Rotational moulding vs. blow moulding: Which production technique is best for your project?
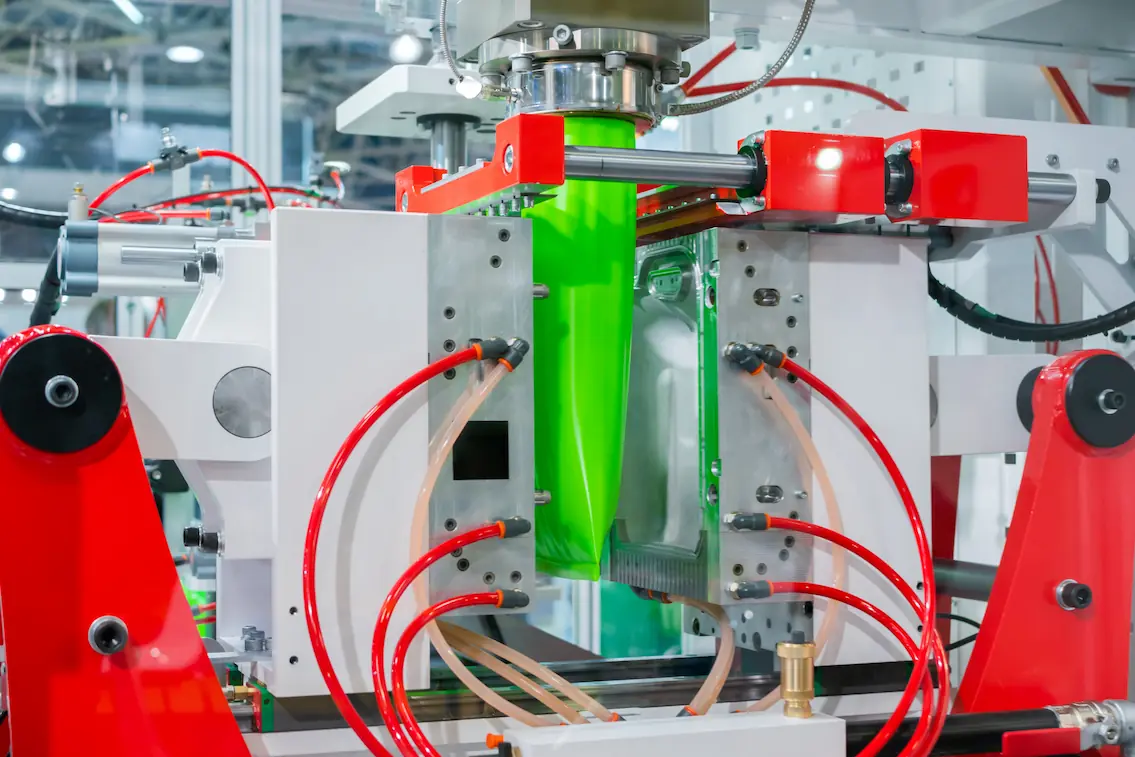
Do you want to manufacture a plastic product and are unsure whether to choose rotational moulding or blow moulding? Both techniques have their own advantages, depending on the design, production volume, and desired properties. At Pentas, we specialize in rotational moulding, but we understand that not every product is suitable for this method. Blow moulding is an alternative production technique with different characteristics and benefits. In this article, we compare both techniques to help you determine which method is best suited for your product. Whether you are looking for a flexible solution for small series or an efficient production method for larger quantities, we are happy to help you make the right choice.
Table of contents
What is blow moulding?
Blow moulding is a production method where a plastic tube (preform) is heated and expanded into a mould using air pressure. This results in a hollow product with thin walls. The process is widely used for manufacturing packaging.
The blow moulding process takes place in four phases:
Formation of the preform: A thermoplastic is extruded into the shape of a tube or a hollow droplet.
Closing of the mould: The mould is closed to define the shape of the final product.
Blowing and cooling: Compressed air presses the material against the walls of the mould. The plastic takes the shape of the mould and cools down.
Removing the product: The formed plastic solidifies and is removed from the mould. Any excess edges, which were created during the closing of the mould, are removed in this phase.
