The production and product process at Pentas
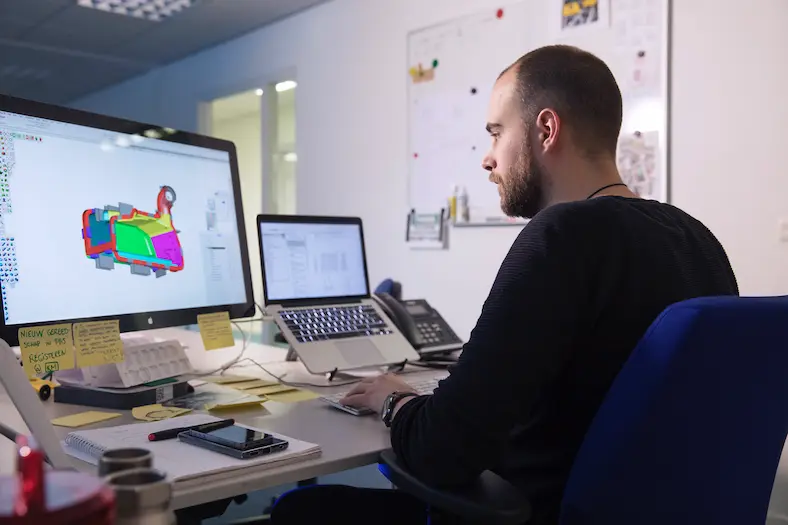
A well-designed rotationally moulded product starts with a carefully thought-out product process. At Pentas, we have gained extensive experience over the years in developing and producing plastic solutions. Once the design is ready for series production, we take the next step: making the product. In this article, we walk you through the steps involved.
Table of contents
Phase 1: Drawing up the programme of requirements
A good rotational moulding product starts with a clear Programme of Requirements (PoR). Together with the customer, we draw up this document as the foundation for the entire development process. It outlines the functional and technical requirements the product must meet.
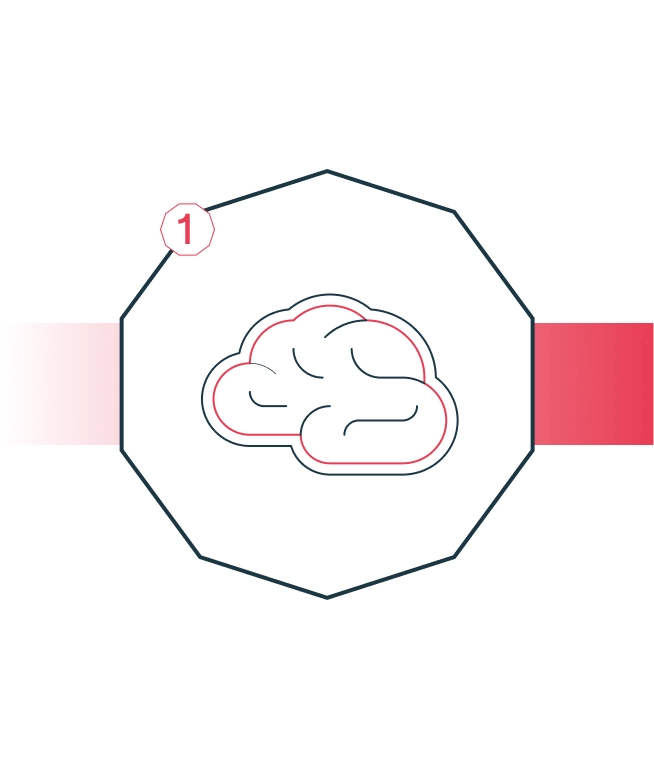
We not only map out the customer’s wishes but also add our many years of experience. What works in practice? Where can we optimise? And what are potential pitfalls? This leads to a complete and feasible set of requirements that serves as a clear guide for the further development of the product.
Examples of PoR components:
Phase 2: Concept development
In this phase, we focus on design, functionality, and manufacturability. We develop one or more concepts and test them against the PoR. We look at both the product’s shape and its application. Often, additional components such as level indicators, caps, and hoses are mounted on the product. Thanks to our extensive supplier network, we have access to a wide range of assembly components.
