The foaming of rotationally moulded products
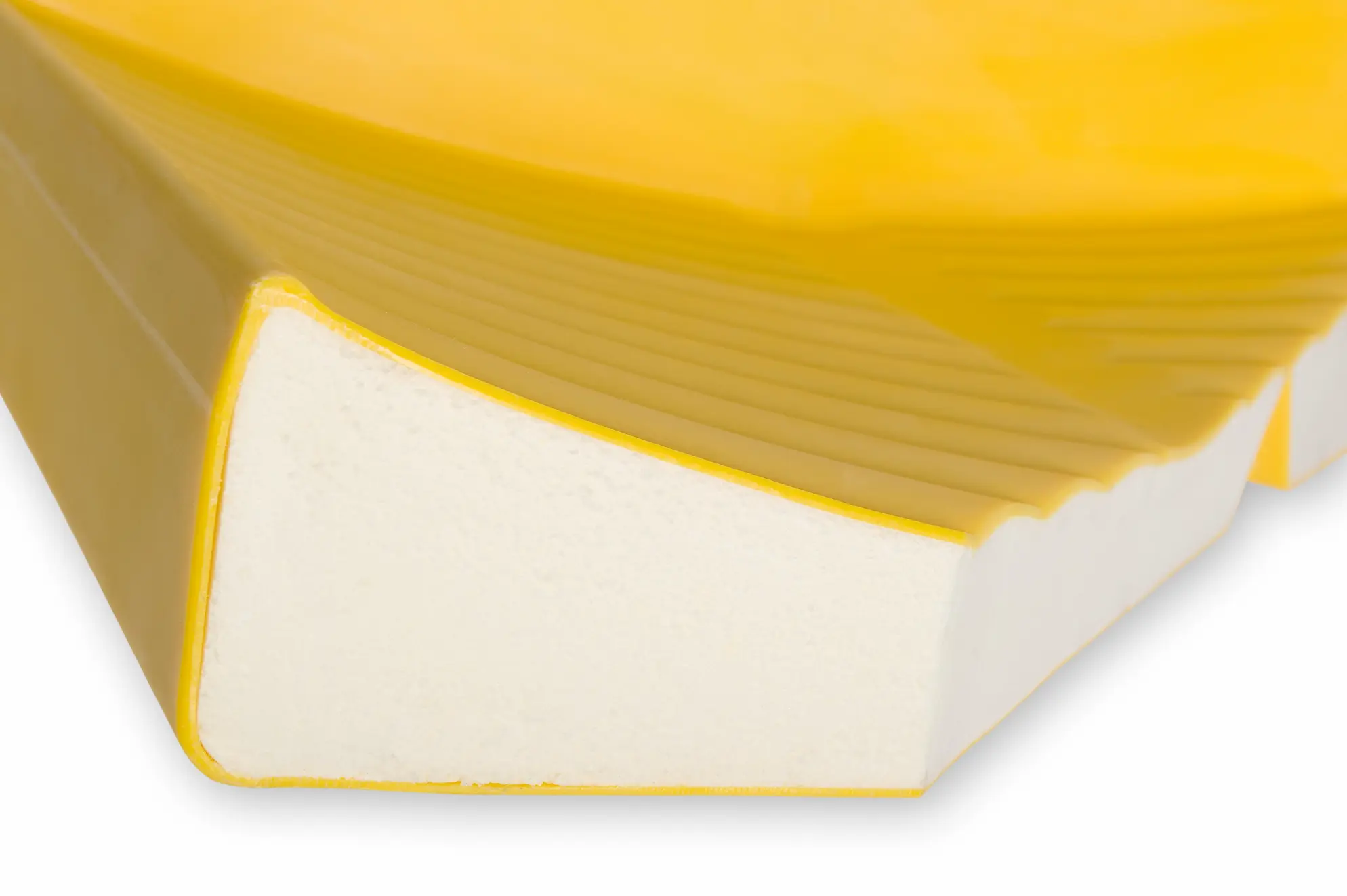
Since the establishment of Pentas, we have built extensive experience in foaming rotational moulding products. Our origins lie in the production of rotationally moulded polyethylene (PE) surfboards. These surfboards, which are hollow due to the rotational moulding process, were filled with polyurethane foam (PU) to provide the necessary rigidity.