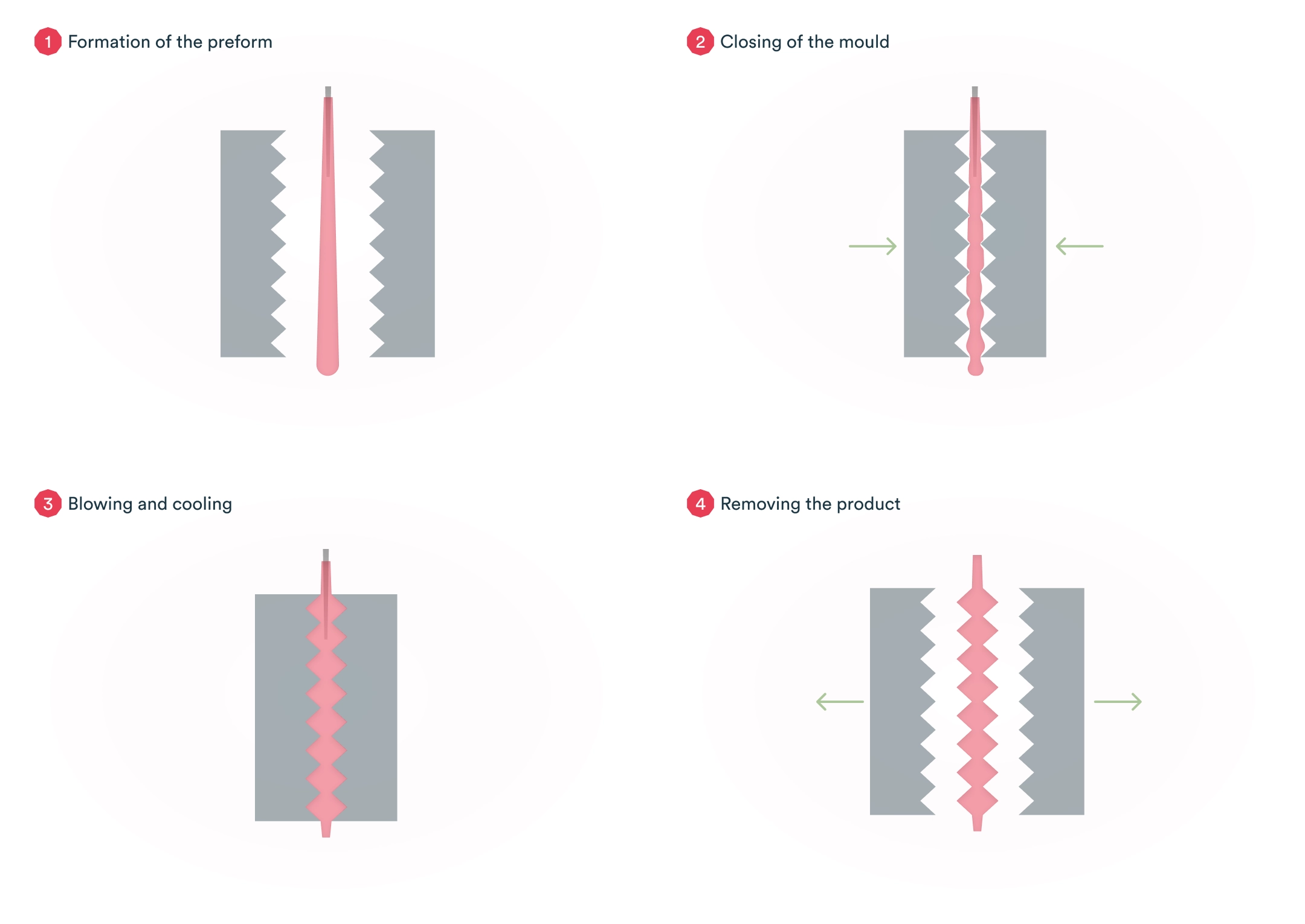
One of the biggest advantages of blow moulding is its efficiency in mass production. Short cycle times allow for the rapid production of large quantities at low costs per unit. This makes the process particularly suitable for packaging such as bottles and jerrycans. Additionally, blow moulding can process various plastics, offering flexibility in material selection.