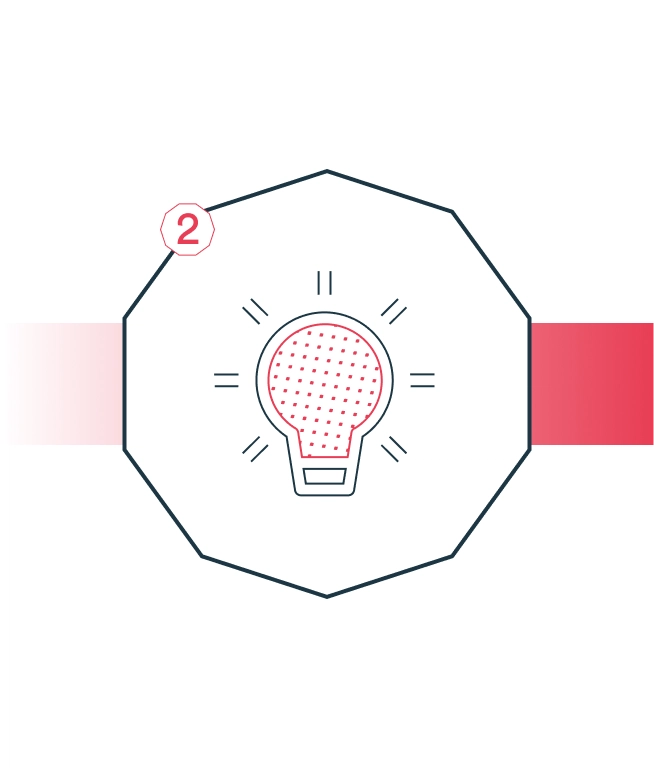
Phase 3: Analysis
To avoid surprises during production, we perform a thorough risk analysis beforehand. We critically assess the selected materials and determine whether the design is suitable for efficient assembly. Using the FMEA method (Failure Mode and Effects Analysis), we systematically identify potential failure modes early on and take preventive measures.
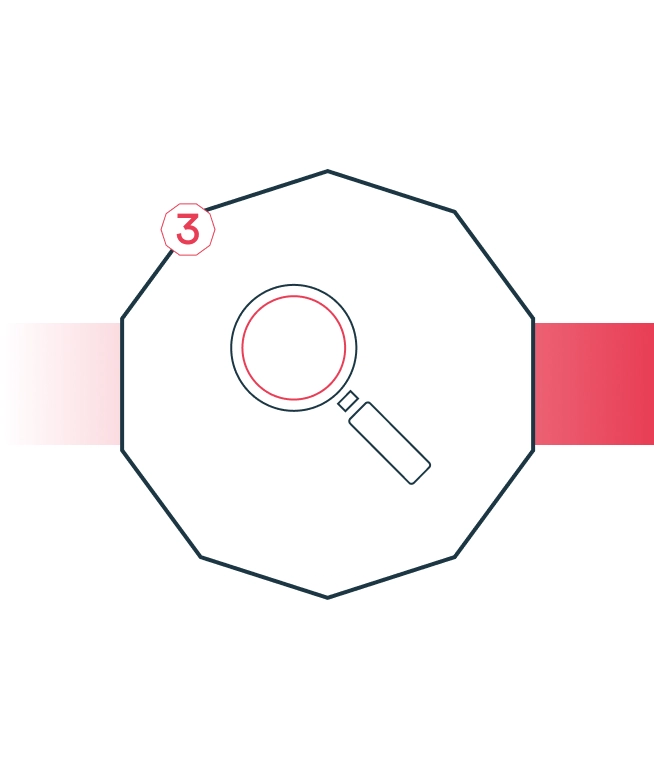
A key part of this phase is creating a control plan. It defines what quality checks are done, when, and with what tools and tolerances. We also design 'Poka-Yoke' solutions – clever process adjustments that automatically help prevent errors.
Phase 4: Final design and approval
This phase bridges design and actual production. The chosen concept is refined into a fully manufacturable product. Depending on customer preference, we do this independently or in close collaboration with their engineering team.
