Entwurfsregeln beim Rotationsguss
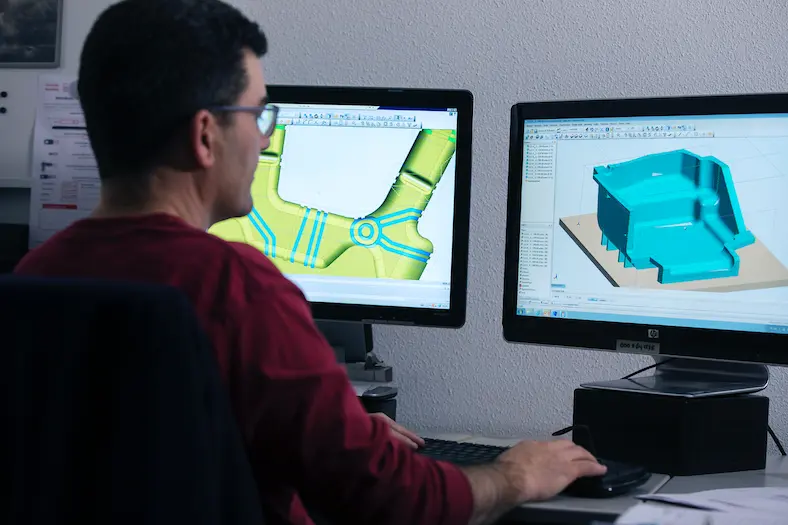
Rotationsguss ist ein Verfahren, bei dem Kunststoffpulver in eine hohle Form, auch Matrize genannt, eingebracht wird. Diese Matrize wird dann erhitzt und entlang zweier Achsen rotiert, wodurch das Pulver schmilzt und gleichmäßig entlang der Innenseite der Matrize verteilt wird, um eine hohle Kunststoffform zu erzeugen. Eine Matrize hat keinen inneren Kern; das Produkt wird durch die Innenwand der Matrize geformt. Der Produktionsprozess umfasst vier Hauptphasen: Befüllen, Erhitzen, Kühlen und Entformen. Nach dieser Phase wird die Matrize gereinigt und der Prozess beginnt von vorne.
Rotationsguss bietet einzigartige Vorteile und Herausforderungen, die gut verstanden werden müssen, um erfolgreich entwerfen und produzieren zu können. In diesem Artikel tauchen wir in die wichtigsten Entwurfsregeln und Überlegungen beim Rotationsguss ein.
Inhoudsopgave
Materialauswahl
Beim Rotationsguss gibt es nur eine begrenzte Anzahl geeigneter Materialien. Die am häufigsten verwendeten Materialien sind Polyethylen (PE) und Polypropylen (PP). Darüber hinaus können auch Materialien wie Polyvinylchlorid (PVC), Nylon und Polycarbonat (PC) verwendet werden, was jedoch seltener vorkommt. Polyethylen ist aufgrund seiner guten Verarbeitbarkeit, chemischen Beständigkeit und niedrigen Kosten bei weitem am beliebtesten. Die Materialwahl hängt von der erforderlichen Steifigkeit und Festigkeit, der Umgebungstemperatur, der benötigten chemischen Beständigkeit, den Anforderungen an Farbe und Dichtheit sowie der UV-Beständigkeit ab.
