Rotational moulding in the defence industry
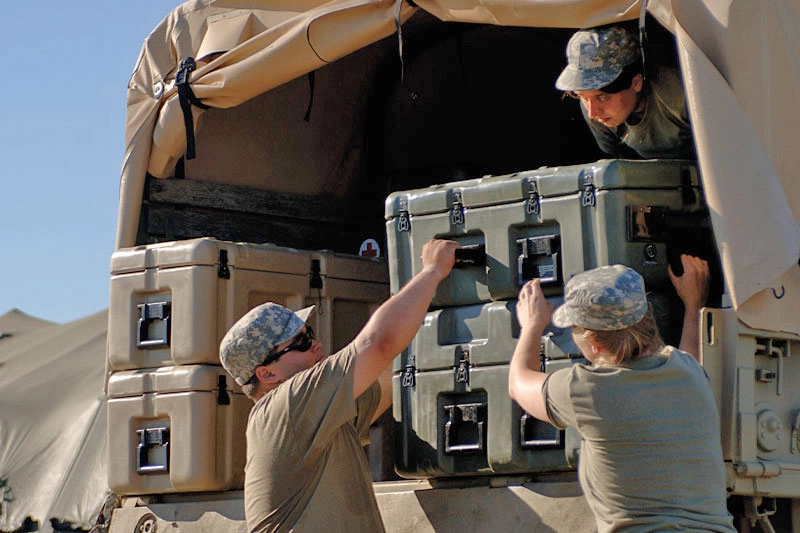
The defence industry is under pressure to find robust, reliable, and innovative production solutions. Whether it concerns vehicles, equipment or logistical resources, defence requires products that can withstand extreme conditions and be delivered on short notice. Plastic products made through rotational moulding offer a unique solution. The technique combines design freedom and flexibility of shape with high impact resistance and local production capacity. This allows for a quick response to new demands and developments.
Table of contents
Unique advantages of rotational moulding for defence applications
Rotational moulding (also known as rotomoulding) is a production process in which plastic powder is heated and rotated in a mould, so that the material melts and evenly deposits against the wall of the mould. The result is a seamless hollow product made in one piece. This way of producing brings several advantages that are particularly relevant for defence.
Shape and design freedom
Complex hollow shapes that are difficult to produce using other techniques can be relatively easily realised with rotational moulding. A rotationally moulded component has a consistent wall thickness and can be made single- or double-walled as desired. This means maximum design freedom to develop a product precisely tailored to the application, including undercut details or integrated reinforcements that are not feasible with injection moulding or thermoforming. Inserts (for example, metal bolt sleeves or thread) can also be easily moulded in during the process, so that mounting points or fastenings are directly integrated into the product.
Robustness and impact resistance
Rotationally moulded products are extremely strong and can take a beating. Because products are seamless and made in one piece, there are no weak spots or weld seams. Materials such as polyethylene (PE) also have naturally high toughness. As a result, rotationally moulded parts can withstand heavy loads and rough handling. This is essential for military use. Think of falls, shocks during transport or impacts from flying debris. A rotationally moulded housing or tank remains intact where a traditional material would deform or crack. Plastic fenders made via rotational moulding are, for example, much more resistant to denting or bending than steel variants, and they do not rust. Moreover, these plastics retain their shape and properties under various temperatures and UV radiation.
Local and flexible production
The investment in a rotational moulding mould is relatively low and the development time is short (a few weeks for a new mould). This makes it feasible to set up local production for specialised defence parts, without dependence on distant supply chains. At Pentas, moulds are designed and made in-house, ensuring fast iteration and confidentiality. The method is also suitable for smaller series or prototypes. Production is cost-effective from about 300 units per year. For the defence industry, where mass production is often not the norm but custom solutions in limited numbers, this flexibility is a major advantage. It means that innovative ideas can quickly be turned into physical products that can be tested and deployed.
Applications of rotational moulding within defence
Fuel tanks for military vehicles
Plastic fuel tanks are ideal for military vehicles due to their low weight, robust character and shape flexibility. Thanks to rotational moulding, these tanks can be designed to fit precisely within the available space of a vehicle. The result is a seamless, impact-resistant product in which connectors and sensor housings are directly integrated, without welds or adhesive joints that could leak.