Table of contents
Today, we build on this knowledge. In close collaboration with various partners, we have refined and further developed our foaming process. As a result, we can now foam a wide range of products, from transport trays requiring extra stability, insulation containers, floats, tanks offering freeze protection, to even medical tabletops needing more rigidity.
In this blog, we will tell you everything about how the foaming process works and its versatile applications.
The different foam materials
Various materials can be used for foaming in rotational moulding, depending on the desired properties of the end product. Here are some common foaming materials suitable for rotational moulding applications:
Polyethylene (PE) foam: Polyethylene is the most commonly used material in rotational moulding due to its good impact resistance, chemical resistance, and cost-effectiveness. It can be foamed to create lightweight, insulating, and strong products, such as in storage tanks, coolers, and protective packaging.
Polyurethane (PU) foam: This foam provides excellent shock absorption and insulation. Polyurethane is often used for products requiring a higher degree of flexibility and cushioning, such as sports equipment, seats, or protective gear.
Polypropylene (PP) foam: Polypropylene has higher heat resistance and is suitable for applications where products need to withstand higher temperatures, such as autoclaveable parts or heat-resistant containers.
EVA (Ethylene-vinyl acetate) foam: This type of foam offers excellent flexibility and impact resistance, making it suitable for applications like sports equipment, shoe soles, and other resilient products.
Each material offers specific advantages, such as flexibility, stiffness, chemical resistance, or thermal insulation. The choice of material depends on the specific requirements of the application, such as thermal insulation, impact resistance, or chemical resistance.
The different types of foam
In rotational moulding, different types of foam can be used depending on the desired properties of the final product. The two main types of foam are closed-cell foam and open-cell foam:
Closed-cell foam
This type of foam contains cells that are completely closed, preventing air and moisture from entering. This makes it an excellent thermal insulator and water-resistant. Closed-cell foam is often used in applications such as insulated tanks, coolers, and storage tanks where protection against moisture and temperature changes is essential.
Open-cell foam
In open-cell foam, the cells are interconnected, resulting in a less dense structure that is better at absorbing shocks and sound. This type of foam is often used in products where shock absorption is more important than insulation, such as in protective packaging and sports equipment.
One-step foam
Additionally, there are foaming systems like one-step foam, where a blowing agent is added to the rotational moulding process to create a foam core with a rigid outer layer. This is often used to create products with variable stiffness and cushioning properties.
The choice of foam type depends on the specific requirements for stiffness, impact resistance, and insulation in the final application.
Why foam?
Insulation
The foam provides insulation because it consists of a network of closed cells that trap air. Air is an excellent thermal insulator as it significantly reduces heat transfer through conduction. In a rotationally moulded product with a foamed core, this means that the air trapped in the foam cells prevents heat from quickly passing through the material.
This property makes foamed rotationally moulded products ideal for applications where thermal insulation is important, such as coolers, storage containers for hot or cold liquids, and other insulated containers. The foam acts as a barrier that limits both heat loss and heat gain, keeping the product more stable under temperature changes.
Impact resistance
Foaming in rotationally moulded products not only enhances insulation but also improves the impact resistance of the product. The foam structure absorbs energy upon impact, making the product more resistant to breakage or deformation. The foam acts as a buffer, with the air trapped in the cells helping to absorb shocks and vibrations.
This makes foamed rotationally moulded products highly suitable for applications where they are exposed to harsh conditions or repeated impacts, such as sports equipment, protective casings, and packaging for sensitive equipment. Thanks to this impact resistance, the products remain intact longer, even under heavy use, significantly increasing their durability. This is crucial for applications like forklift roofs, which must withstand falling objects.
Stiffness
Foaming in rotational moulding contributes to stiffness by combining a rigid outer layer with a foamed core, creating a stronger structure without increasing the weight. The hard outer layer of the product provides structural strength, while the foamed core offers support and contributes to the overall stiffness due to its closed cells.
This principle makes foamed rotationally moulded products suitable for applications where a balance between lightweight and stiffness is required, such as in furniture, containers, and construction panels. The foam layer reduces sagging or deformation under load, helping the product maintain its shape and function even under prolonged use or heavy loads. This is essential for products like luggage trays that race through transport systems at high speed.
Foaming methods:
Foam can be applied to a rotationally moulded product in two ways: post-mould or during the rotational moulding process itself. Each method has its pros and cons.
Foaming during the rotational moulding process (in-situ foaming)
In this method, the foam is applied during the rotational moulding process, usually by adding a blowing agent or foaming agent to the polymer powder in the mould. The foam forms during heating and rotation, allowing the product to be shaped in a single step.
