Der Produktions- und Produktprozess bei Pentas
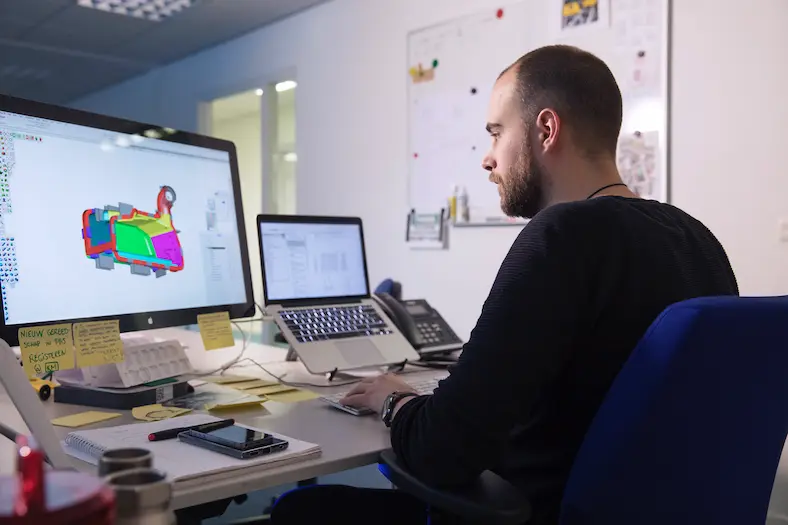
Ein gutes Rotationsgussprodukt beginnt mit einem durchdachten Produktprozess. Bei Pentas haben wir im Laufe der Jahre viel Erfahrung in der Entwicklung und Herstellung von Kunststofflösungen gesammelt. Sobald das Design für die Serienproduktion bereit ist, gehen wir den nächsten Schritt: die Produktfertigung. In diesem Artikel erläutern wir die einzelnen Schritte.
Table of contents
Phase 1: Erstellung des Pflichtenhefts
Ein gutes Rotationsgussprodukt beginnt mit einem klaren Pflichtenheft. Gemeinsam mit dem Kunden erstellen wir dieses Dokument als Grundlage für den gesamten Entwicklungsprozess. Darin legen wir die funktionalen und technischen Anforderungen an das Produkt fest.
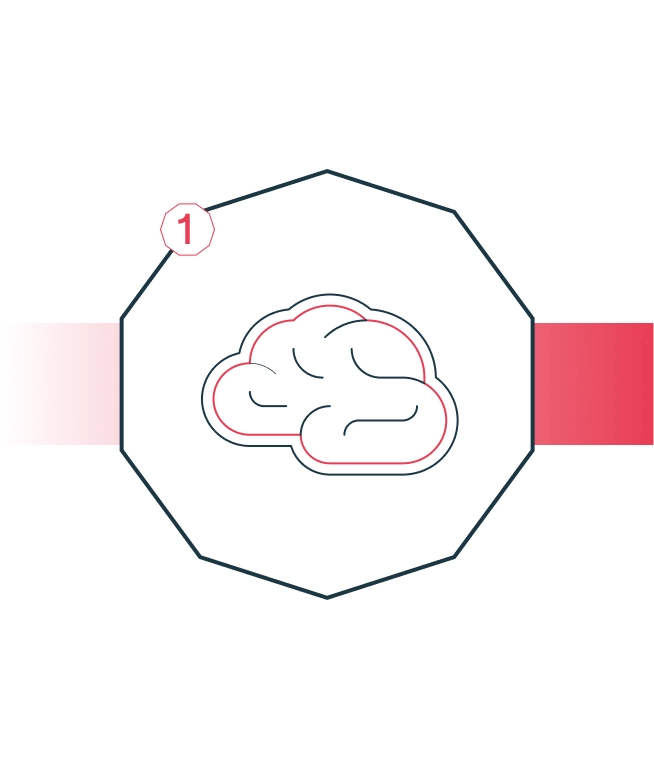
Dabei berücksichtigen wir nicht nur die Wünsche des Kunden, sondern bringen auch unsere langjährige Erfahrung ein. Was funktioniert in der Praxis? Wo kann man optimieren? Wo lauern mögliche Fallstricke? So entsteht ein vollständiges und realisierbares Anforderungspaket, das als klarer Leitfaden für die Produktentwicklung dient.