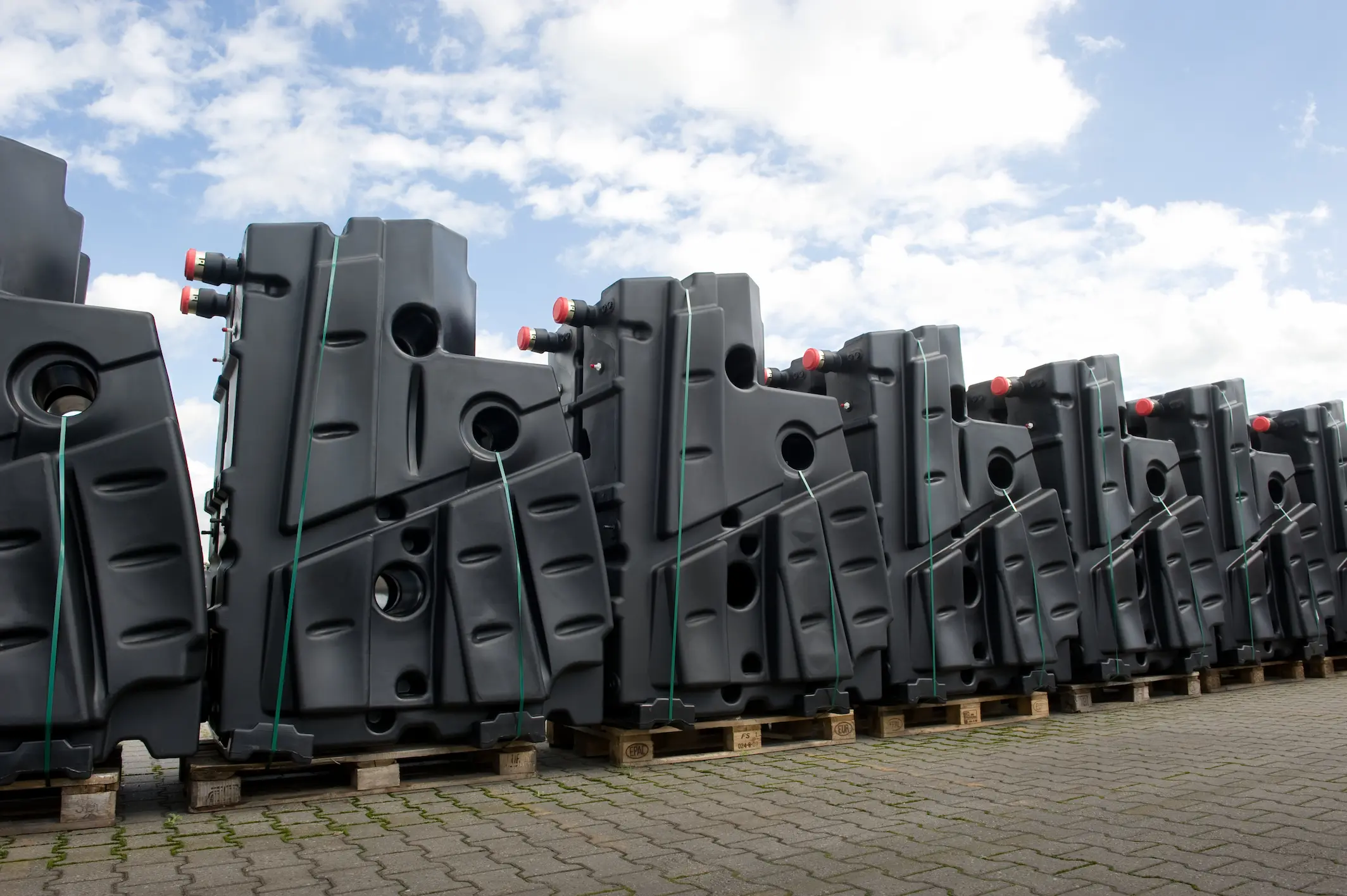
Polyethylene tanks are flexible and can handle impact better than traditional metal variants. In an accident or explosion, a flexible plastic tank is less likely to crack or rupture than a metal one. The US army already experimented in the 1970s with rotationally moulded polyethylene tanks to improve impact resistance. Moreover, the tanks are immune to corrosion and can be chemically optimised for various fuel types such as petrol, diesel and kerosene. Barrier materials limit vapour emissions and make the tanks suitable for stringent environmental standards such as CARB or EPA.
A plastic fuel tank can be dozens of percent lighter than a steel equivalent with the same volume. This reduced weight translates into additional load capacity or range for the vehicle. Of course, plastic fuel tanks must meet inspections, for example TÜV certification for use on public roads or internal military standards. Pentas has experience with this, with fuel tanks that have passed fire tests, drop tests and impact tests as required.
Drinking water tanks and liquid reservoirs
In addition to fuel, drinking water is important in operations. Plastic water tanks offer safe storage for drinking water. Since the inside of the tank consists of inert polyethylene, no flavours or chemicals leach into the water. Special food-grade plastics can also be used, which are certified for drinking water contact.