However, there are limitations. The design freedom is more restricted than with other techniques, making it difficult to create complex or reinforced structures. Furthermore, wall thickness control is less precise, which can lead to variations in product quality. Although the unit production costs are low for large series, the initial investment is high due to the expensive moulds. This makes blow moulding less attractive for smaller production runs.
Applications of blow moulding:
Blow moulding is particularly suitable for the production of packaging, such as bottles and jerrycans.
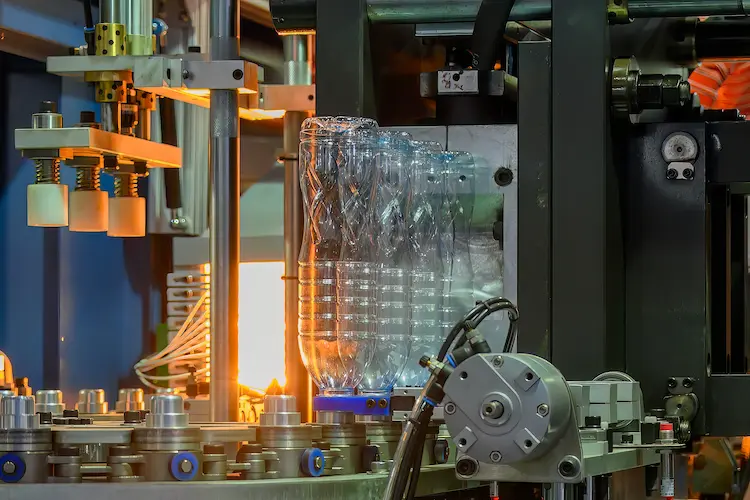
What is rotational moulding?
In rotational moulding, plastic powder is placed inside a mould, which is then slowly rotated around two axes in an oven. The heat melts the powder, causing it to adhere to the inner surface of the mould. The result is a seamless, hollow product with a uniform wall thickness.
One of the strengths of rotational moulding is its low mould costs, making it an ideal choice for smaller production runs. Additionally, this technique offers great design flexibility, allowing for the creation of complex geometries and double-walled structures. Since the process does not create seams, the products are free of stress points, contributing to high structural strength. This makes rotational moulding particularly suitable for large and durable products, such as storage tanks and playground equipment.
On the downside, the process is slower than blow moulding, resulting in longer production times per unit and higher costs for mass production. Rotational moulding is less suitable for extremely thin-walled products, and the material selection is more limited.
Applications of rotational moulding:
Rotational moulding is ideal for the production of complex, large products, such as these plastic tanks used in the agricultural sector.
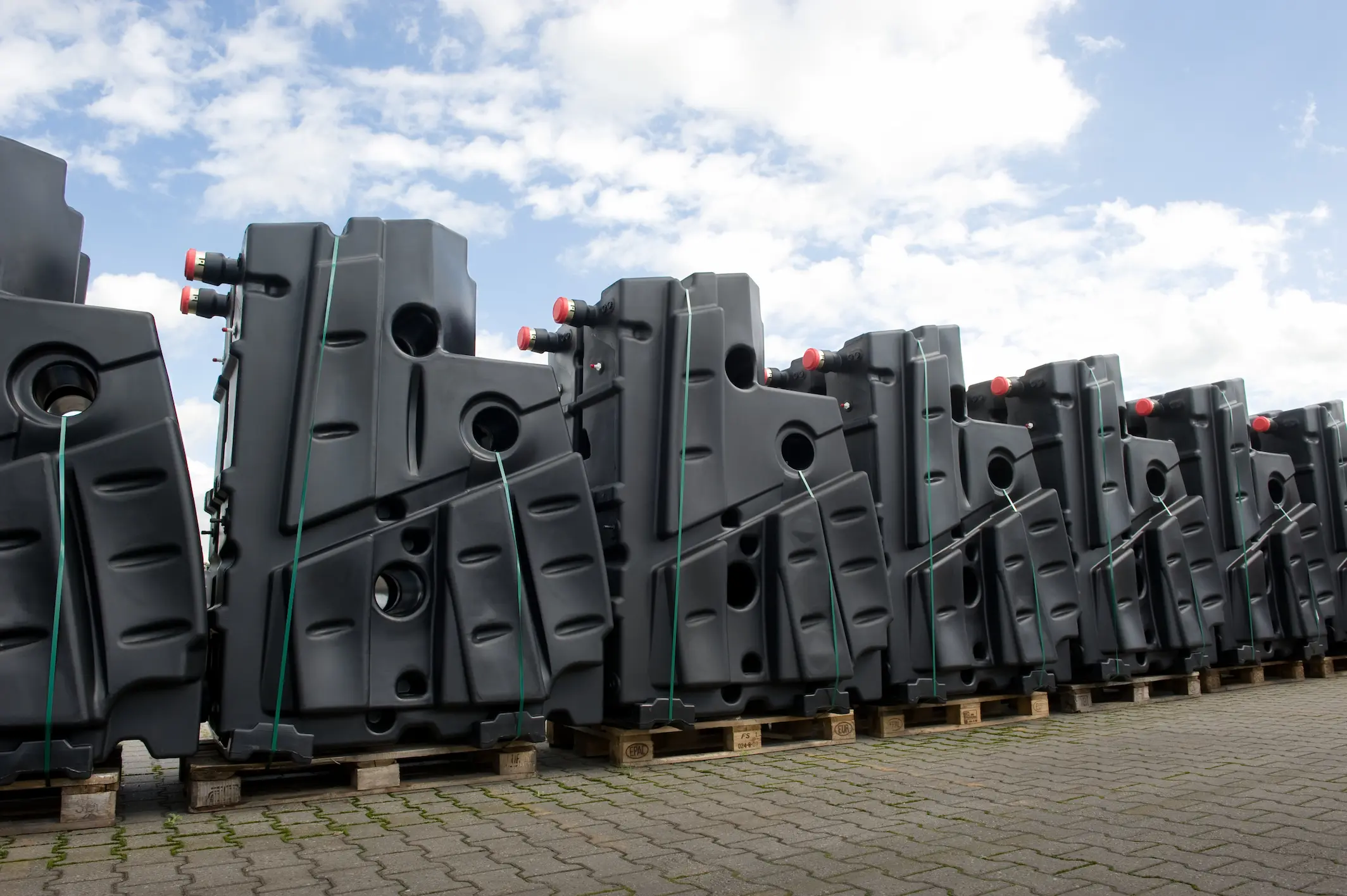
Which technique should you choose?
Blow moulding
