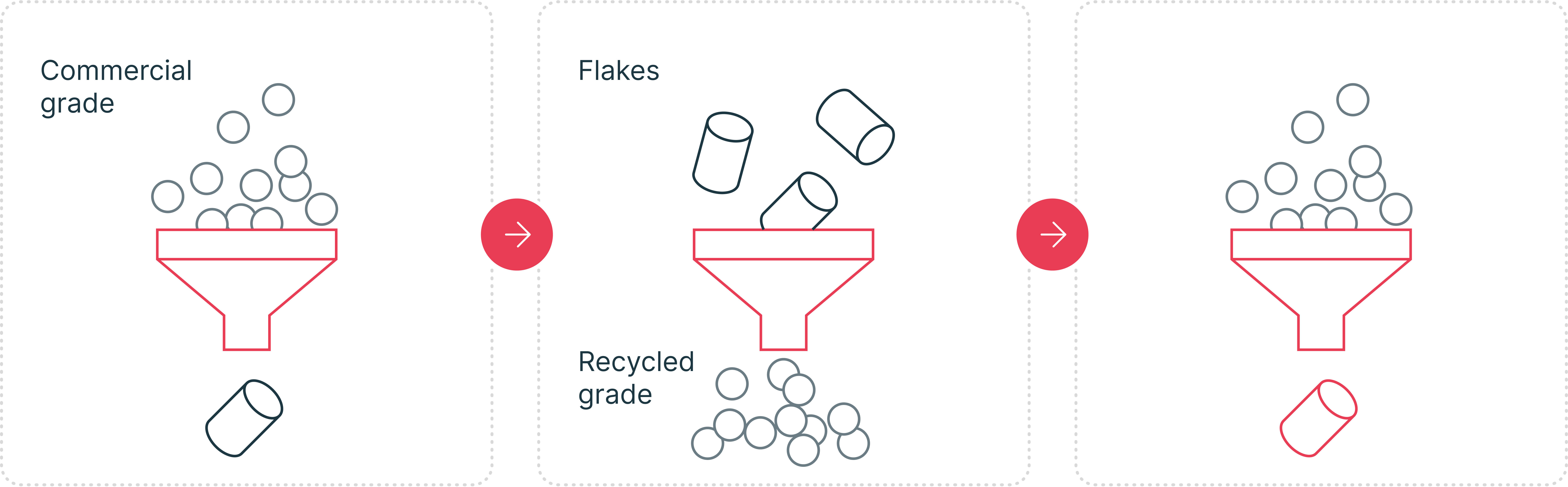
To refine the process of recycling used polyethylene (PE) rotational moulded products into new material, we add a few crucial steps at the beginning of the process:
Disassembly of Products: Disassembling composite products to determine which materials are suitable for recycling and which are not. This is essential to process only pure rotational moulding material.
Sorting of Rotational Moulding Material: After disassembly, careful sorting of materials is carried out, distinguishing between actual rotational moulding material and non-matching materials. This step ensures that only compatible materials are recycled.
Coarse Shredding (6x6cm): Before the products are reduced to the finer 2x2 centimeters, they are first roughly shredded into pieces of about 6x6 centimeters. This makes it easier to process larger volumes and prepare for the next steps.
The process then continues as described earlier:
Washing: Cleaning the used products to remove contamination and residues.
Shredding (2x2cm): Reducing the products to pieces of about 2x2 centimeters.
Color Sorting (optional): Sorting the pieces by color, if necessary.
Extrusion Additives: Adding extrusion additives to the PE.
Grinding: Further grinding the material into finer particles.
By recycling used rotational moulded products in this way, high-quality rotational molding material (rPE) can be produced for use in high-quality products.
Supply chain transparency through a digital Product passport (DPP):
To make the recycling process of rotational moulded products efficient and effective, implementing a recycling label for rotational moulding material on future products is crucial. This label will inform recycling companies of the material the product is made of and how it should be further processed. Currently, sorting is only done by main groups such as PE and PP, but as indicated, this is not sufficient for rotational molding material, so an R-PE label indicating that the PE material is specifically designed for rotational moulding is necessary.
