The importance of material choice: A comparison of Linear and Cross Linked Polyethylene
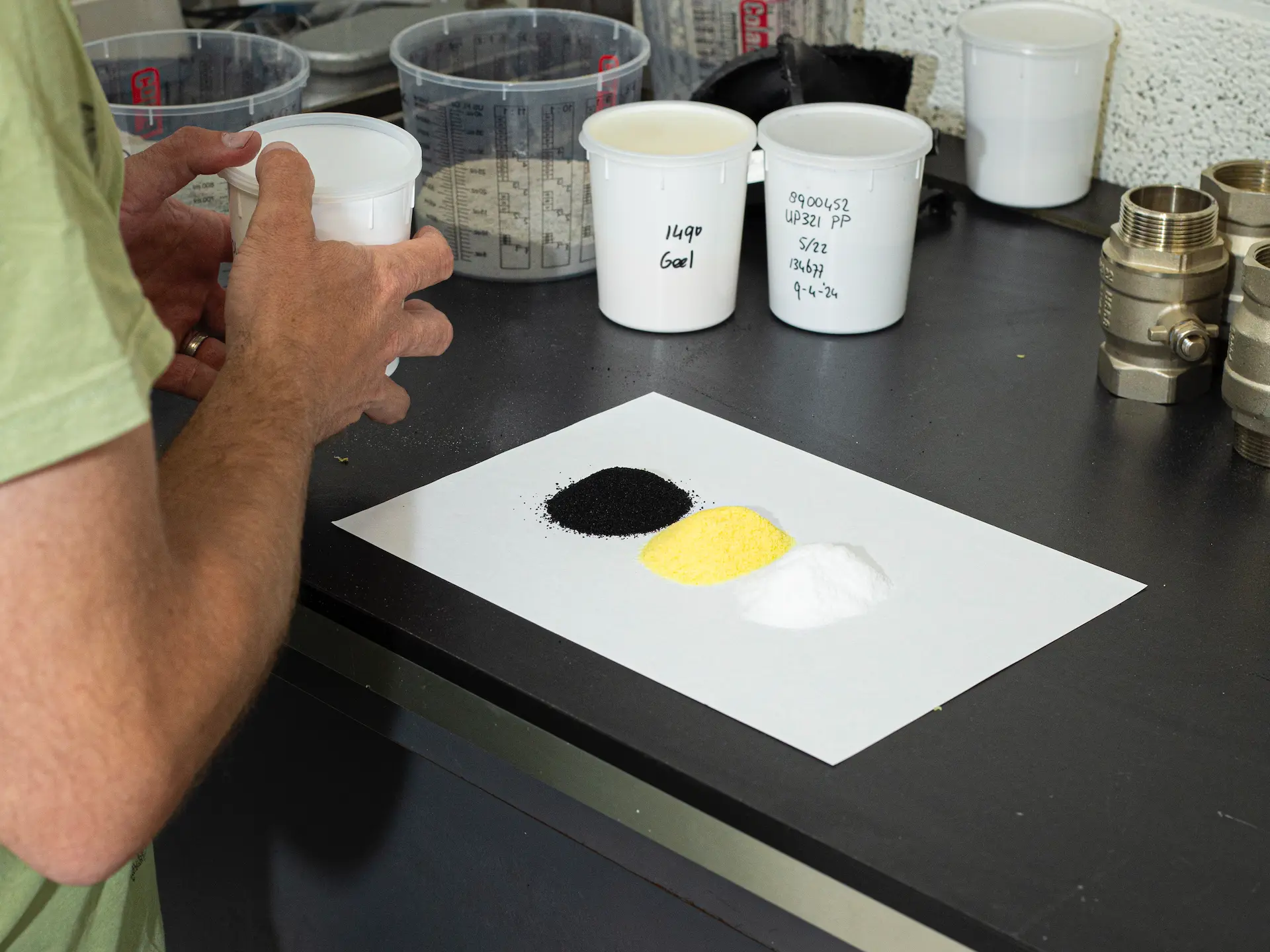
In rotational moulding, there is less choice of materials compared to techniques such as injection moulding or blow moulding. This is because it involves a low-pressure manufacturing process where it is more challenging to introduce heat into the material to melt it. Within the available rotational moulding materials, polyethylene (PE) is the most common. There are significant differences within this category, but generally, they can be categorized into Linear Polyethylene (LPE or LLDPE) and Crosslink Polyethylene (XLPE). Each of these prominent materials has unique properties, which are discussed further in this article.
Table of contents
Linear Polyethylene (LPE/LLDPE): Flexibility and durability
LLDPE, known for its flexibility and impact resistance, is an ideal choice for products requiring a balance between pliability and durability. The excellent impact resistance of LLDPE, even at extreme temperatures, makes it a reliable choice for a wide range of products, such as agricultural tanks, playground equipment, recreational vehicles, and industrial containers.