Beispiele für Inhalte eines Pflichtenhefts:
Phase 2: Konzeptentwicklung
In dieser Phase konzentrieren wir uns auf Design, Funktionalität und Herstellbarkeit. Wir entwickeln ein oder mehrere Konzepte und prüfen diese anhand des Pflichtenhefts. Dabei betrachten wir nicht nur die Form, sondern auch die Anwendung. Häufig werden zusätzliche Komponenten wie Füllstandsanzeiger, Verschlüsse oder Schläuche am Produkt montiert. Dank unseres breiten Lieferantennetzwerks haben wir Zugriff auf ein großes Sortiment an Montagekomponenten.
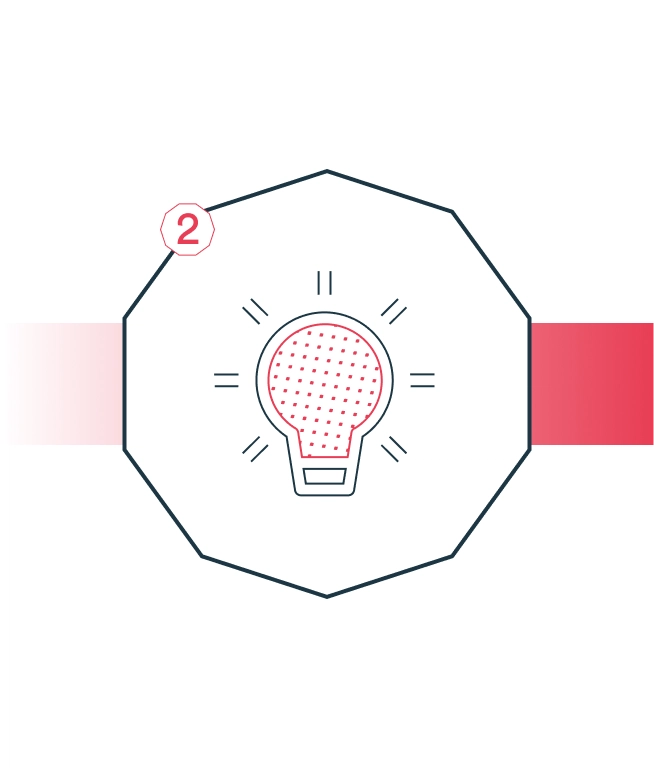
Phase 3: Analyse
Um Überraschungen in der Produktion zu vermeiden, führen wir im Vorfeld eine gründliche Risikoanalyse durch. Wir prüfen kritisch die Materialwahl und beurteilen, ob das Design für eine effiziente Montage geeignet ist. Mit der FMEA-Methode (Fehlermöglichkeits- und -einflussanalyse) erfassen wir potenzielle Fehlerquellen systematisch und treffen frühzeitig Gegenmaßnahmen.
