Innovative Air Duct for Schmitz Cargobull
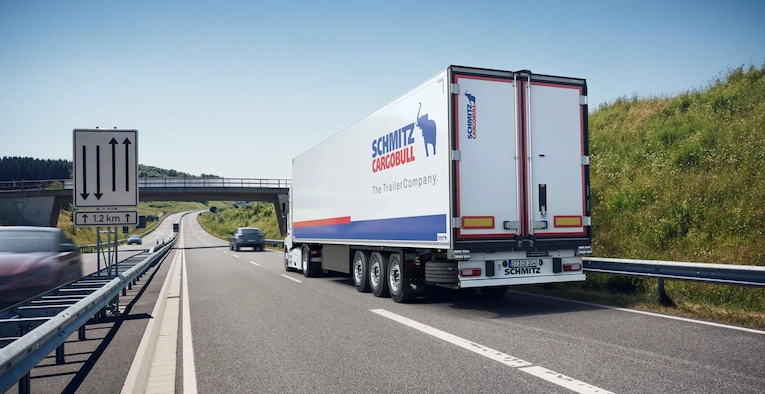
At Pentas, we take pride in serving a wide range of industries, including the automotive sector. In this industry, the use of rotational moulding is increasing due to the unique advantages the technique offers. One example is our collaboration with Schmitz Cargobull, a leading player in the transport sector specializing in trailer manufacturing. Together, we developed a sustainable solution to replace traditional sheet metal air ducts with robust and flexible air ducts produced through rotational moulding. In this case study, we take you through the challenges, the process, the collaboration, and the results of this successful project.
Table of contents
The challenge
Schmitz Cargobull originally used air ducts made from thin sheet metal. While these initially served their purpose, practical issues frequently arose. During the loading of taller pallets, the air ducts were often struck, leading to irreparable damage. This meant the dented ducts frequently needed replacement, resulting in significant costs and disruptions to daily operations.
To structurally solve this problem, Schmitz sought an innovative and sustainable solution. The new air duct needed to be flexible and durable enough to withstand impacts without permanent damage. Additionally, the material had to be food-safe to comply with strict hygiene regulations. Schmitz also had specific operational requirements: the duct had to be easy to replace in case of damage to minimize downtime, lightweight to reduce the load on vehicles, and designed with drainage openings to efficiently remove condensation and prevent corrosion.
This combination of functional and practical requirements formed the foundation for developing an innovative solution to overcome Schmitz's operational challenges.
The solution
Pentas was invited by Schmitz to analyze the situation on-site in Vreden, Germany. During our visit to the production facility, we gained a full understanding of the issues and specific challenges. This led to the start of a project where we worked together on custom-made, flexible air ducts.
Director Marthijn Koorn with the air duct.
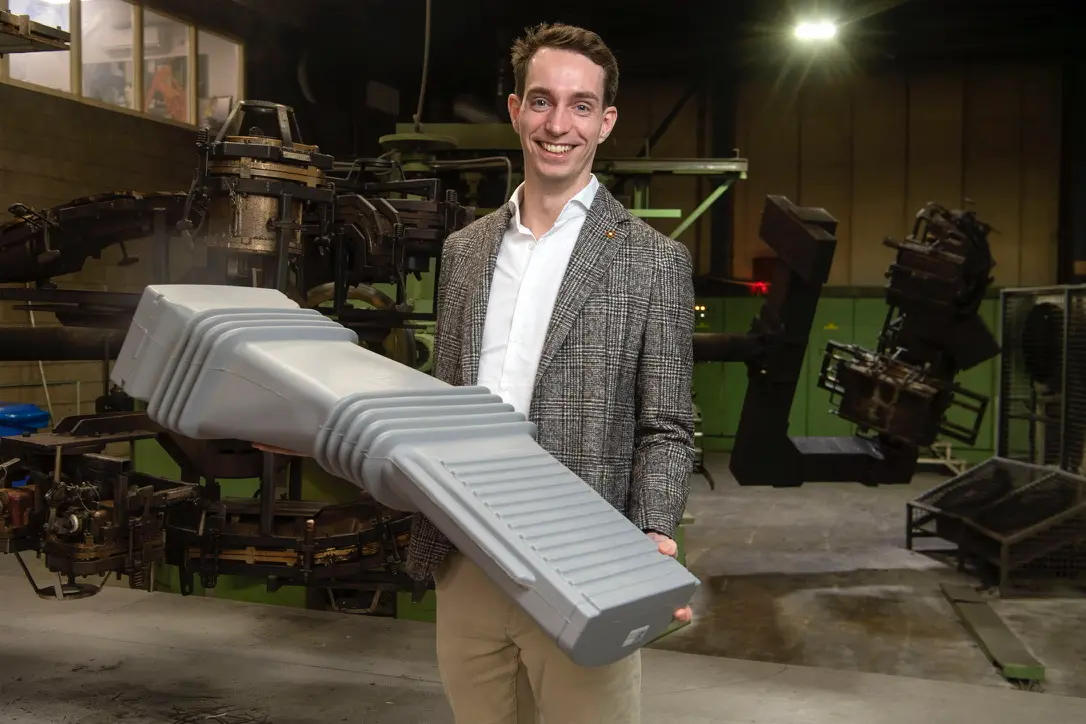
Innovation through rotational moulding
To meet strict requirements regarding hygiene, surface quality, and flexibility, both the design and the material of the air ducts were developed in parallel. In collaboration with our raw material supplier, we selected a plastic that was not only durable and flexible but also lightweight and food-safe.
