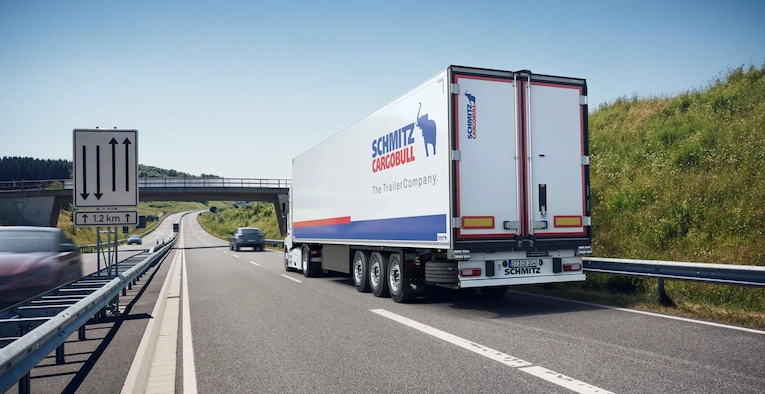
Collaboration
Innovative Air Duct for Schmitz CargobullThe possibilities of plastic rotational molding are virtually limitless. From robust fuel tanks for agricultural machinery and advanced slosh dampers for wind turbines to durable toilet cabins – the bigger the challenge, the better. It requires deep technical knowledge and a bold approach to create solutions that are ready for the future. At Pentas, we have the expertise and resources to tackle any challenge and deliver innovative, future-proof solutions.
The unique rotational moulding process of PentasWhat is rotational moulding?With nearly 50 years of experience and more than 700 different plastic products, our process runs like a well-oiled machine. We can manufacture items up to a diameter of 2,500 mm and a length of 4,000 mm. Do you want to challenge us?
Looking for more information about Pentas and rotomoulding? Use the table of contents to navigate to the topic.
Table of contents
At Pentas, our team of 150 people is passionate about technology. There’s always someone who thinks things can be more efficient. We encourage that thinking and are not afraid to make fundamental changes, but only if it leads to more efficient operations, benefiting our customers.
Using FMEA, we prevent design errors, and our ERP systems track the product throughout the entire process. We continuously monitor quality during production. If there’s a deviation from the drawing, we solve it at the source. It’s no wonder we are ISO 9001 certified.
We are highly driven to produce as sustainably as possible, continuously monitoring the environmental performance of our processes. Almost all waste streams are reused. We continuously innovate to make our products stronger, lighter, and more sustainable.
In order to define the development, it is important to draft a Programme of Requirements (PoR) that your product will have to meet.
The concept focuses on integrating functions and producibility as a plastic rotational moulding product. This phase results in the delivery of one or multiple concepts with a motivation and testing of the concepts against the PoR as well as a substantiation with design sketches.
A risk analysis will be conducted in consultation with yourself. We will test whether the choice of material is suitable for your requirements.
Detailing of the plastic rotational moulding product is an important phase before we can proceed with mould construction and automation.
Based on your final 2D and 3D CAD drawings of the plastic rotational moulding product, Pentas will start development and mould construction.
Before Pentas takes your plastic rotational moulding product into mass production, the product and the process will have to be approved.
This extension of the production of your plastic rotational moulding product requires associated steps to validate the process
At Pentas, we take pride in our long-term collaborations with various customers. These sustainable relationships form the foundation of our success. Together with our clients, we strive for innovation and excellence, offering tailored solutions that meet their needs perfectly. These close partnerships allow us to grow and deliver innovative rotational moulding solutions that meet the highest standards.
Collaboration
Innovative Air Duct for Schmitz CargobullCollaboration
Lighter tank saves fuelRotational moulding (Rotomoulding) is a thermal forming process used to create hollow plastic components. The process involves filling a mould with fine plastic powder, heating it, and rotating the mould around two perpendicular axes. The powder melts and adheres evenly to the inside of the mould, resulting in a uniform wall thickness and minimal stress in the final product. After heating, the mould is cooled, and the finished component is easily removed from the mould without further processing.
Rotational moulding is a versatile and innovative technique used to manufacture hollow, seamless plastic products. It is renowned for its ability to produce complex and large shapes with consistent wall thickness and minimal stress.
Rotational moulding
The production and product process at PentasRotational moulding
The foaming of rotationally moulded productsRotational moulding
The rotational moulding processRotational moulding
The future of rotational mouldingRotational moulding
Materials for Rotational MouldingRotational moulding
Design rules for rotational mouldingWe have years of experience in designing and producing high-quality moulds that form the foundation of our innovative rotational moulding processes. Every mould we create is carefully tailored to the specific requirements of our customers, resulting in products of exceptional quality. With our expertise in moulds and rotational moulding, we continuously set new standards in the industry.
At Pentas, we serve a wide range of markets with our expertise in rotational moulding. Our products find their way into various sectors, including construction, agriculture, automotive, and consumer products. Our flexibility and technical know-how enable us to provide customised solutions for every market we serve.
