Handyscan 3D Max: Precision in production, mold making, and quality control
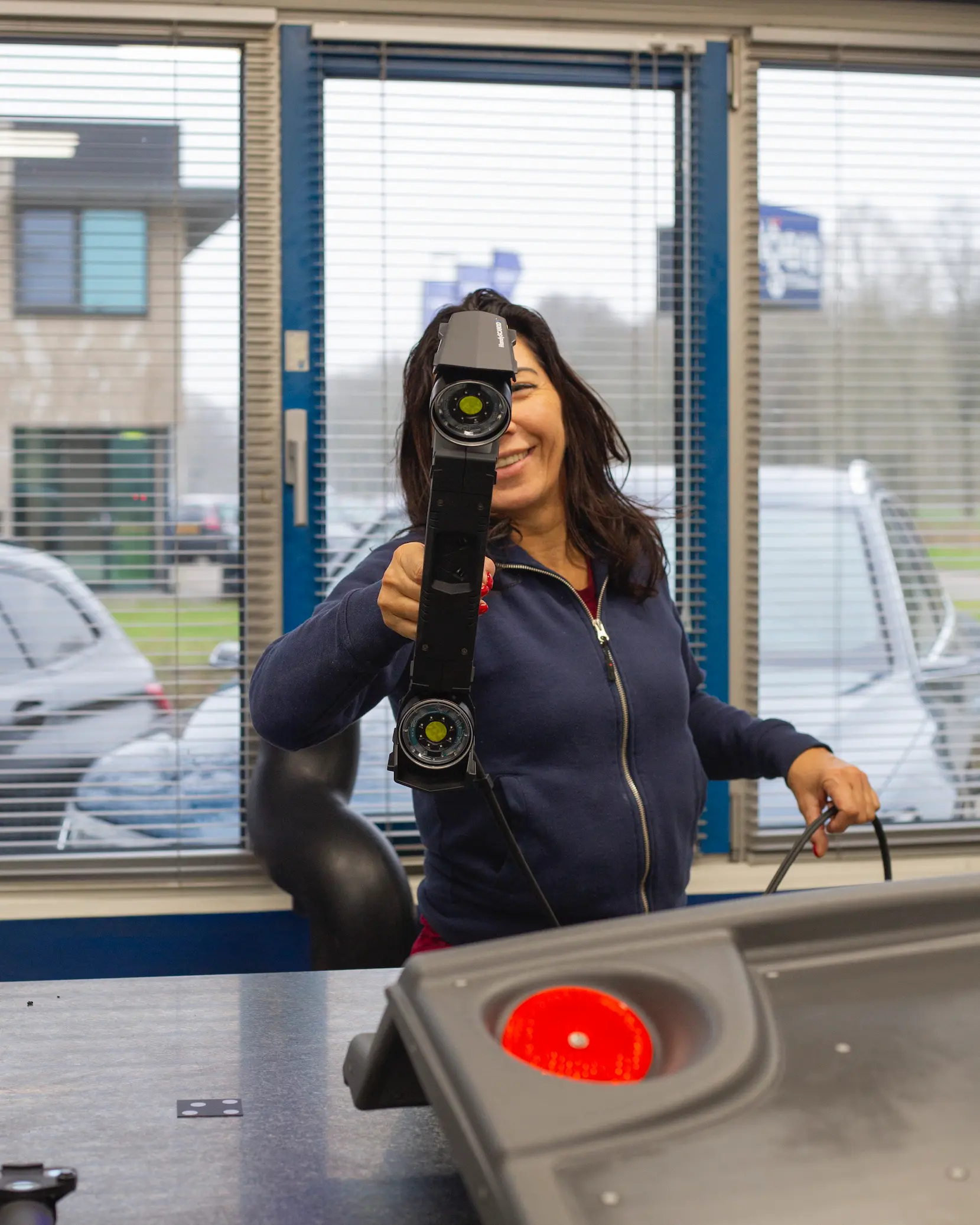
At the beginning of this year, we at Pentas made a technological leap by integrating the Handyscan 3D Max into our operational processes, achieved with the expert support of EMS Benelux. This state-of-the-art 3D scanner, which excels with an accuracy of up to 0.15 mm, is crucial for delivering demanding products to customers. It offers us the ability to digitize complex objects with unprecedented speed and precision, a crucial factor for maintaining, among other things, our production quality.
The 3D scanner is used for various tasks:
First Product Inspection (Erstmuster Prüfung - EMP): Recording and validating new product developments
Within our quality assurance process, the First Product Inspection plays a crucial role. This procedure starts with the careful recording of the very first product that comes out of a newly manufactured mold, which we can now do very precisely using the 3D scanner. This initial product is then digitally analyzed to ensure that it meets all our strict quality standards.
After approval, this first product inspection is documented and stored as an important reference point that can be used in quality control.

Quality Control: ensuring consistency and quality
In serial production, products will periodically be rescanned and compared with the original reference point stored in a 3D model. Possible deviations can then be easily observed and adjusted. This method allows us to monitor and ensure the consistency of our products, assuring a high standard of process control and product quality.