The chemical resistance of LLDPE makes it a preferred material for storage tanks and containers that need to withstand various substances. Moreover, the ease of processing LLDPE in the rotational moulding process allows for cost-effective production, making it a financially sensible choice for manufacturers. From an environmental perspective, the recyclability of LLDPE is an additional benefit, contributing to the sustainability goals of industries.
However, this material is not well suited for manufacturing gasoline fuel tanks because permeation occurs, meaning gasoline can migrate through the polymer and eventually escape into the environment. Permeation is a critical consideration when designing fuel tanks with materials such as PE, especially due to environmental and safety concerns. For diesel, it functions differently, which is why such tanks are mostly made from linear PE.
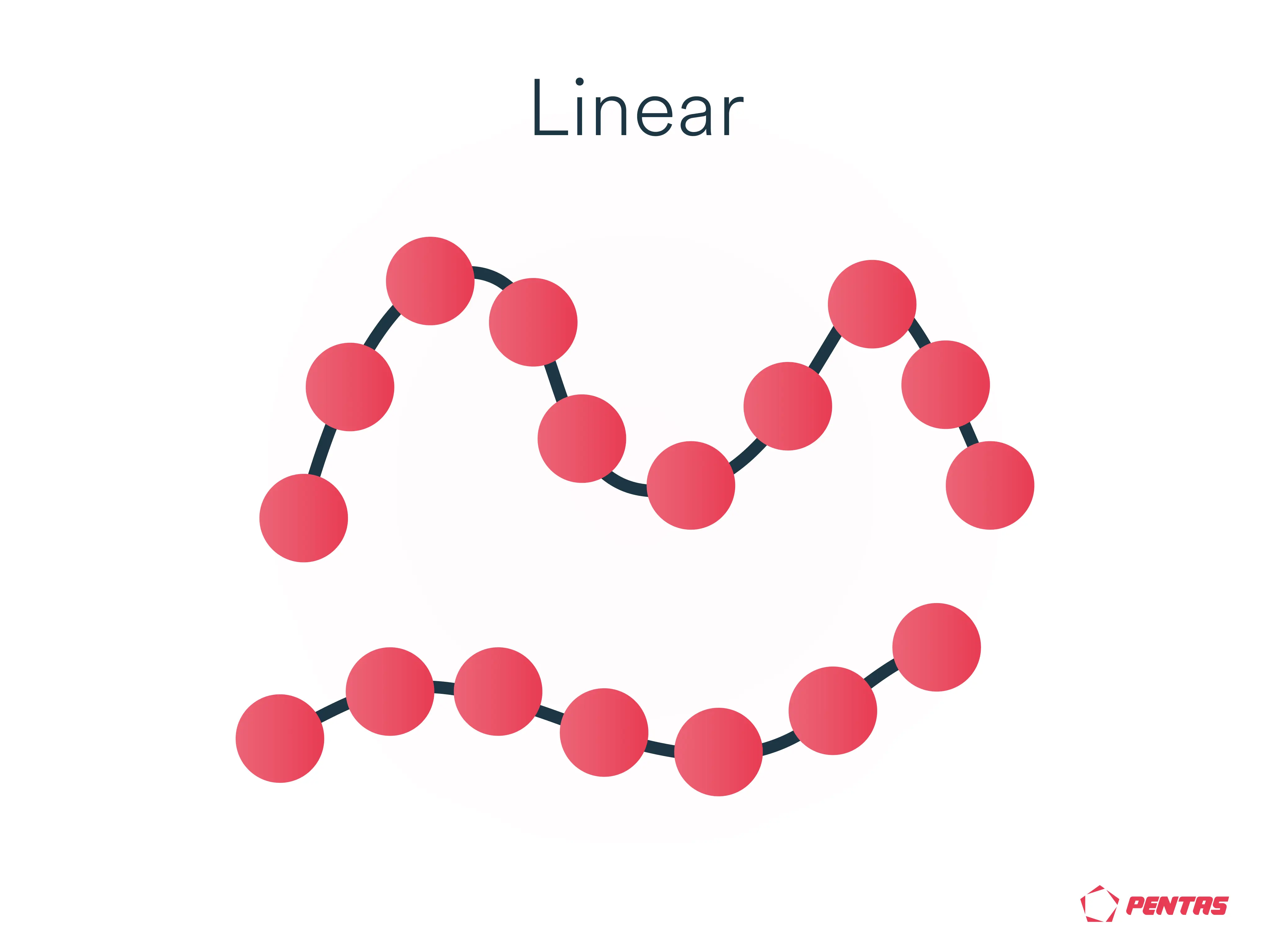
Crosslink Polyethylene (XLPE): Robustness for heavy industrial applications
On the other end of the spectrum is XLPE, which stands out for its excellent chemical resistance and heat resistance. The crosslinking technology enhances the molecular structure, resulting in increased rigidity and mechanical strength. This makes XLPE the choice for heavy industrial applications, such as pipelines, fuel, and chemical storage tanks.