Advantages:
Disadvantages:
Foaming post-mould (post-moulding foaming)
In this method, the foam is added after the moulding process. This is done by injecting foam through openings in the product or by filling the product with foam after the rotationally moulded outer layer has been formed.
Advantages:
Disadvantages:
Both methods offer advantages depending on the product design and application requirements.
Examples of foamed products
Luggage trays
These custom trays transport luggage at airports at high speed. Thanks to PU foam, they gain the strength needed to effortlessly process thousands of suitcases.
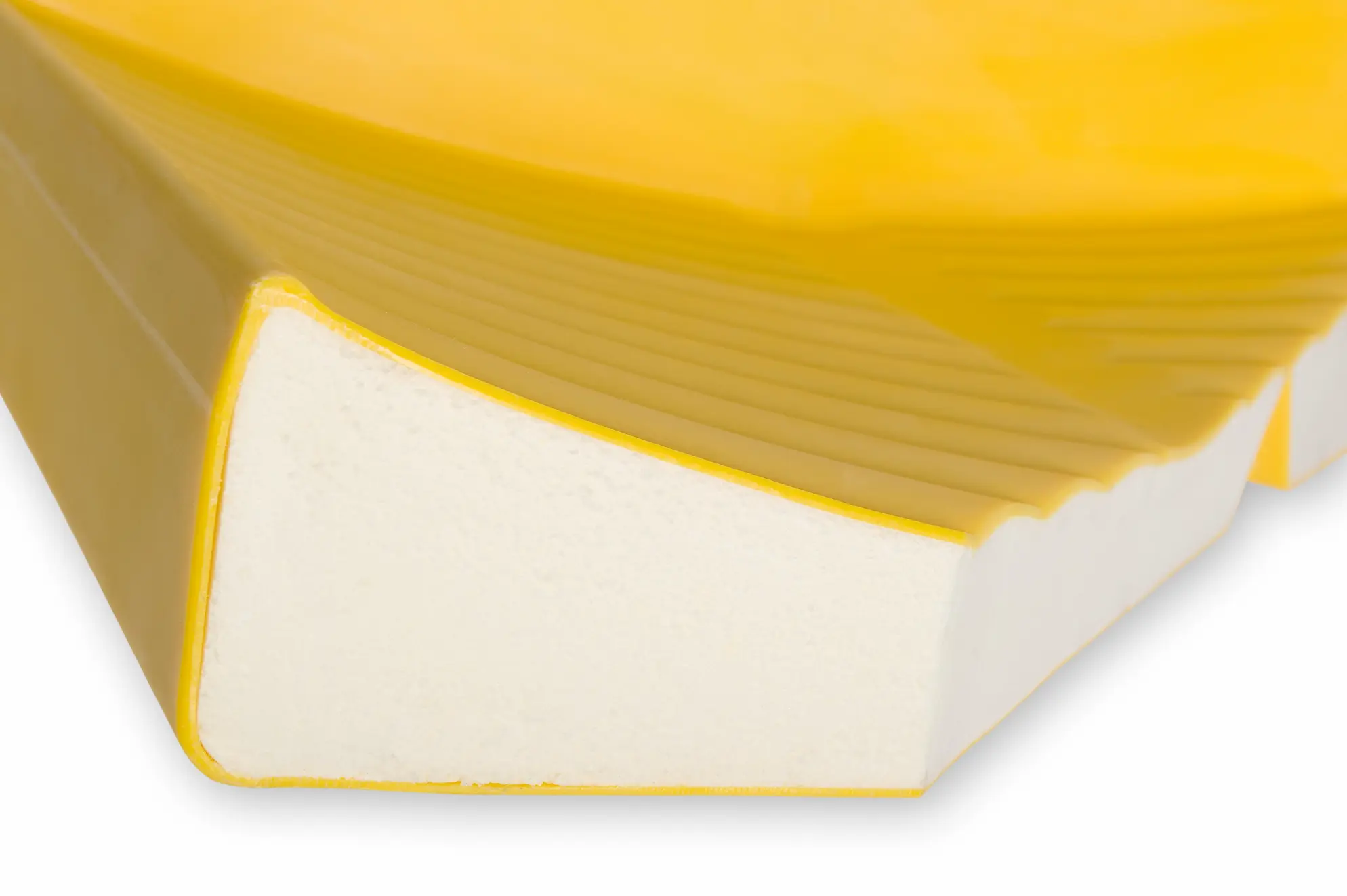
Medical tabletops
For hospitals, we have developed tabletops that are both flat and strong thanks to the foam.