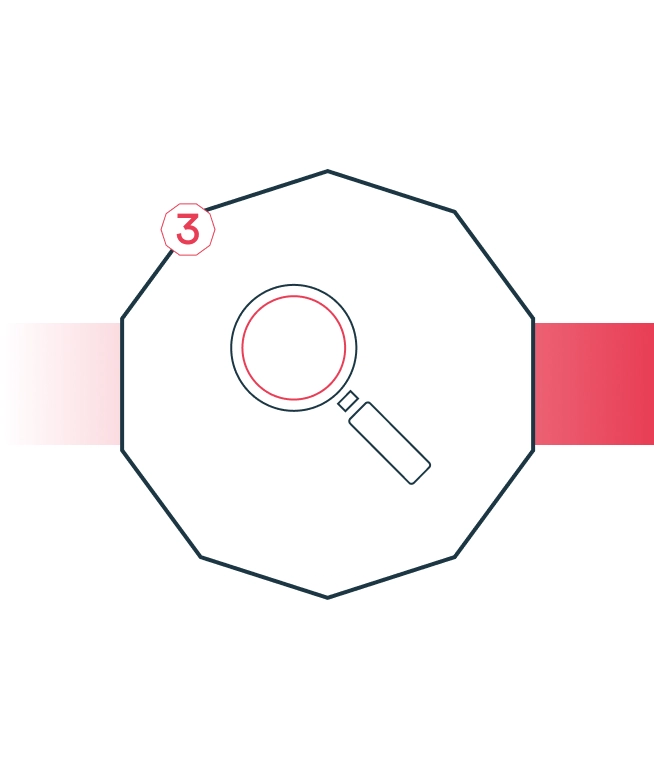
Ein wichtiger Bestandteil ist die Erstellung eines Kontrollplans. Dieser definiert, welche Qualitätsprüfungen wann, mit welchen Mitteln und Toleranzen durchgeführt werden. Zudem entwickeln wir „Poka-Yoke“-Lösungen – clevere Prozessanpassungen, die Fehler automatisch vermeiden helfen.
Phase 4: Finales Design und Freigabe
Diese Phase bildet die Brücke zwischen Design und Produktion. Das gewählte Konzept wird detailliert zu einem fertigungsgerechten Produkt ausgearbeitet. Je nach Wunsch des Kunden geschieht dies eigenständig oder in enger Zusammenarbeit mit dessen Technikteam.
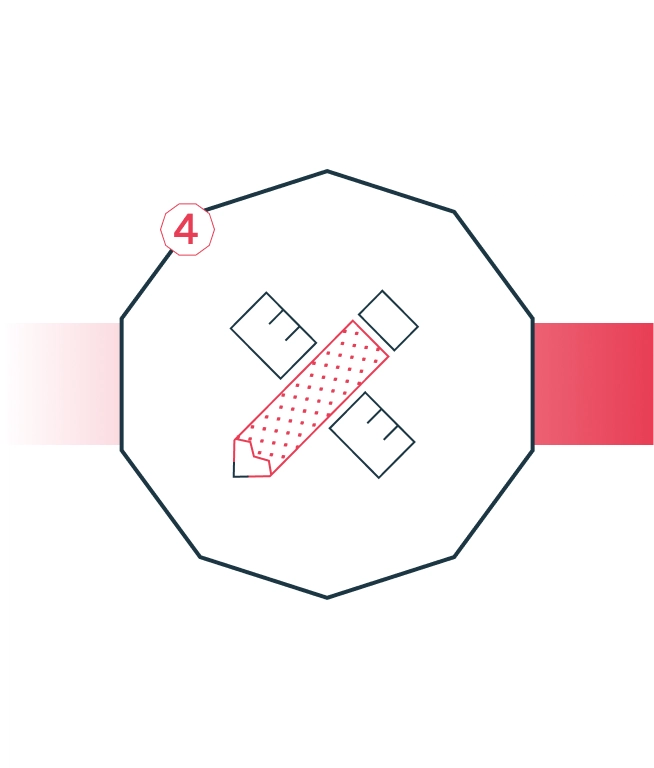
Wir legen Wandstärken, Verstärkungsrippen und Entformungsschrägen fest. Maße, Toleranzen und kritische Produkteigenschaften werden dokumentiert.
Darauf basierend erstellen wir ein präzises 3D-CAD-Modell zur Herstellung von Formen und Werkzeugen sowie detaillierte 2D-Zeichnungen für die Qualitätsprüfung.
Nach Freigabe durch den Kunden beginnt der Formenbau.
Phase 5: Formbau, Stützformen, Lehren und Automatisierung
Nach Freigabe der CAD-Zeichnungen starten wir mit dem Formbau. Da wir diesen komplett intern durchführen, bieten wir optimale Preis-Leistung und kurze Durchlaufzeiten.