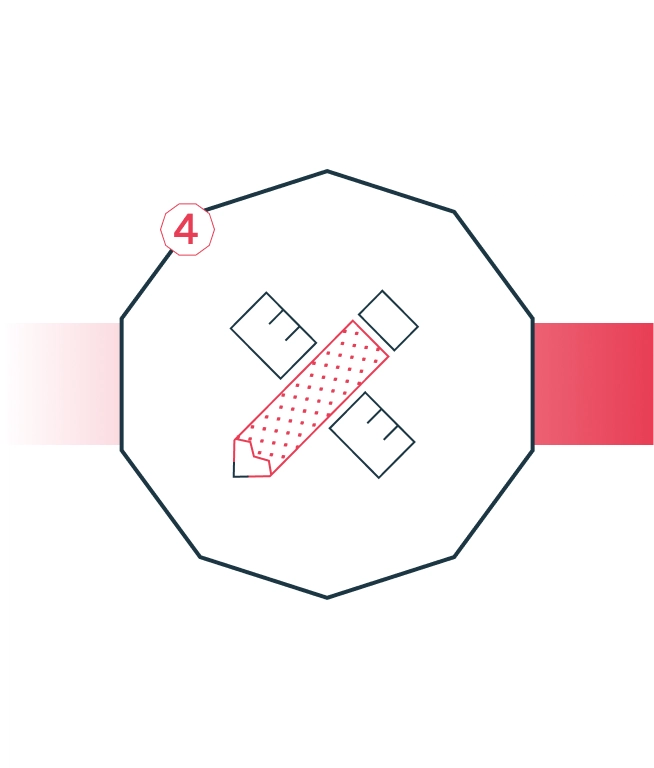
Here we define the ideal wall thickness, structural ribs, and draft angles for easy demoulding. Dimensions, tolerances, and critical product features are carefully documented.
Based on this, we create a precise 3D CAD model as the basis for mould and tool production, followed by detailed 2D drawings for quality control during and after production.
Customer approval of these drawings and models marks the official design release and the start of mould construction.
Phase 5: Moulds, support tools, gauges, and automation
After final CAD approval, we begin mould production. Since we design and manufacture moulds in-house, we ensure optimal cost-efficiency and a short turnaround time. At the same time, we develop necessary support tools, gauges, and automation (e.g. robot programs or Pick & Place systems). A detailed project plan ensures all parts are ready in time for the next production steps.
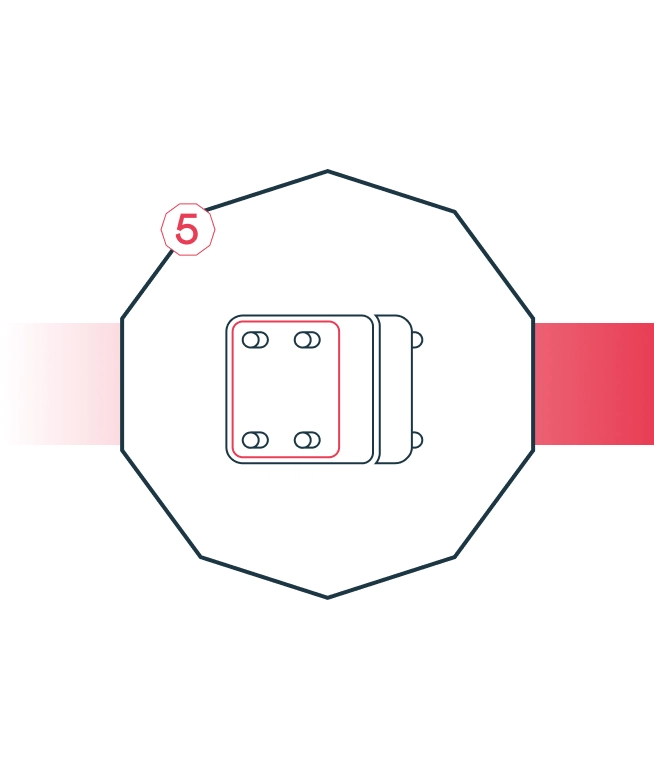
Phase 6: First Article Approval (FAA) and production startup
Before series production begins, the product undergoes the First Article Approval (FAA) process to validate both the product and process.