Coolers
Coolers benefit from the insulating effect of PU foam, allowing them to keep their contents cool for a long time.
Floats
Floats used in pool lane markers or lakes have their buoyancy increased by filling them with PU foam.
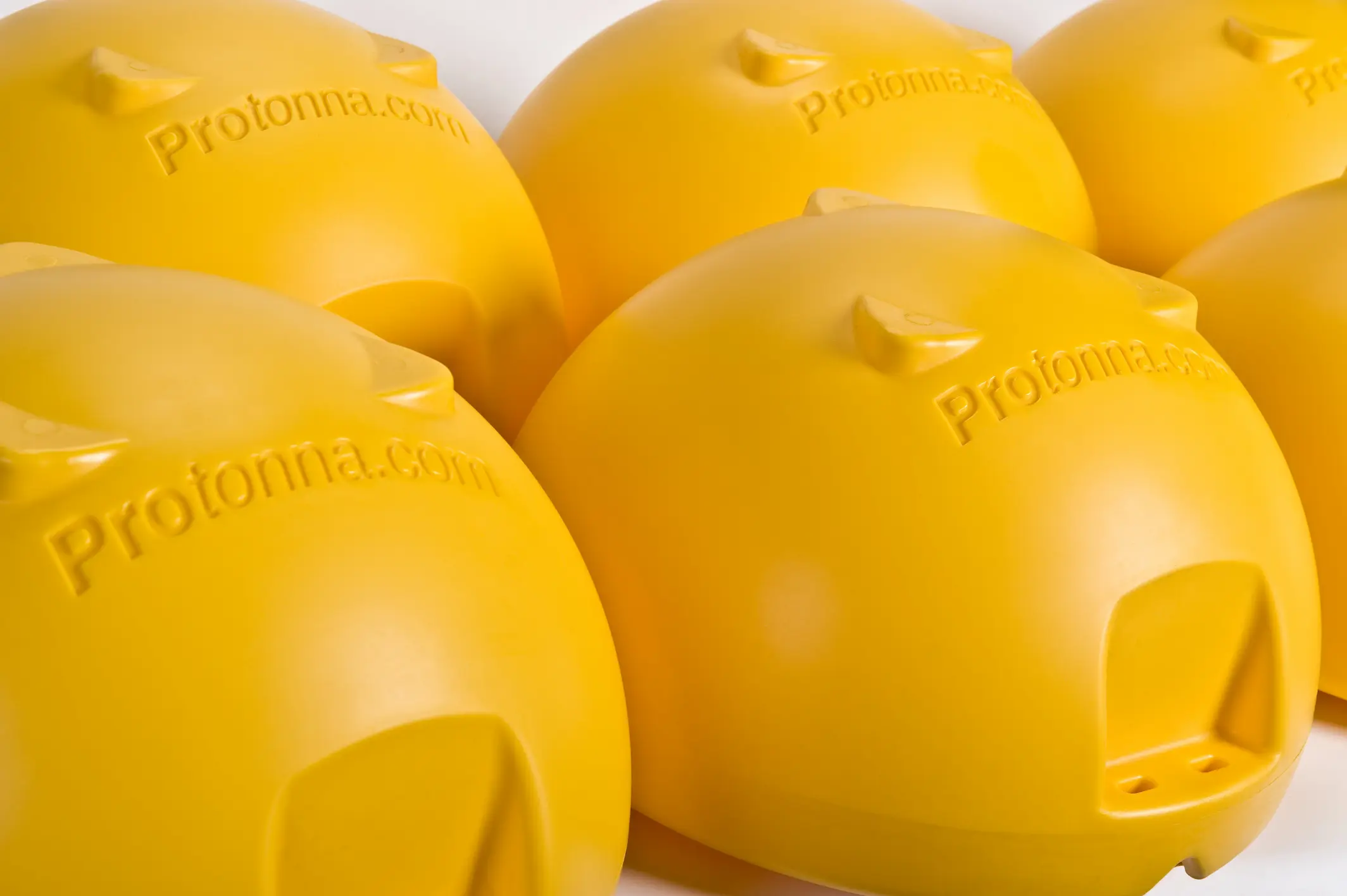