Reverse Engineering: copying and reproducing machine parts
Our technical department also uses this technology for reverse engineering purposes. This allows us to digitize machine parts with high precision, after which exact replicas can be produced. This is particularly useful for machine parts whose original design drawings are no longer available. By this approach, we can extend the life of production equipment and reduce dependency on external suppliers.
Natural product surfaces: development of surface structures on molds
The use of the 3D scanner also offers possibilities in the design of molds, especially for products that need a natural appearance such as that of walls, sand, or tree bark. Using the scanner, we can digitize these surfaces and use them in the 3D drawings of the mold. This process results in end products with authentic textures that mimic the natural look. This technical approach enables us to develop products that look and feel authentically natural, delivering tangible quality.
Dinand from the quality service at Pentas shares his experiences with the transition to the 3D scanner:
"In the past, we relied on traditional measuring tools such as calipers or rulers for measuring our products. These methods were sufficient for simple geometries, but they presented challenges when measuring complex designs, especially concerning curves. With this 3D scanner, that has really changed. By applying reference stickers to the product and then scanning it, we can now quickly and efficiently generate a digital 3D model. This model shows any deviations from the original design with high precision, taking our quality control to a higher level.”
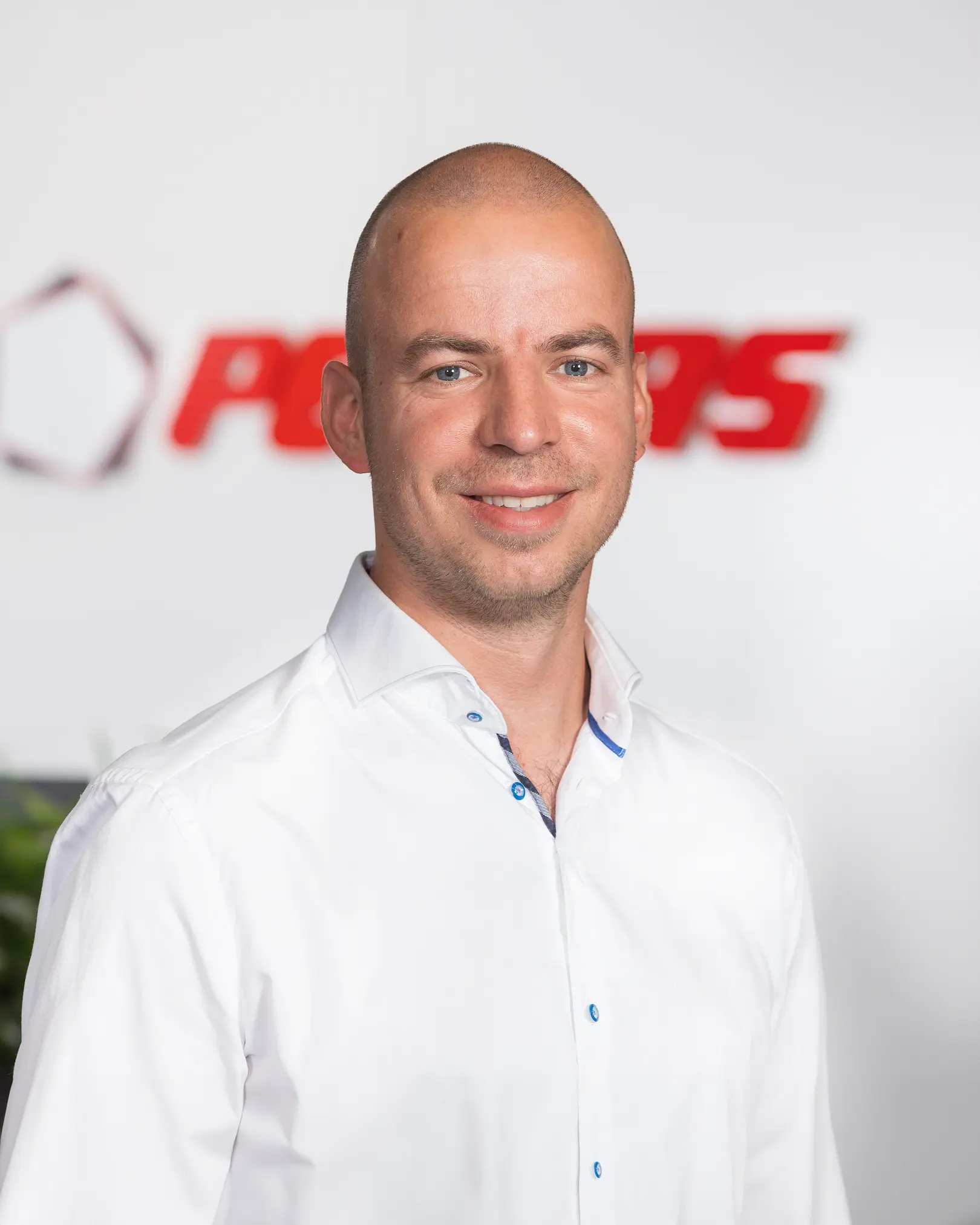
The introduction of the Handyscan 3D Max into our production process marks a significant step forward in our approach to quality and precision. This decision underscores our ongoing commitment to integrating technological advancements and being prepared for the future.