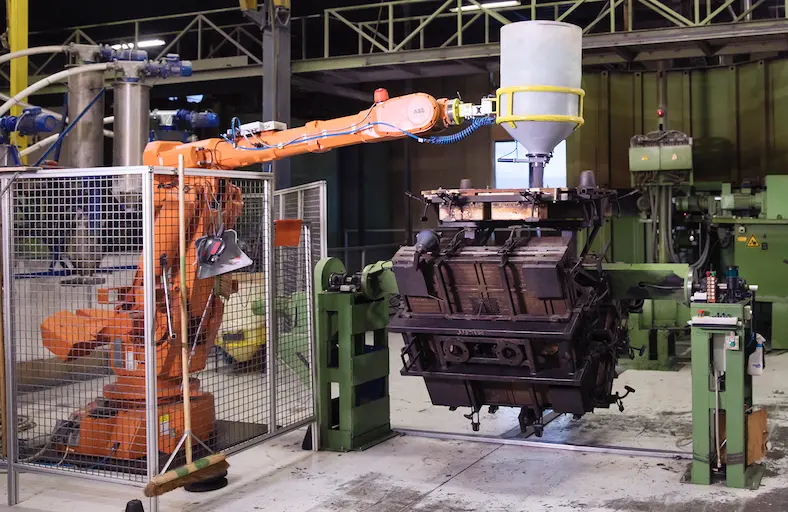
Anzahl der Produkte
Das Rotationsgussverfahren eignet sich für kleine und große Produktionsserien. Es kann für Serien ab 50 Einheiten angewendet werden, wird jedoch auch für große Serien von bis zu 75.000 Einheiten pro Jahr verwendet. Wenn die Mengen weiter steigen, wird oft eine andere Technik gewählt. Die Leistung einer Matrize, die 24 Stunden am Tag, fünf Tage die Woche läuft, beträgt etwa 3.000 Einheiten pro Jahr mit einem Maximum von 80 Produkten pro Woche. Wenn die jährliche Nachfrage diesen Wert übersteigt, müssen mehrere Matrizen hergestellt werden. Durch den Einsatz mehrerer Matrizen können wir die Produktionskapazität pro Woche oder Jahr erheblich steigern und die Nachfrage decken.
Produktgröße und -komplexität
Beim Rotationsguss wird oft an größere Produkte gedacht, aber diese Technik eignet sich auch gut für kleinere Produkte. Es ist möglich, mehrere Matrizen an einem Arm zu verwenden, was eine optimale Maschinenauslastung ermöglicht. Ein weiterer Vorteil des Rotationsgusses ist die Formfreiheit; das Verfahren bietet nahezu unbegrenzte Gestaltungsmöglichkeiten. Es können hohle Formen und komplexe Konturen produziert werden, die mit anderen Methoden schwer oder unmöglich herzustellen sind. Die Formen, die durch Rotationsguss hergestellt werden können, sind nahezu unbegrenzt. Während andere Produktionsmethoden komplexe Baugruppen von Komponenten für ein komplexes Endprodukt erfordern, kann der Rotationsguss diese Baugruppe durch ein einziges einheitliches Produkt ersetzen. Diese Produktionsweise ist stabiler und kostensparend.
Verformung
Eine Herausforderung beim Rotationsguss ist die Verformung. Im Gegensatz zu anderen Gießverfahren wie dem Spritzguss wird beim Rotationsguss kein äußerer Druck ausgeübt, um das Material in die Form zu drücken. Dies führt dazu, dass das Material unkontrolliert schrumpft und sich verformt. Kunststoffmaterial neigt dazu, beim Abkühlen zu schrumpfen
; bei Polyethylen beträgt dies etwa 3 % und bei Polypropylen 2 %. Dies wird bereits in der Entwurfsphase berücksichtigt, indem die Matrizen größer als das tatsächliche Produkt gefertigt werden.
Neben dem Schrumpfen ist auch das Verziehen ein häufiges Problem. Verziehen ist die Verformung großer Flächen, die oft während des Abkühlprozesses auftritt. Während dieser Abkühlphase ist es sehr wichtig, gleichmäßig und ruhig zu kühlen. Dies verhindert Spannungen im Material, die letztlich zu verzogenen Oberflächen führen. Auch kann das Verziehen verhindert werden, indem eine möglichst gleichmäßige Wandstärke geschaffen wird. Dies fördert eine gleichmäßige Schrumpfung und reduziert die Verformung. Das Vermeiden großer, flacher Oberflächen im Entwurf kann ebenfalls helfen, Verziehen zu verhindern. Verstärkungsrippen können hinzugefügt werden, um die Steifigkeit dünnwandiger Teile zu erhöhen, ohne das Gewicht signifikant zu erhöhen. Diese Rippen können je nach Produktanforderungen hohl oder massiv sein. "Kiss-off"-Rippen, bei denen zwei Wände fast, aber nicht ganz aneinander stoßen, können ebenfalls verwendet werden, um die strukturelle Integrität zu verbessern.
Wanddicke und Gleichmäßigkeit
Ein Vorteil des Rotationsgusses ist die Möglichkeit, die Wandstärke des Endprodukts durch einfaches Hinzufügen von mehr oder weniger Material zur Form anzupassen. Die Wandstärke kann von 0,5 mm bis zu 50 mm variieren, wobei eine Gleichmäßigkeit von ±10 % möglich ist. Es ist wichtig, eine gleichmäßige Wandstärke beizubehalten, um Spannungen und Verformungen zu minimieren.
