Het rotatiegietproces
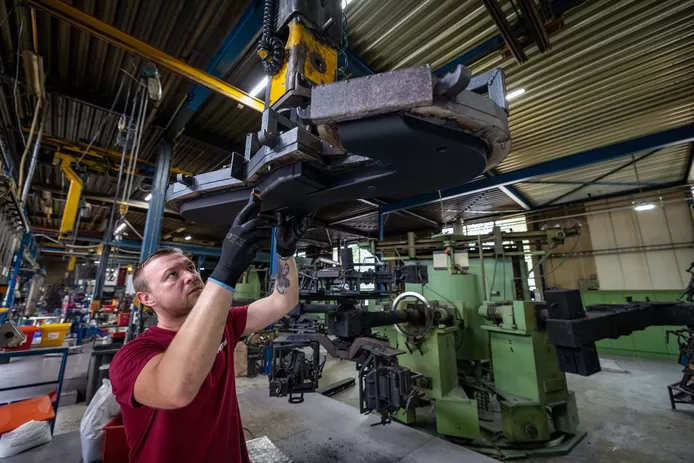
Rotatiegieten is een unieke productiemethode die wordt gebruikt om holle kunststofproducten te maken. Deze techniek is bijzonder geschikt vanwege de mogelijkheid om grote, duurzame voorwerpen met een uniforme wanddikte en complexe vormen te produceren. In dit artikel vertellen we je graag meer over de stappen die nodig zijn bij het rotatiegietproces.
Inhoudsopgave
Stap 1: Vullen van de matrijs
Het proces begint met het plaatsen en vullen van de matrijs. Vooraf afgewogen kunststofpoeder, vaak polyethyleen, wordt in de matrijs geladen. Het poeder heeft een grootte van 35 mesh, wat overeenkomt met een diameter van 74 tot 2000 micron. Het is belangrijk dat dit zo klein is omdat het warmte efficiënter absorbeert dan korrels, wat zorgt voor een snellere en gelijkmatigere smelting. De consistentie van het poeder is ook cruciaal, aangezien een gelijkmatige deeltjesgrootte en een goede stroming zorgen voor een uniforme wanddikte.
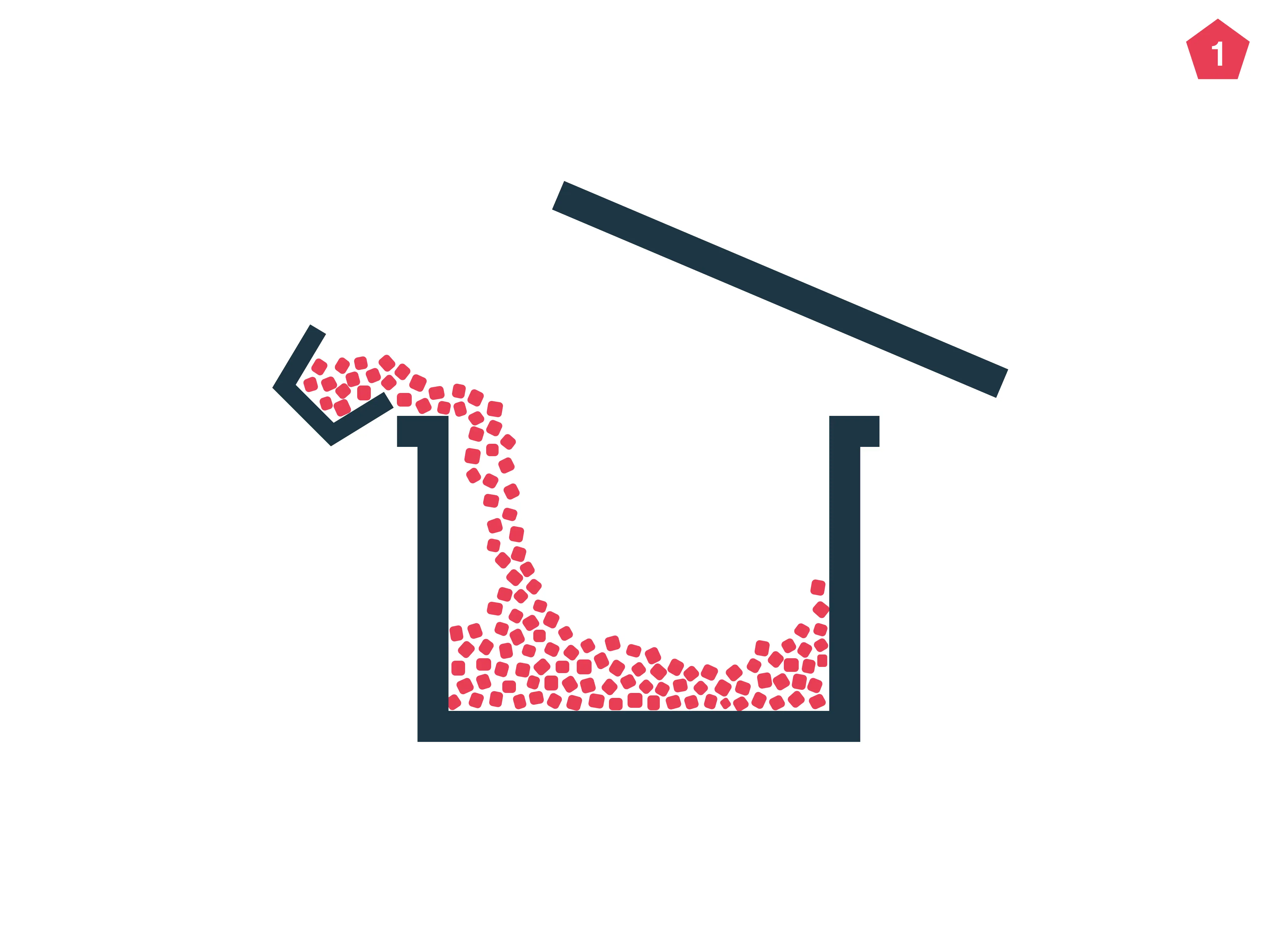
Ook wordt de binnenkant van de mal schoongemaakt en moet deze vrij van verontreinigingen zijn. Lossingsmiddelen worden vaak toegepast om het verwijderen van het afgewerkte product te vergemakkelijken en schade aan de mal te voorkomen.
Als dit allemaal gedaan is, zal de mal zorgvuldig worden gesloten. Correct sluiten is cruciaal om lekkage van poeder of lucht te voorkomen. Voor het sluiten van de mal kan gebruik worden gemaakt van handklemmen, boutverbindingen of geavanceerde automatische pneumatische klemmen.
Stap 2: Verwarmen en roterend verhitten
Zodra de matrijs gevuld is, wordt deze in een oven geplaatst die is verwarmd tot temperaturen tussen 250 en 300°C. De juiste combinatie van verwarmingstijd en temperatuur wordt vooraf berekend en is essentieel om ervoor te zorgen dat het poeder volledig smelt zonder degradatie van het materiaal. Tijdens deze fase draait de matrijs langzaam over twee assen (biaxiale rotatie, meestal 4 tot 20 omwentelingen per minuut). Deze rotatie zorgt ervoor dat het materiaal zich gelijkmatig afzet en een consistente wanddikte creëert. Het kunststofpoeder smelt en hecht zich aan het binnenoppervlak van de mal door een proces van sinteren. Er is geen externe druk, waardoor het materiaal zich gelijkmatig verspreidt en de kans op interne spanningen en defecten wordt verminderd.