The durability of XLPE means an increased resistance to cracking and breaking, essential for products exposed to demanding conditions. However, a significant drawback of XLPE is that it is not recyclable and, due to very tight manufacturing process tolerances, there is a higher scrap rate, an aspect companies must consider regarding sustainability practices and environmental awareness.
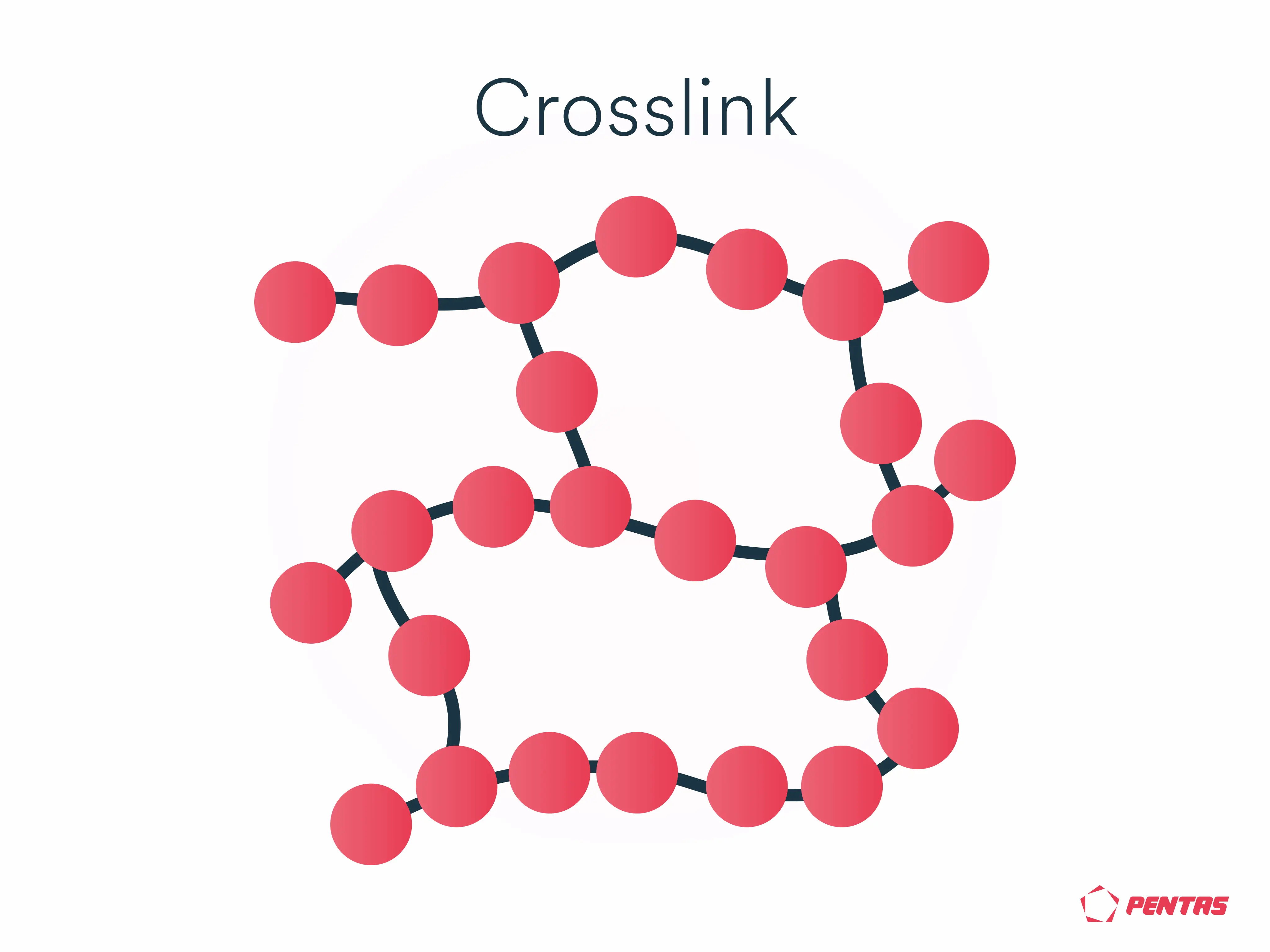
Making the choice: LLDPE or XLPE?
Choosing between LPE/LLDPE and XLPE may seem challenging, but when considering environmental factors, the choice becomes clearer. XLPE, although strong and durable, offers fewer benefits in terms of recycling and environmental impact compared to LPE/LLDPE. Moreover, when considering applicability and the importance of rigidity, LPE/LLDPE offers ample opportunities to develop products that are not only strong and functional but also environmentally conscious through smart design and innovation, such as the use of form stiffness and ribs. Through thoughtful material choices and design strategies, we can create products that are sustainable and environmentally friendly.