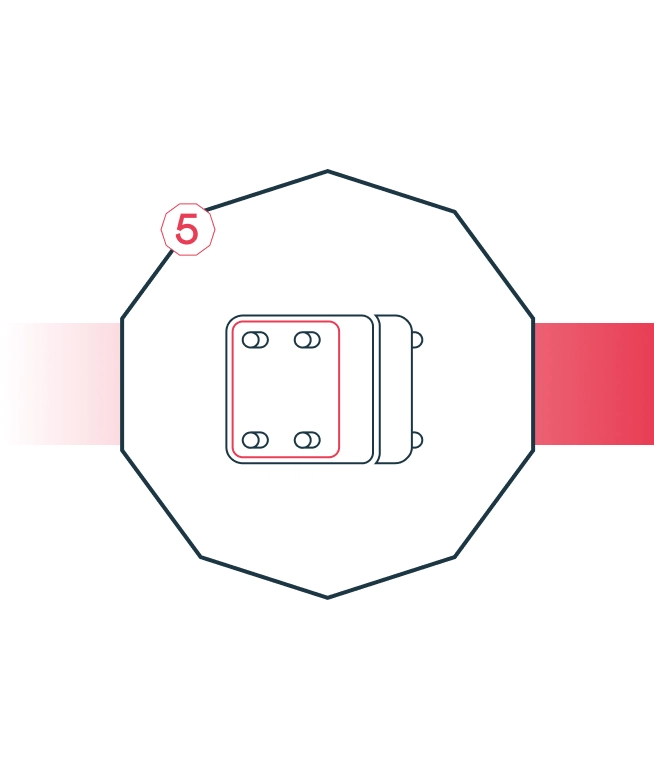
Parallel entwickeln wir die nötigen Stützformen, Lehren und Automatisierungslösungen wie Roboterprogramme oder Pick-&-Place-Systeme.
Eine detaillierte Projektplanung sichert den reibungslosen Ablauf der nächsten Produktionsschritte.
Phase 6: Erstmusterfreigabe (EMF) und Produktionsstart
Vor dem Start der Serienproduktion durchläuft das Produkt die Erstmusterfreigabe. Dabei validieren wir Produkt und Prozess.
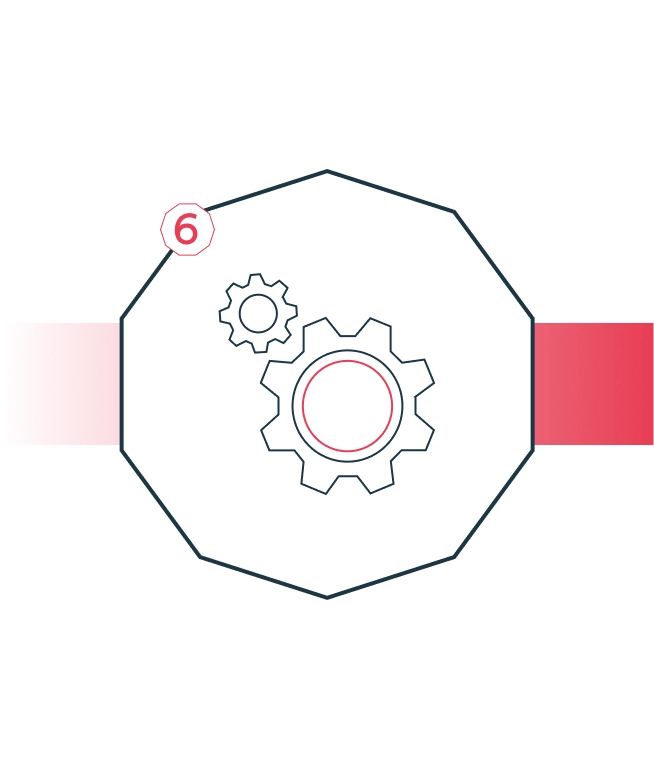
Nach Einbau der Form in die Rotationsgussmaschine wird eine kleine Testserie gefertigt. In dieser Phase optimieren wir Maschinenparameter wie Rotationsgeschwindigkeit, Temperaturprofile und Kühlzeiten für gleichbleibende Qualität und ideale Wandstärkenverteilung.