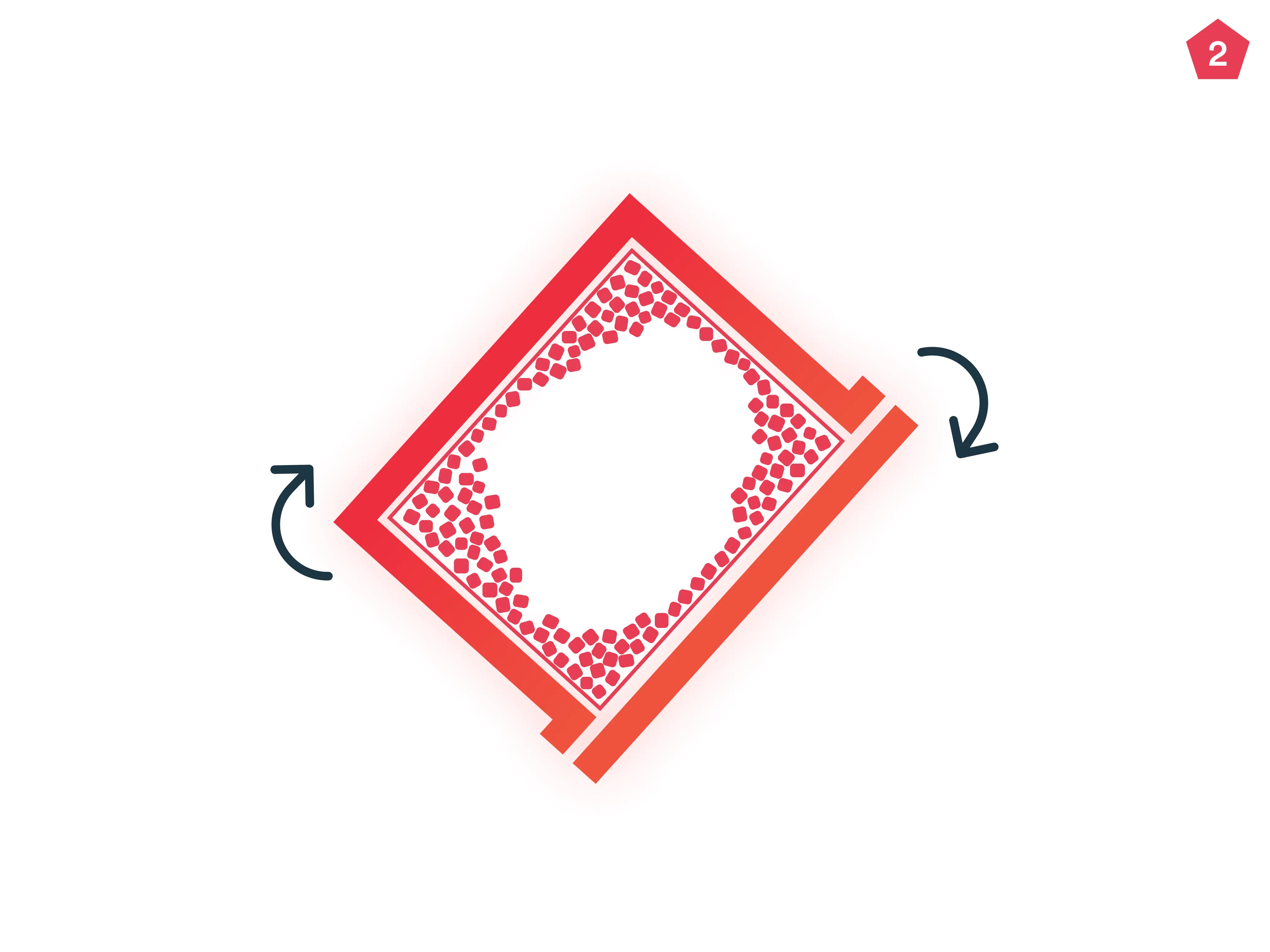
Stap 3: Koelen
Na het smelten en vormen van een uniforme laag wordt de matrijs naar een koelstation verplaatst. Hier draait de matrijs verder terwijl deze wordt gekoeld totdat deze ongeveer 70°C bereikt. Het is belangrijk dat de mal blijft roteren tijdens het koelen om een gelijkmatige krimp en afkoeling te garanderen. Dit helpt om vervormingen zoals kromtrekken en ongelijkmatige wanddikte te voorkomen. Afhankelijk van het materiaal en de vereisten van het eindproduct kan lucht- of waterkoeling worden toegepast. Luchtkoeling is meestal langzamer en meer gecontroleerd, terwijl waterkoeling sneller is maar een risico op thermische schokken met zich meebrengt. De dikte van het product heeft ook een grote invloed op de duur van het koelproces; des te dikker de wand, des te meer tijd er nodig is om te koelen. Ook is bij een dikkere wanddikte een grotere kans op vervorming van het product.