Rotationally moulded water tanks have similar advantages as fuel tanks. They are seamless, lightweight and extremely robust. The tanks can hold volumes up to 13,000 litres while maintaining shape. In a military context, the volumes are often smaller, but the principle is the same. The tanks are easy to transport, optionally equipped with integrated handles in the design.
A water tank that stands in the sun should not encourage algae growth or contaminate the water. By adding UV stabilisers to the plastic, the tank remains usable in sunlight for years without degradation.
Covers and fenders for defence vehicles
In addition to tanks, covers and fenders of off-road vehicles, armoured vehicles or support equipment are increasingly being made from plastic using rotational moulding. Where many of these parts used to be metal, plastic now offers several advantages.
Fenders and covers are exposed to water, mud, sand and various weather conditions. Steel or aluminium must be well treated to avoid corrosion. Plastic, on the other hand, is naturally resistant to rust. Especially for vehicles that are operational outdoors for long periods, this material durability is a great asset.
Moreover, rotationally moulded covers can be shaped specifically to the customer. They can precisely follow the contours of a vehicle and be equipped with integrated mounting points, ribs or cutouts for lights and hatches. For example, a fender can be designed with locally thicker areas for extra strength where needed, while saving weight elsewhere. Thanks to rotational moulding, a part is created without seams that doesn’t rattle or come loose due to vibrations. A plastic fender flexes on impact, where a metal one would dent.
Insulated storage boxes for medicines
To safely transport temperature-sensitive items such as medicines, vaccines or blood, insulated transport boxes are needed. Rotational moulding makes it possible to produce double-walled boxes, with the hollow wall filled with foam for insulation.
A rotationally moulded cooler box offers excellent thermal insulation in extreme climates. The seamless construction prevents unwanted heat leakage or moisture bridges. The plastic used is food-safe, hygienic and inert to medical substances.
The boxes are shock-resistant and remain functional after drops. They seal well thanks to sturdy clamps and rubber gaskets. Internal compartments can be moulded in or added later, so the contents remain organised and protected. The result is a robust and efficient solution for medical logistics.
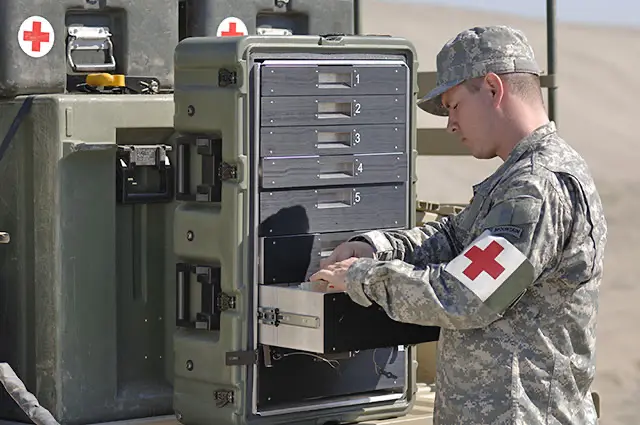
Weapon and ammunition cases
Ammunition and weapons require sturdy, safe storage. Plastic ammunition cases are resistant to impact, moisture and corrosion, forming a durable alternative to traditional metal variants.
Rotationally moulded ammunition cases are often stackable and equipped with integrated handles and closures. Since plastic does not conduct, it is safer for storing explosives. The corners and edges can be made extra thick for shock resistance.
