From idea to product, here is how rotational moulding works
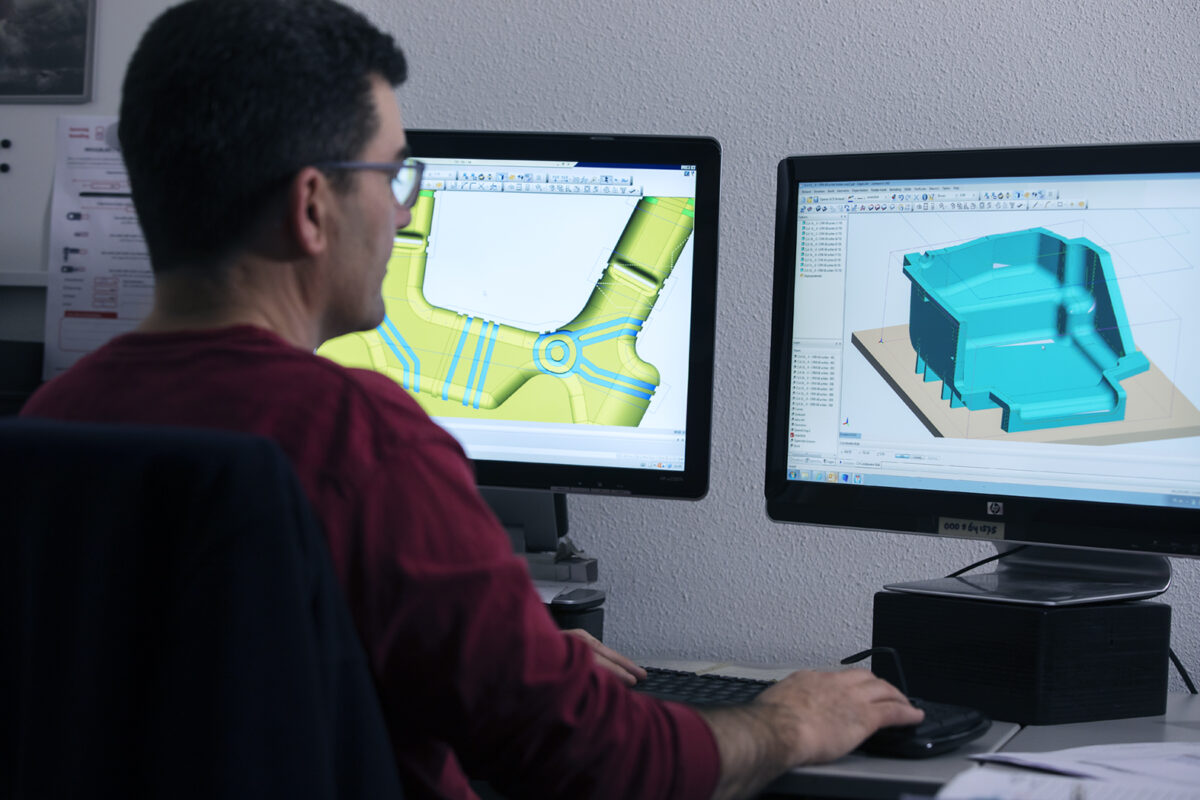
Every product starts as an idea. But the road from idea to a production-ready product is a speciality. Our speciality. At Pentas Moulding, we have a lot of knowledge and experience in this regard. Once the product is ready for mass production, we can produce and deliver it by order. We will clarify the process below in several steps.
From design to finish
Whether it be fuel tanks, flower pots, mudguards or toys: all plastic products by Pentas are made in a similar way. The shape, dimensions and colour may differ but the steps we take are always the same. From design to rotational moulding and from assembly/finish to transport.