Die Produkte werden von unserer Qualitätsabteilung umfassend geprüft (Maße, Form, Gewicht, optische Qualität). Die Ergebnisse werden im EMF-Bericht dokumentiert.
Abweichungen werden analysiert und bei Bedarf im Design, der Form oder dem Prozess angepasst. Erst wenn alle Anforderungen aus dem Pflichtenheft erfüllt sind, erfolgt die Freigabe für die Serienproduktion.
Phase 7: Serienproduktion, Finish & Montage
Nach der Freigabe beginnt die Serienproduktion. Die Form wird entsprechend den Kundenaufträgen eingeplant. Alles ist auf eine stabile und reproduzierbare Qualität ausgerichtet. Alle Hilfsmittel, Komponenten, Anleitungen und Prüfmittel sind exakt abgestimmt.
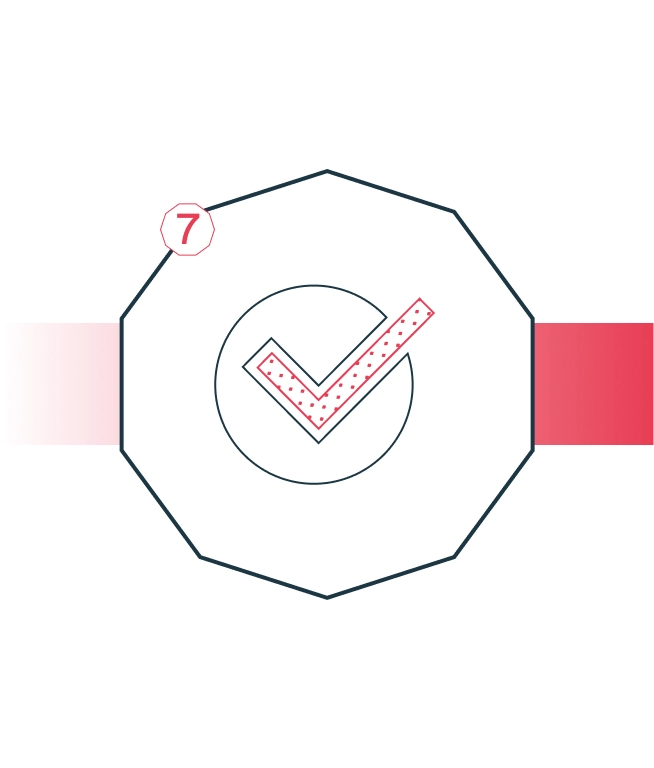
Unsere Techniker übernehmen die Nachbearbeitung: Entgraten, Bearbeiten, Prüfen. Bei Bedarf wird das Produkt vollständig montiert, etwa mit Sensoren, Schläuchen oder Kupplungen.
Die Qualitätssicherung bleibt zentral. Stichprobenprüfungen erfolgen mit Tablets und 3D-Scannern, direkt abgeglichen mit CAD-Daten. Bei Abweichungen wird an der Quelle nachgebessert. Abschließend übernehmen wir auch die Logistik – Just-in-Time und Just-in-Sequence, exakt auf den Produktionsprozess des Kunden abgestimmt.
Pentas verfügt über langjährige Erfahrung in der Entwicklung und Herstellung von Kunststoffprodukten mittels Rotationsguss. Jedes Projekt – vom Entwurf bis zur Auslieferung – wird sorgfältig begleitet. Präzision steht in jeder Phase im Mittelpunkt, mit Blick für technische Details und praktische Umsetzbarkeit. Unsere strukturierte Arbeitsweise und enge Abstimmung mit dem Kunden sorgen für einen reibungslosen Ablauf. Unsere Produkte finden weltweit Einsatz in verschiedensten Branchen.