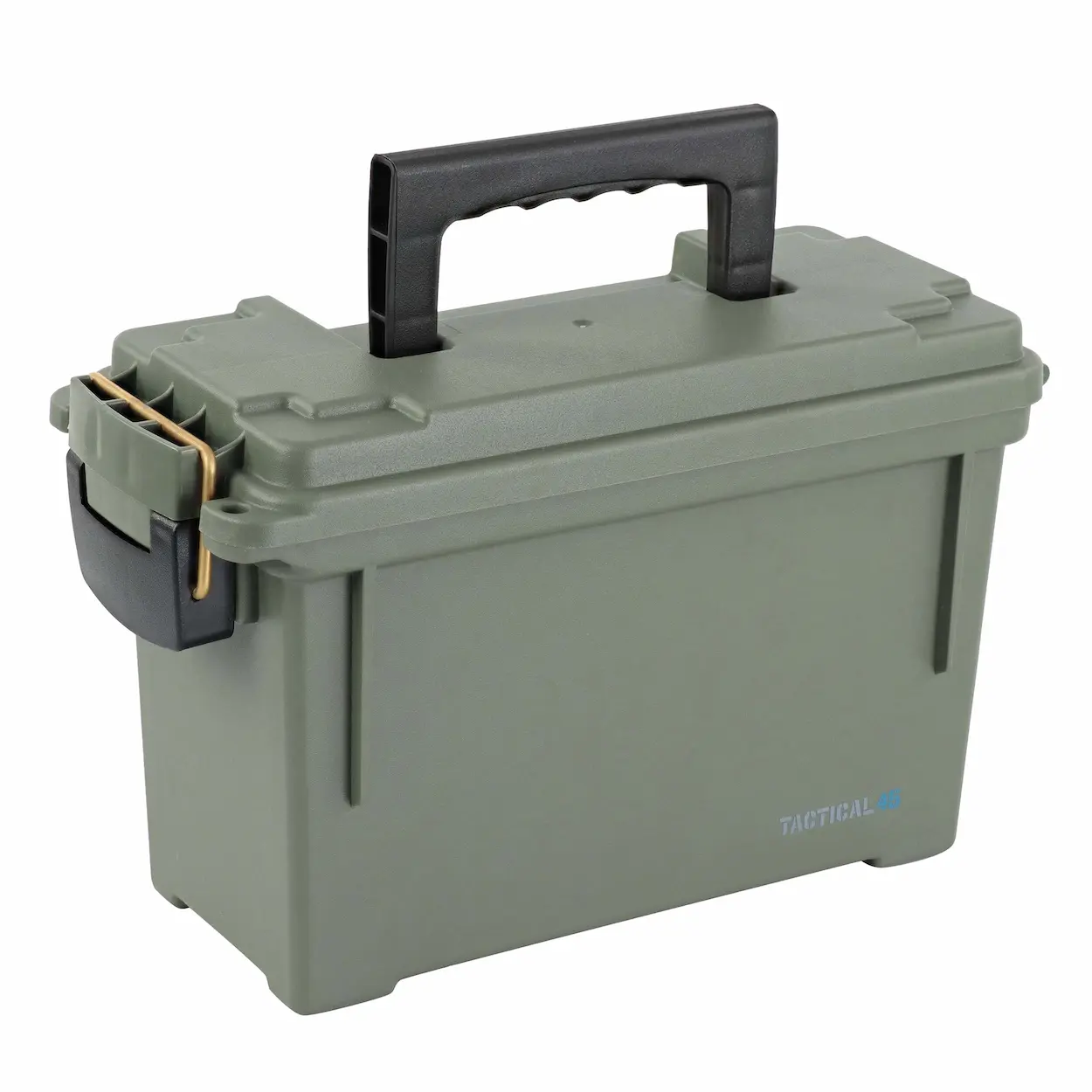
The lid can be equipped with an integrated seal so the case is water- and dustproof (e.g., IP67). Inside, rails or cutouts are possible for foam inserts or compartments. Everything is designed with the end use in mind.
Enclosures for communication equipment
Radios, servers and communication systems require enclosures that can withstand shocks, vibrations and environmental influences. Rotationally moulded plastic enclosures offer that protection and can be fully customised.
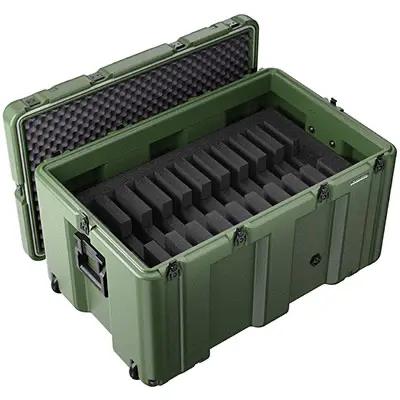
By using flame-retardant materials, enclosures can meet standards such as UL94 V-0. With coatings or conductive paints, EMI/RF shielding is also possible, protecting sensitive systems from electromagnetic interference.
Flexible walls dampen vibrations. Cable grommets, mounting frames or 19-inch racks can be integrated into the design. This creates a plug-and-play solution that can be deployed quickly and offers field protection.
Autonomous unmanned reconnaissance boats
An emerging application is the production of hull structures for unmanned surface vehicles (USVs). These small reconnaissance boats operate under harsh conditions and require strong, low-maintenance hulls.
A rotationally moulded hull is waterproof, seamless and impact-resistant. Compared to fibreglass, polyethylene is tougher and easier to maintain. Scratches have little effect and no painting is needed. Foam can also be added for extra buoyancy.
For scaling up, rotational moulding offers great advantages. Moulds can be produced quickly and production can be scaled relatively easily. For defence, this means producing innovative maritime resources quickly, at scale, and sustainably.