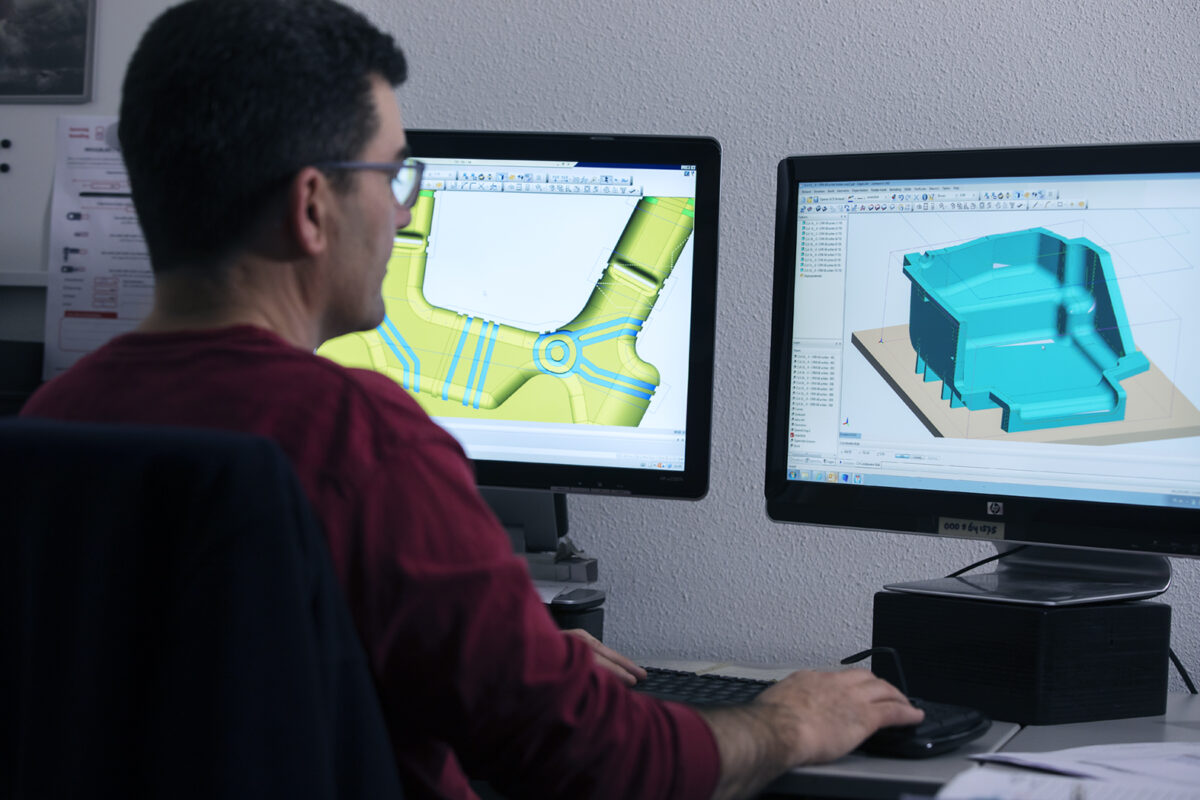
The design
The design is the foundation of any product. In consultation with yourself, our client, we create the optimal design. We hear your wishes and requirements and analyse the entire assembly environment of the product. We consider all of this in the context of the possibilities and limitations of the rotational moulding process and are happy to share our many years of experience with you to avoid any pitfalls.
Within the predetermined framework, our builders optimise the design for the rotational moulding process. Product design is not just about the shape of the plastic product, but also about its application. We install parts into the product routinely, such as level gauges, caps, hoses, etc. Our extensive supplier network allows us to rely on a wide range of this type of assembly parts. But that is not all. Our builders are also responsible for designing the production mould which is then produced at our own mould construction department.
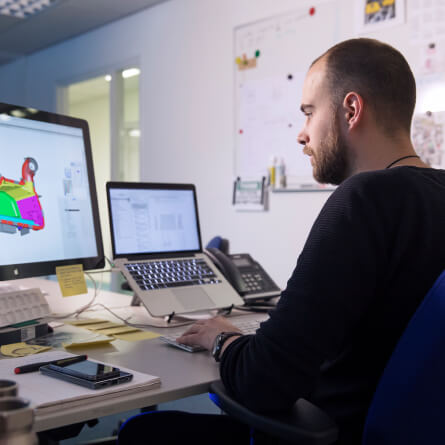
The mould
Once we know the dimensions and shape of the product, we will build a production mould. This mould is used to make countless exact copies of your product. Once the series is completed, we store the mould at our warehouse for your next order.