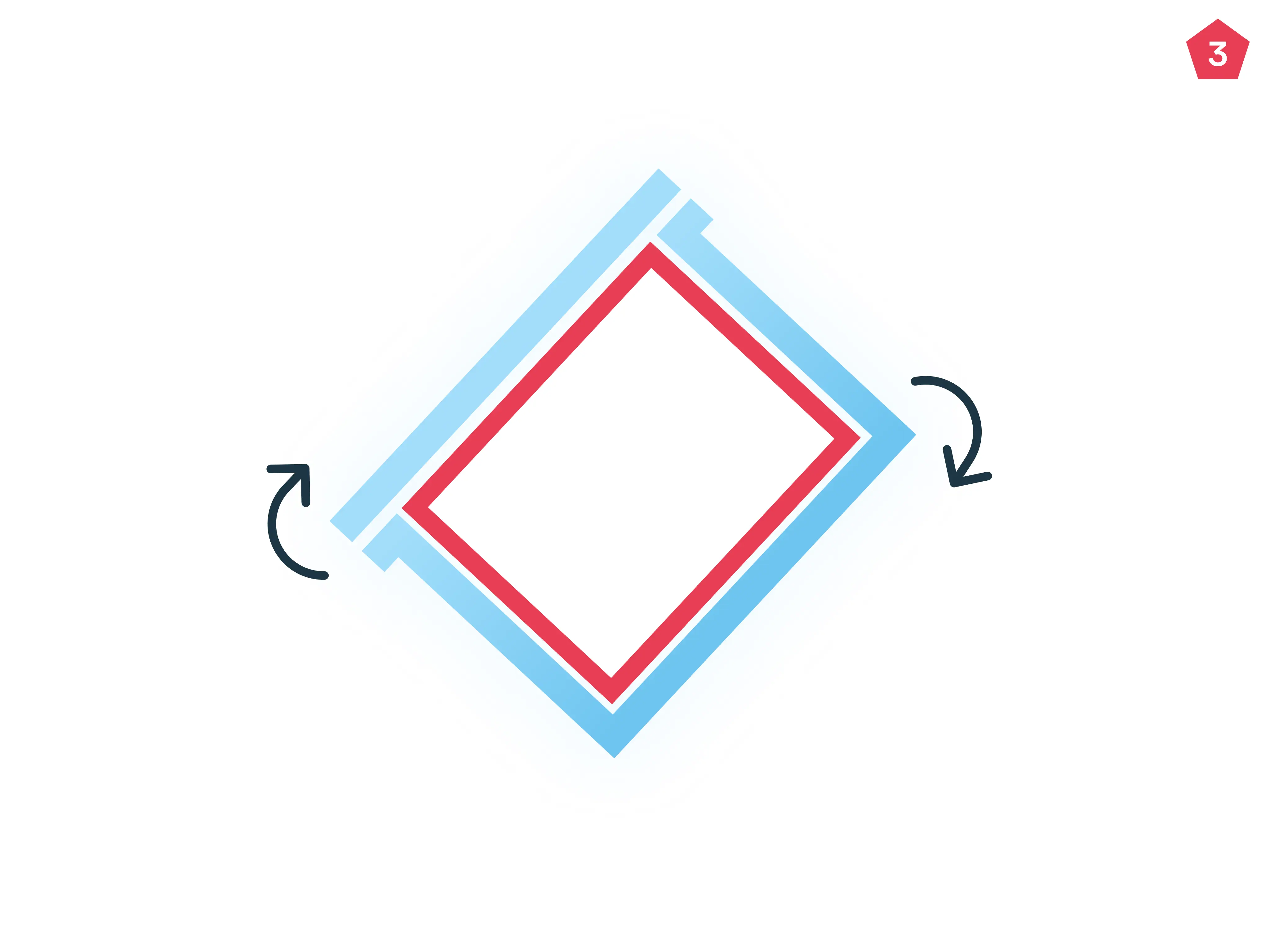
Stap 4: Uitnemen van het product
Zodra het kunststof voldoende is afgekoeld en gestold, wordt de matrijs geopend. We hebben een pneumatisch klemsysteem ontwikkeld om dit proces te versnellen. Het nieuw gevormde kunststofproduct wordt voorzichtig uit de matrijs gehaald. In deze fase is het belangrijk om zorgvuldig te werk te gaan om beschadiging van zowel het product als de mal te voorkomen. Het product wordt vervolgens geplaatst in een speciaal ontworpen steunmal om verder af te koelen. Deze steunmal helpt om de kritische afmetingen van het product te behouden terwijl het volledig afkoelt.