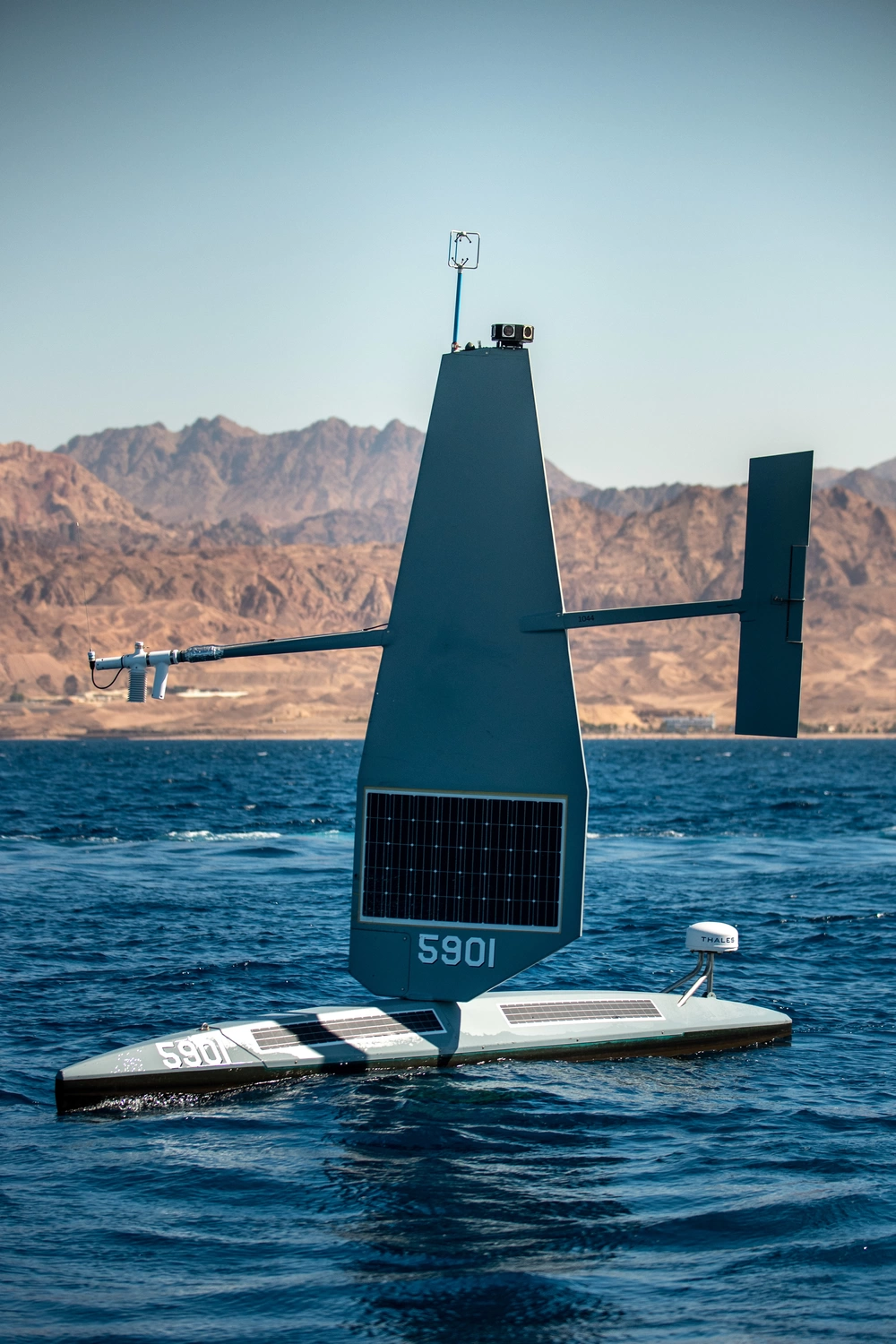
Collaboration for the best rotationally moulded solution
Pentas does not have ready-made defence products on the shelf. We are not a defence supplier with our own end products but a rotational moulding specialist with our own design department. We work together with partners who understand the application and the end-user needs. Pentas provides the material knowledge and production expertise.
Together with the customer, we develop a product from idea to realisation. We advise on material selection, wall thicknesses, mould construction and special requirements such as flame retardancy or UV resistance. Our moulds are developed in-house and after prototyping, we can scale up directly to production.
This close collaboration, where each party contributes its expertise, leads to the best result. Do you have a challenge where plastic could play a role? Rotational moulding might just be the answer. Feel free to contact us. We’re happy to think along.