Pentas only uses CNC moulds in order to guarantee products of the highest possible quality. Benefits include close tolerances, proper wall thickness distribution and tight division seams. In addition, CNC moulds are relatively easy to adjust should any design changes prove necessary.
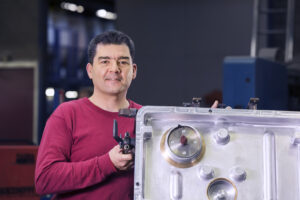
Rotational moulding
We fill the mould with plastic powder and heat it until the powder, now a liquid mass, sticks to the hot mould wall. Next, the product is cooled at our cooling station. In order to ensure proper wall thickness distribution, the mould is rotated on two arms throughout the entire process. In the final step, the set product is removed from the mould which is filled with a new batch of powder for the next cycle.
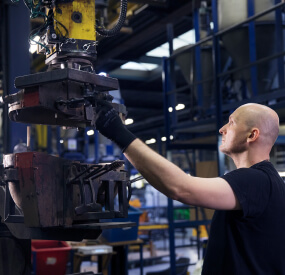
Finish
Our professional technical staff finish the product. Based on specific post-processing instructions available on the production line in digital form, the product is finished. During the design phase, we take a critical look at this entire process. Support moulds, gauges and measuring equipment are designed in advance for critical dimensions or important shapes. We also consider what may go wrong in our production/post-processing process in advance and anticipate this by developing ‘Poka-Yoke’ solutions.
As a system supplier, we deliver more than the plastic product alone. We install assembly parts as well to deliver semi-finished products. This means your product is delivered ready-made and completely assembled. To enable all of this, we manage stock parts and supplier relationships ourselves.
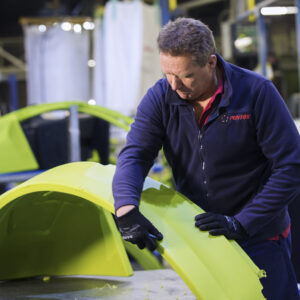
Quality assurance
Pentas puts quality first. We go all out in order to meet the agreements made with our client and the expected quality. One way of doing this is by conducting thorough quality inspections. Quality assurance staff go around our factory with tablets taking samples from our production series. Drawings with tolerances are compared to the actual product. In the event of any deviations, we will investigate the cause and solve the problem at the source. Every individual product must meet all of the client’s predetermined requirements and thanks to our thorough inspections, we make sure it does.
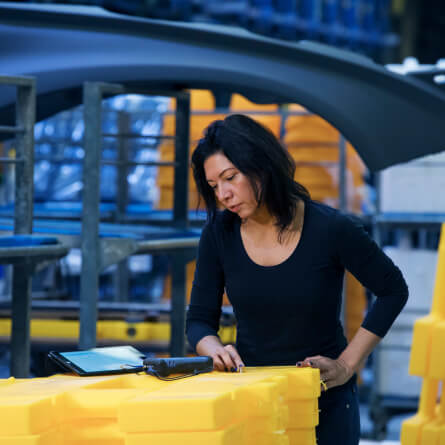
Transport
If your organisation does not have its own transport department, we can have your product delivered to the desired location. We do this in collaboration with professional carriers in the region. We are well versed in logistic techniques such as Just-In-Time and Just-In-Sequence and work with them on a daily basis.
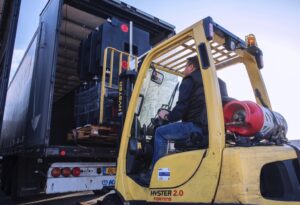
Curious about the possibilities of rotational moulding?
Contact us and we will be happy to tell you more. Whatever your question may be, we will be able to help you.