One of the challenges was that no existing material met all these requirements. The development process was not without obstacles, as the material initially proved difficult to process using rotational moulding. We encountered many pinholes, and the product was difficult to remove from the mould. Several iterations and innovations were necessary to achieve a good result, requiring close collaboration between all parties.
Additionally, we conducted an extensive Failure Mode and Effects Analysis (FMEA) to identify and minimize potential risks in the design and production process. Internally, we created and tested multiple designs. Ultimately, we designed the product as a bellows-like structure, adding even more flexibility to the air duct. This made it more adaptable for various air conditioning systems in refrigerated trailers.
The mould for the air duct, in which the distinctive accordion structure is clearly visible.
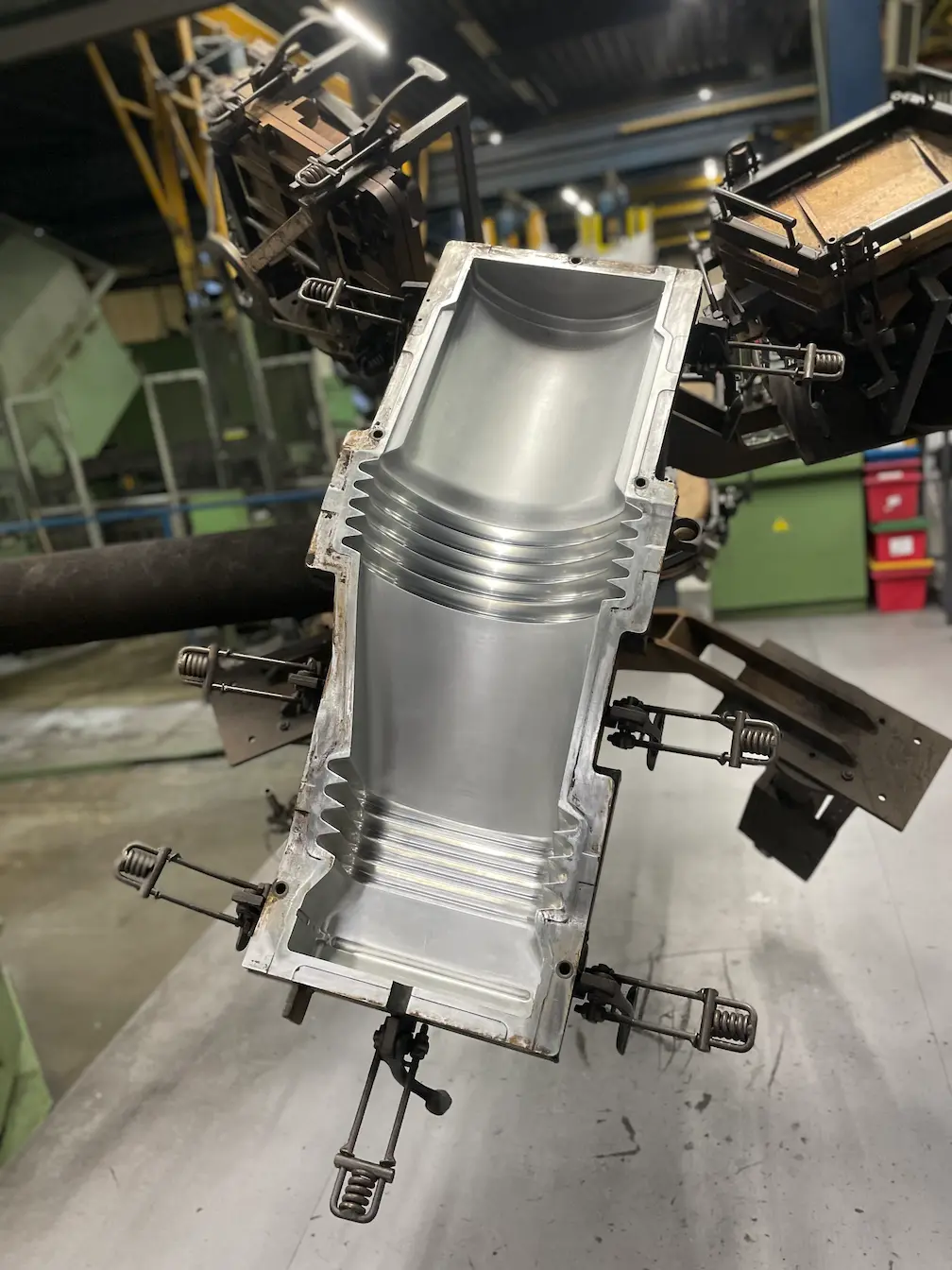
The final design integrated innovative features, such as drainage openings and a pre-assembled mounting system for easy installation. Milling operations were also applied to ensure both openings in the product were precisely executed.
Rotational moulding proved to be the ideal production technique for this application. It allowed us to manufacture stress-free, hollow products with uniform wall thicknesses, resulting in an air duct that was both economically and functionally superior to the traditional sheet metal version.
The process
The development process, which took over 12 months, involved intensive collaboration between the teams from Schmitz, Pentas, and our raw material supplier. During the design phase, multiple prototypes were tested to find the perfect balance between flexibility, durability, and user-friendliness.