Eckenradius und Gestaltungsfreiheit
Ein wichtiger Entwurfsaspekt beim Rotationsguss ist die Verwendung abgerundeter Ecken. Abgerundete Ecken verbessern den Materialfluss während des Gussprozesses und reduzieren das Risiko von Spannungen und Brüchen im Endprodukt. Die empfohlenen Innenradien reichen von 3,2 mm bis 12,7 mm, abhängig vom verwendeten Material. Große Radien helfen auch, eine gleichmäßige Wandstärke zu erhalten und die strukturelle Integrität des Produkts zu verbessern.
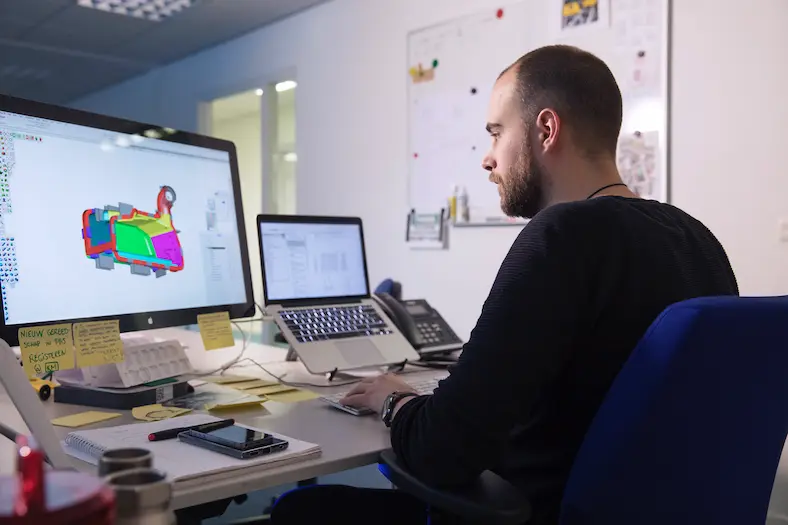
Einsätze
Das Integrieren von Einsätzen, wie Metallbuchsen und Gewinden, ist beim Rotationsguss gut möglich. Diese Einsätze können während des Gussprozesses in die Form eingebracht werden, um nahtlos in das Endprodukt integriert zu werden.
Es ist auch möglich, interne oder externe Gewinde mit zu rotieren. Allerdings ist es nicht möglich, feine Gewinde mit dieser Methode hinzuzufügen. Das Mitrotieren von Gewinden ist kostensparend, aber nicht langlebig.
Texturen
Das Finish von rotationsgegossenen Produkten kann je nach Form und verwendeten Materialien von Hochglanz bis gerippt variieren. Eine glatte, polierte Oberfläche kann teurer und zeitaufwändiger sein, bietet jedoch Vorteile wie einfache grafische Anwendung und verbesserte Ästhetik. Es ist sogar möglich, verschiedene Oberflächenstrukturen auf ein einzelnes Produkt aufzubringen.
Zusammengefasst bietet der Rotationsguss Designern enorme Freiheit und Flexibilität bei der Schaffung komplexer, hohler Kunststoffprodukte. Durch die Berücksichtigung der spezifischen Entwurfsregeln und Materialüberlegungen können hochwertige, langlebige und kostengünstige Produkte hergestellt werden. Das Verständnis der Nuancen des Rotationsgussverfahrens ist entscheidend für die Optimierung der Produktqualität und die Minimierung von Produktionsfehlern. Durch die richtige Materialauswahl, die Beachtung der Wandstärke und des Eckenradius und die Verwendung der richtigen Verstärkungsmethoden können Designer die Vorteile des Rotationsgusses maximal nutzen und innovative Lösungen schaffen, die den Anforderungen verschiedener Branchen gerecht werden. Bei Pentas arbeiten wir gerne mit unserem Ingenieurteam und dem Kunden zusammen, um diese Schritte zu durchlaufen und das beste Produkt zu entwickeln. Wir sind überzeugt, dass eine enge Zusammenarbeit und ein gründliches Verständnis des Prozesses und der Kundenanforderungen zum besten Endergebnis führen.