Markets
Surprising designs and applications of rotomoulded productsRotomoulding is a versatile production method that stands out due to its design freedom and low investment costs. Thanks to technological advancements and clever product design, more and more innovative applications are emerging. In this blog, we highlight several striking examples from the sector that underline the strength and possibilities of rotomoulding.
Markets
Rotational moulding in the transport sector: innovative plastic solutionsThe transport sector demands robust, lightweight, and durable products that can be efficiently manufactured. Rotational moulding (rotomoulding) is a plastic manufacturing technique that meets these requirements well. It enables the production of seamless, hollow products by rotating plastic powder in a heated mould so that it evenly hardens against the mould wall. Rotational moulding offers a combination of design freedom and cost efficiency for volumes of several hundred units per year, which other methods struggle to match. From logistic packaging to fuel tanks and from wheel arches to interior parts: rotationally moulded components are used in road transport, logistics, agricultural machinery, railways, and mobility infrastructure.
Markets
Rotational moulding in the defence industryThe defence industry is under pressure to find robust, reliable, and innovative production solutions. Whether it concerns vehicles, equipment or logistical resources, defence requires products that can withstand extreme conditions and be delivered on short notice. Plastic products made through rotational moulding offer a unique solution. The technique combines design freedom and flexibility of shape with high impact resistance and local production capacity. This allows for a quick response to new demands and developments.
Markets
Surprising designs and innovative applications of rotational moulding productsThe rotational moulding industry is constantly evolving through new technologies and creative designs. In this blog, we showcase some innovative applications that highlight the versatility and power of rotational moulding. Think, for example, of street furniture or watersport products. This technique proves its value across various sectors.
Markets
Rotomoulded packaging materialRotational moulding is a versatile manufacturing technique that can also be applied in the production of packaging. This technique is particularly suited for creating hollow products, making it ideal for packaging materials such as plastic pallets, storage tanks, transport and storage containers, IBC containers (Intermediate Bulk Containers), and plastic barrels and drums. In this article, we will discuss the various applications and advantages of rotomoulded packaging materials.
Markets
More than a thousand products: The versatility of rotational mouldingAt Pentas, we take pride in the wide range of products we can manufacture using our rotational moulding process. Rotational moulding is an extremely versatile technique used in numerous markets and countries. Our products range in weight from 500 grams to 100 kilograms, and the applications are just as diverse. Whether it’s urinals for events, fuel tanks for agricultural machinery, buoys at sea, or water tanks in campers – our production currently exceeds a thousand unique products.
Quality is at the heart of everything we do. We only deliver products that meet the highest standards. Every part we produce undergoes strict inspections to ensure it meets the specific requirements of our customers. We use advanced technologies and tightly controlled production processes to ensure consistency and precision.
Innovation is the foundation of our success stories. We continuously strive to push the boundaries of what is possible in rotational moulding. By integrating the latest technologies and creative solutions, we remain at the forefront of the industry. Our teams work closely together to develop innovative designs that meet the specific needs of our customers. From concept to production, we are constantly exploring and implementing new materials and techniques to make products more efficient, sustainable, and functional.
Innovation
Robots and AI with a human face: Pentas' visionWe envision a factory where robots and humans work side by side. This might sound futuristic, but at Pentas, we've been working daily to realize this vision since 1995. Over the years, one thing has become crystal clear: at Pentas, technology is never meant to replace people, but to support and empower them.
Innovation
3D printers for innovation and efficiencyAt Pentas, we use innovative technologies to enhance our rotational moulding process and deliver complex products with consistent quality. One of the tools we use is our 3D printers. In this blog, we explain how 3D printing helps optimize our processes and maintain the high-quality standards our customers expect.
Innovation
Innovation in knowledge retention: The role of augmented realityWithin the manufacturing industry, we face a crucial challenge: retaining our expertise. In collaboration with Saxion University of Applied Sciences, the University of Twente, and other partners, we are making a significant step forward by integrating augmented reality (AR) into our processes. This initiative aims to capture and transfer essential knowledge within our organization.
Innovation
Handyscan 3D Max: Precision in production, mold making, and quality controlAt the beginning of this year, we at Pentas made a technological leap by integrating the Handyscan 3D Max into our operational processes, achieved with the expert support of EMS Benelux. This state-of-the-art 3D scanner, which excels with an accuracy of up to 0.15 mm, is crucial for delivering demanding products to customers.
Innovation
New innovative manufacturing process brings ideas into shape even more effectivelyPentas Moulding B.V. relies on state-of-the-art milling technology from Fooke and saves 50% of the machining time in the production of aluminum moulds.
Innovation
Pentas continues to expand its machineryWe will receive and install a new rotational moulding machine from Reinhardt. This will be an expansion of our existing machinery.
We are committed to sustainable production by continuously monitoring the environmental impact of our processes. Almost all of our waste streams are reused. In addition, we continue to innovate to make our products stronger, lighter, and more environmentally friendly.
Sustainability
Solar Panels at Pentas: Four Years LaterSustainability
Saving energy at the drawing boardAt Pentas, everything revolves around dedication and craftsmanship in rotational moulding. As a leading specialist in the industry, we offer innovative and customized solutions for a wide range of applications. With decades of experience and deep technical expertise, we have built a reputation for delivering high-quality products that meet the strict requirements of our customers.