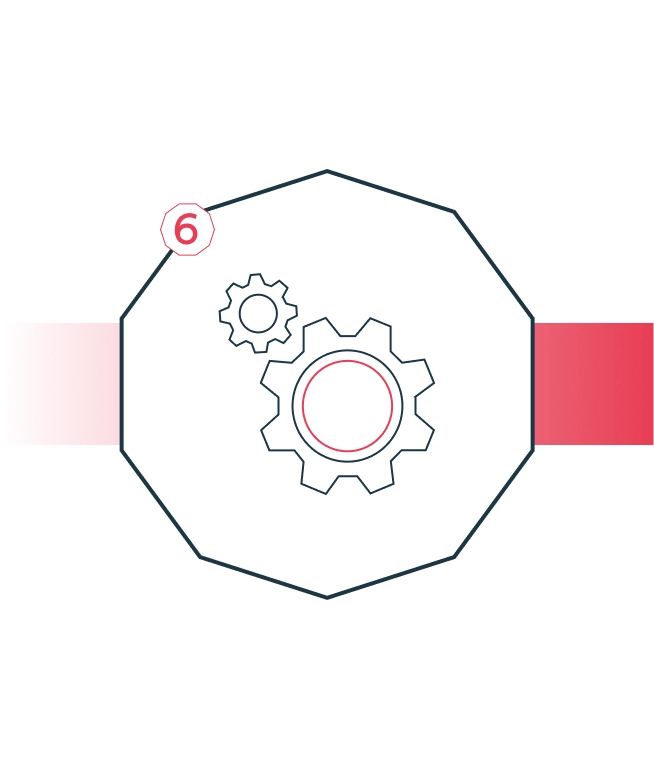
Once the mould is ready, it is installed on the rotational moulding machine and a small test batch is produced. During this phase, machine settings such as rotation speeds, temperature profiles, and cooling times are optimised for consistent quality and ideal wall thickness.
The test products are thoroughly measured and inspected by our quality department. Findings are recorded in an FAA report, which forms the basis for final product approval.
Any deviations are reviewed and, if necessary, adjusted in the design, mould, or process. Only when the product meets all PoR requirements is it released for series production.
Phase 7: Series production, finishing & assembly
After product approval, we begin series production. The mould is scheduled based on customer orders. Everything is set up to ensure stable, reproducible quality. Tools, components, instructions, and checks are all aligned to the product. Our technical staff handle post-processing, such as trimming and inspection. If needed, the product is fully assembled with sensors, hoses, or couplings to deliver ready-to-use components or finished products.
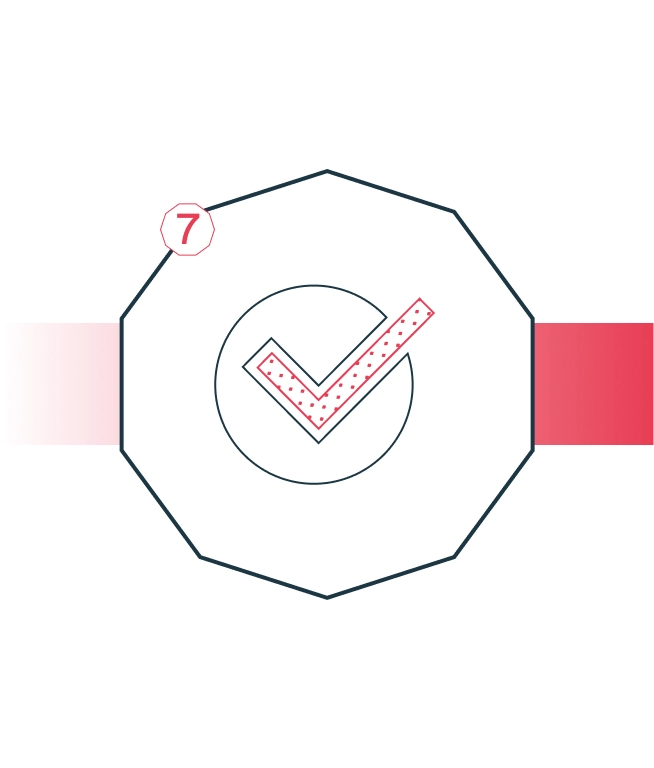
Quality assurance remains essential. Our staff conduct random inspections using tablets and 3D scanners, comparing results directly with 3D models and drawings. Deviations are addressed at the source.
Finally, we handle logistics – delivering the right product at the right time and place, including Just-in-Time and Just-in-Sequence deliveries tailored to the customer’s production.