The choice between blow moulding and rotational moulding depends on various factors, such as the desired production volume, design complexity, and costs. Blow moulding is particularly suitable for producing large quantities of thin-walled, hollow products. With its fast cycle times and ability to work with various plastics, this technique offers a cost-effective solution for mass production.
Rotational moulding
Rotational moulding, on the other hand, is ideal for products with a complex design that require uniform wall thickness and structural strength. The low mould costs make this technique attractive for smaller series, while the seamless construction enhances durability. Moreover, rotational moulding allows for the production of very large products, such as storage tanks and playground equipment, which are difficult or impossible to achieve with blow moulding.
When a product needs to be lightweight and produced in large quantities, blow moulding is an efficient solution. For products that need to be large, strong, or complex in shape, rotational moulding is often the better choice. The final decision depends on the specific requirements of the project and the desired product properties.
Property | Rotational moulding | Blow moulding |
---|---|---|
Production volume | Ideal for small to medium runs (10 - 5,000 units), but runs of up to 50,000 units are possible | Ideal for small to medium runs (10 - 5,000 units), but runs of up to 50,000 units are possible |
Cost per product | Higher due to longer production time | Low for high volumes |
Mould costs | Relatively low | High |
Wall thickness | Thick and uniform | Thin, difficult to vary |
Design freedom | Very flexible, suitable for complex designs | Limited, mainly simple shapes |
Mechanical strength | Seamless, strong, and durable | May contain seams and weak points |
A suitable solution for every project
Curious which production technique best suits your project? At Pentas, we are happy to think along with you! Contact us and discover how we can bring your product idea to life. We will discuss the possibilities and find the perfect solution together.