The flexible air ducts are shock-resistant and return to their original shape after a collision without permanent damage.
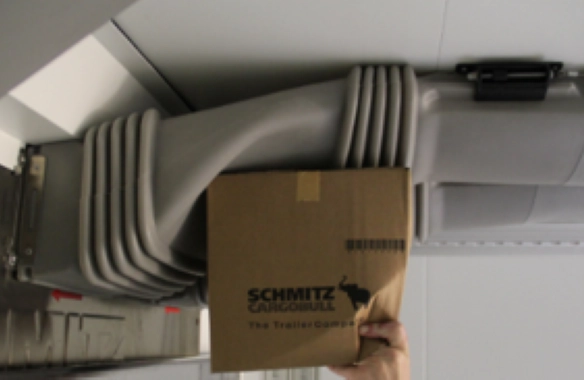
Because the material was new to this application, special tooling also had to be designed. After finalizing the design and production configurations, extensive laboratory and practical tests were conducted to ensure the air ducts met all functional and technical requirements.
The result
The final product exceeded all expectations and fully resolved Schmitz’s challenges. The flexible air ducts proved to be extremely impact-resistant, as they recover from collisions without permanent damage. This minimized damage caused by careless loading and resulted in significant cost savings due to a lower replacement frequency and shorter installation times.
The lightweight design and easy installation also make the air ducts highly user-friendly. Since their introduction, no complaints have been received from end users, proving the quality and reliability of the product.
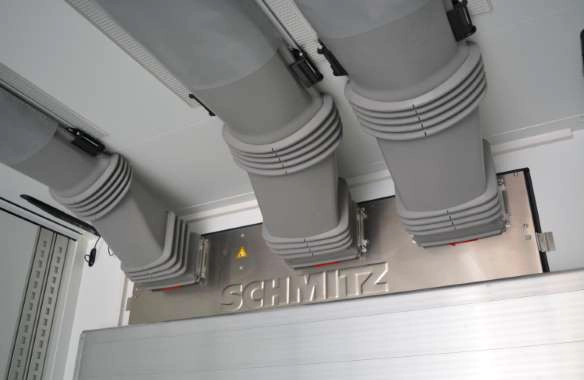
The future
Although the new air ducts are currently used exclusively for Schmitz’s refrigeration units, we see great potential for broader application in other areas of the transport sector. This collaboration illustrates how innovation and partnership can lead to solutions that not only solve problems but also create long-term value.
Curious about what rotational moulding can do for your company? Contact us and discover the possibilities!