Pentas has many years of experience developing and producing plastic products via rotational moulding. Every project – from initial design to final delivery – is carefully managed. Accuracy is key in every phase, with attention to technical details and practical usability. A structured approach and ongoing coordination with the customer ensure a smooth process. Our products are used worldwide in a wide range of industries.
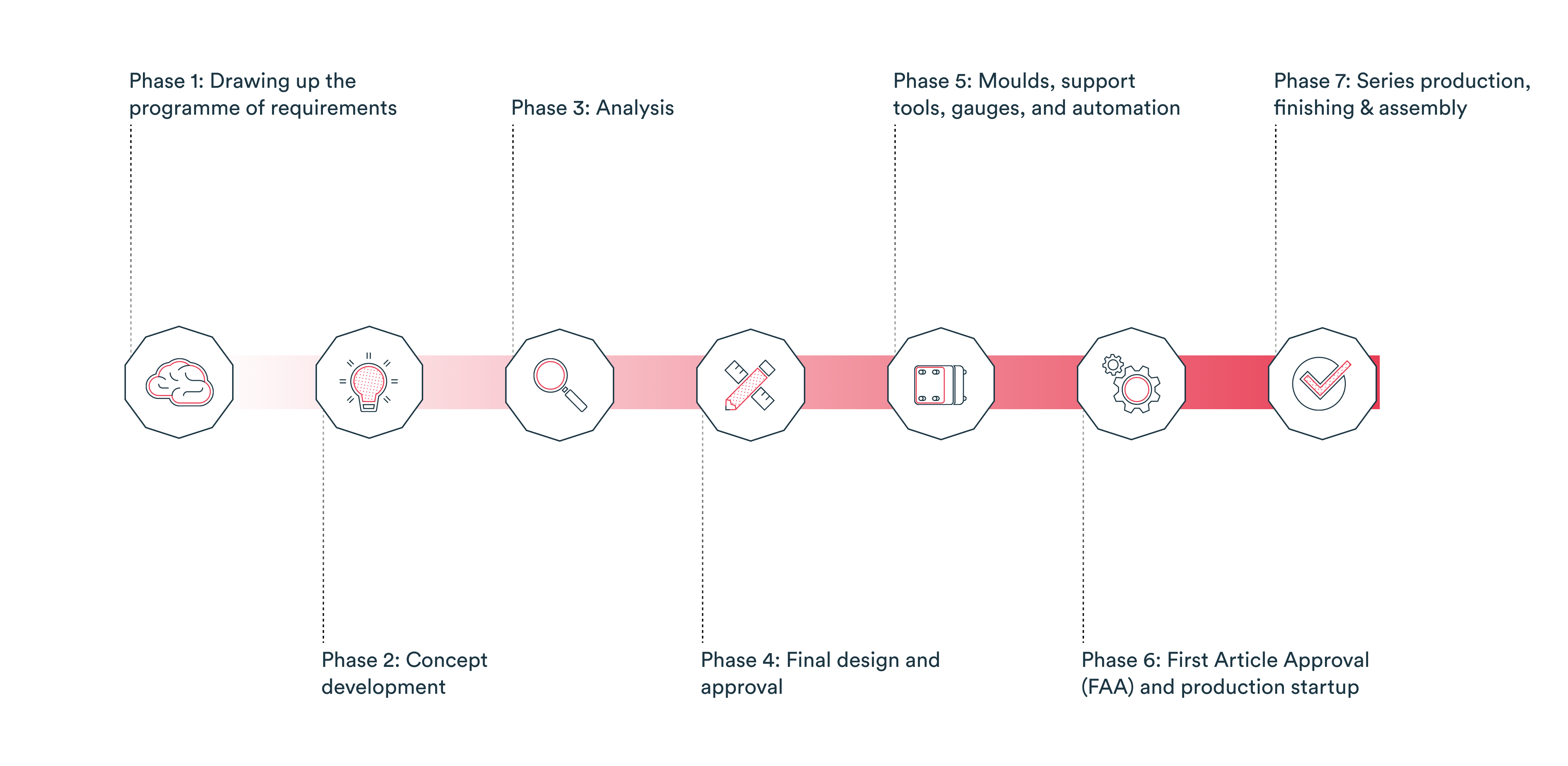