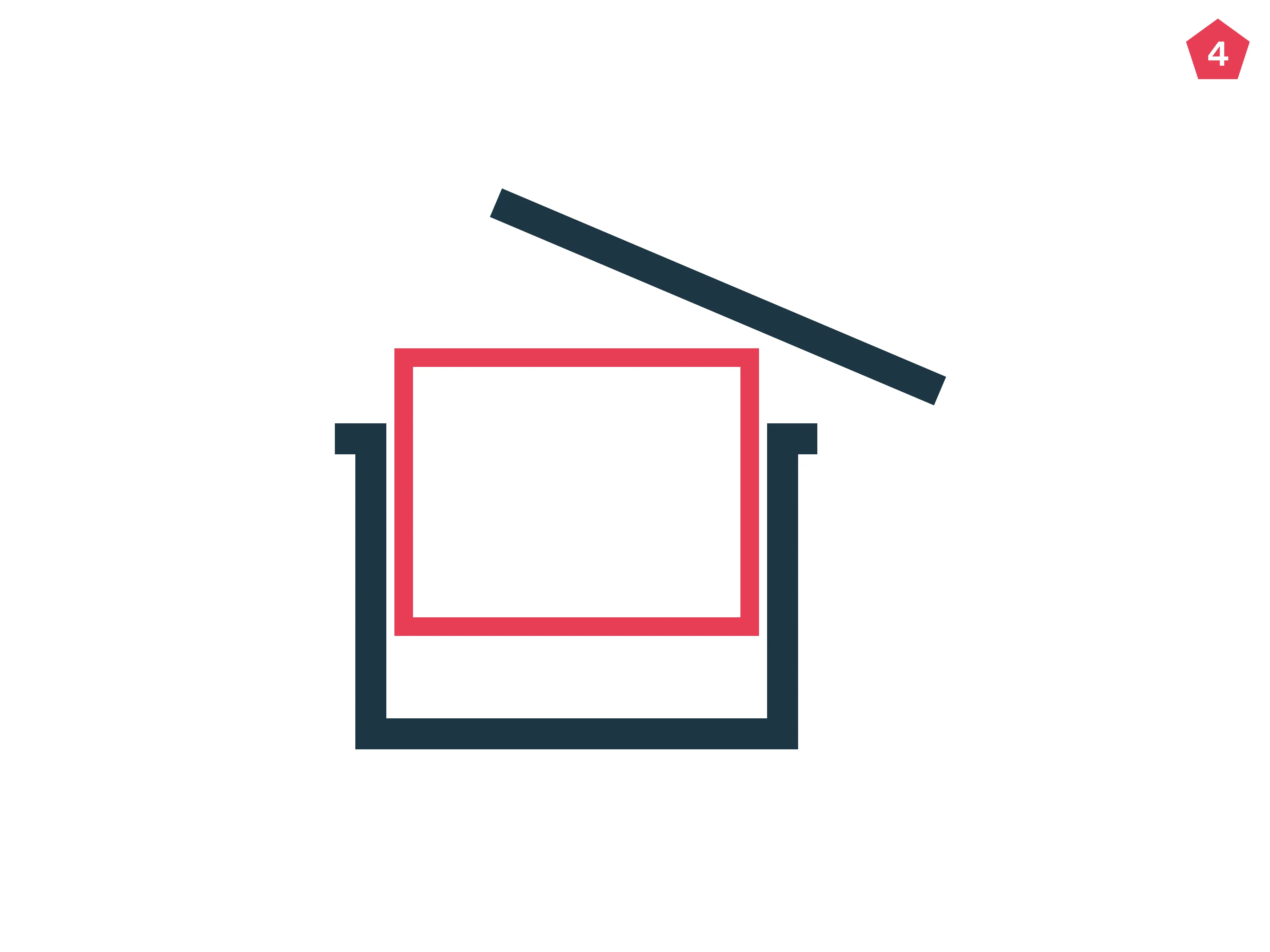
Stap 5: Voorbereiden voor de volgende cyclus
De laatste stap in de cyclus is het schoonmaken van de matrijs en het voorbereiden voor de volgende batch. Deze voorbereiding omvat het inspecteren van de matrijs op eventuele residuen of onvolkomenheden en het opnieuw aanbrengen van eventuele lossingsmiddelen. Bij continue operatie kan deze cyclus 24 uur per dag, vijf dagen per week draaien, wat de productiviteit maximaliseert.
Rotatiegieten is een veelzijdig en efficiënt proces voor het vervaardigen van een breed scala aan holle kunststofproducten. Van het nauwkeurig vullen van matrijzen tot het gecontroleerd koelen en voorzichtig verwijderen van het product, elke stap is ontworpen om een hoge kwaliteit en consistente output te garanderen. Zo kunnen we betrouwbare en duurzame producten leveren voor diverse toepassingen.