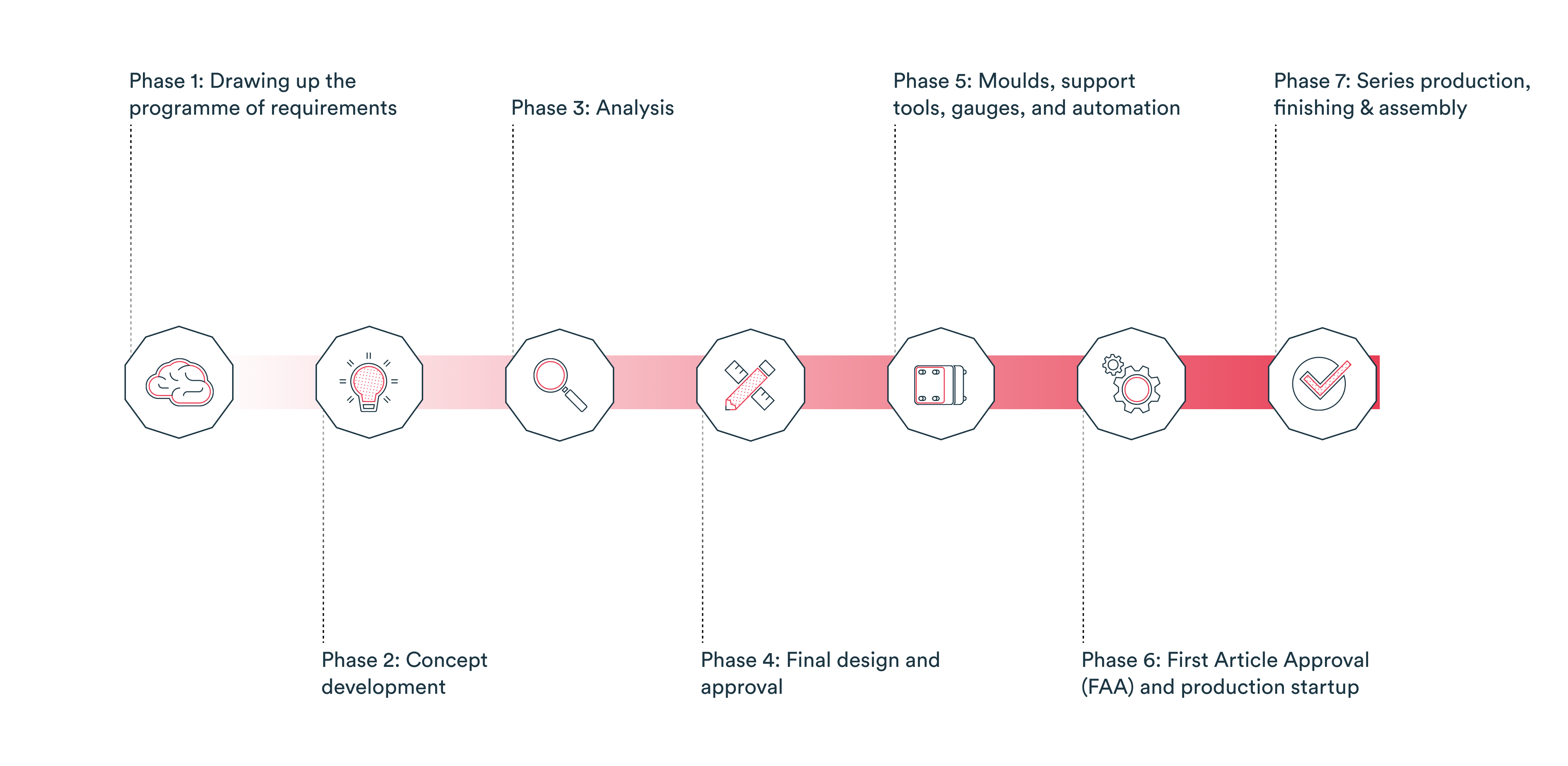