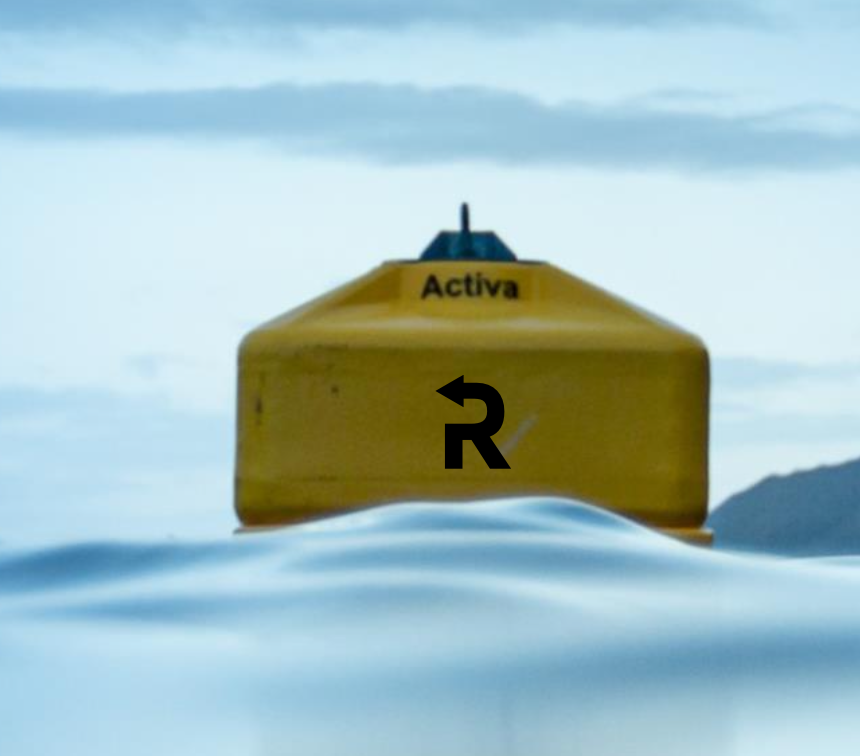
In addition, products of the future will receive a Digital Product Passport (DPP). This is a database with product specifications at the product-instance level. A unique product number in this database refers to, for example, the material the product is made from, CO2 footprint, and the manufacturer.
Pentas has been committed to the traceability of its products for over ten years, with each produced item being individually registered in a database. This database contains essential information such as the production date and location, as well as the materials used, which is extremely useful for recycling purposes.
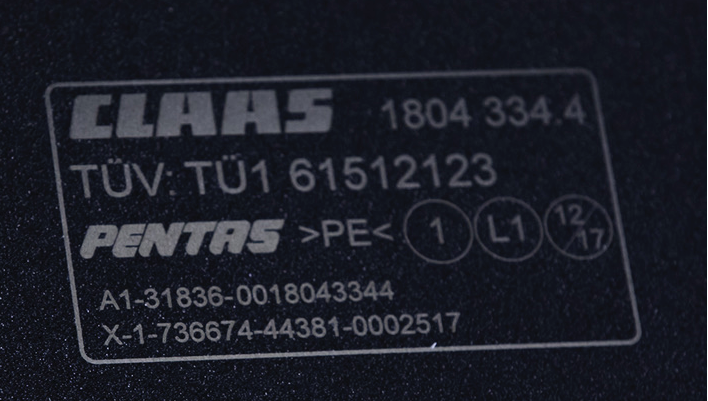
For the future, this approach will be further expanded by making this data available in an online database. GS1, a global non-profit organization specialized in standardizing product identification and barcodes, plays a leading role in this. GS1 develops standards for identifying, capturing, and sharing product data across the entire value chain, contributing to increased efficiency, safety, and traceability.
European Union guidelines for 2030
By 2030, the European Union aims to ensure that all plastic packaging on the market is reusable or easily recyclable, including rotational moulded water tanks, for example. The plan is for more than half of all plastic waste in Europe to be recycled by that time.
To achieve this, a system called Extended Producer Responsibility (EPR) is utilized. This means that companies producing products are also responsible for what happens at the end of the product's lifecycle. They must ensure that products are easy to take back, reuse, or recycle.
What's Next?
The rotational moulding industry faces challenges, primarily focused on developing high-quality recycled polyethylene (PE) materials. A logical step in this direction is identifying used rotational moulding material through a certification mark or an online database. Additionally, by making agreements with customers regarding the handling of waste after use, we can recover these valuable resources and reuse them for the production of high-quality recycled material. It is essential for the industry to move forward together.