Pentas
Pentas Moulding named Next Icon 2025We are proud to share that Pentas Moulding has been named Next Icon 2025. During the fourth edition of Next Icons, held on Wednesday, May 21 in Enschede, we were given a valuable platform to showcase what we stand for as a manufacturer of plastic products: customization, innovation, and the smart use of technology.
Pentas
Pentas shares AI experiences at international IT-RO trade fair in ItalyInnovation within the Rotationsguss industry often stems from collaboration and knowledge sharing. Companies in our sector regularly exchange hands-on experiences and share insights on new techniques and technologies. One of the key trends today is the application of artificial intelligence (AI) and automation in the production process. At Pentas, we’ve been leading in this field for two years now, and we recently shared our experiences at the international IT-RO trade fair in Italy.
Pentas
Pentas recognised as a sponsor by the INDPentas Moulding has been officially recognised as a sponsor by the Immigration and Naturalisation Service (IND). This means that the IND considers us a reliable partner for attracting international talent and that we are allowed to use fast-track procedures to apply for residence permits for foreign employees, researchers, and interns. In this blog, we explain what this recognition entails, the benefits and responsibilities that come with it, and what it means in concrete terms for Pentas.
Pentas
Visit of Erwin Hoogland to Pentas for the INDUSTR_I4.0 programOn December 13, 2024, we welcomed deputy Erwin Hoogland from the province of Overijssel. Pentas is the first company in Overijssel to receive a grant under the INDUSTR_I4.0 program, marking a significant milestone. In this blog, you’ll discover more about the program and how Pentas is leveraging AI technology to transform production processes.
Pentas
Knowledge exchange during the Rototour 2024The past two weeks were entirely focused on knowledge exchange and strengthening the rotational moulding industry. During the Rototour 2024 in Brazil, rotational moulders from around the world gathered to share ideas and visit local moulders. In this article, we share our key insights and experiences from this intensive and inspiring journey full of valuable encounters.
Pentas
Which rotational moulding machines do we have?At Pentas, we use various rotational moulding machines to meet the diverse needs of our customers. Our facility is equipped with 10 carousel machines and 1 advanced Rock and Roll machine, together providing a wide range of production capabilities.
Rotational moulding is a manufacturing process used to create hollow plastic parts. In this process, a mould, also known as a die, is filled with plastic powder. The mould is then heated while being rotated on two axes. This ensures that the material melts and evenly coats the inside of the mould, resulting in a strong, seamless part. After that, the mould is moved to a cooling station, where it continues to rotate while being cooled, allowing the plastic inside to harden. The final step occurs at the demoulding station, where the mould is opened and the hollow product is removed. From here, the process begins again.
Polyethylene (PE) is the most commonly used material in rotational moulding due to its versatility, cost-effectiveness, and excellent processability. PE has a wide melting range, making it ideal for rotational moulding as it allows for even melting and good flow during the moulding process. Additionally, PE offers excellent properties such as chemical resistance, durability, and flexibility, making it suitable for a wide range of products.
In addition to PE, other materials can be used, such as polypropylene (PP), nylon (PA), polycarbonate (PC), and PVC. Within these plastic groups, there are different variants, each with unique properties such as color, impact resistance, and aging resistance.
Rotational moulding offers several advantages, including low investment costs for moulds and tools, leading to low production costs for small to medium runs, up to tens of thousands per year. It allows for the creation of complex and large shapes, ensures uniform wall thickness, and results in minimal material waste. Additionally, hollow and fully enclosed parts can be easily produced.
The wall thickness of a rotationally moulded part is crucial for both its strength and cost. Thicker walls increase the strength and durability of the product but also raise material costs. It is important to determine the optimal wall thickness to meet functional requirements without incurring unnecessary expenses. A smart product design, based on how the product will be used, can help optimize this. By incorporating ribs or kiss-offs, the forces exerted on the product can be better distributed, reducing the need for excess wall thickness or material.
Problems such as warping, poor impact resistance, and uneven wall thickness can occur during the rotational moulding process. These issues can often be resolved by adjusting the process, such as optimizing heating and cooling times, or by selecting more suitable materials and additives.
When designing rotationally moulded products, it is important to avoid sharp corners, ensure uniform wall thickness, and place inserts and ribs strategically for added strength. This helps reduce stress and improves the durability and reliability of the final product.
Material selection is critical because it determines the processing parameters, mechanical properties, and chemical resistance of the final product. It is essential to choose a material that is suitable for the specific application and environmental conditions.
Rotational moulding is used in a wide range of applications, including water tanks, air ducts, containers/packaging, and industrial housings. The process is particularly suitable for producing large, complex, and hollow parts.
Moulds for rotational moulding must withstand high temperatures and have a non-porous surface to ensure a smooth final product. They should also be designed for easy opening to remove the moulded part without damage. Over time, design changes may be necessary, and if the mould is of high quality, these changes can be incorporated into the existing mould, saving costs by avoiding the need for a new mould.