The rotational moulding process
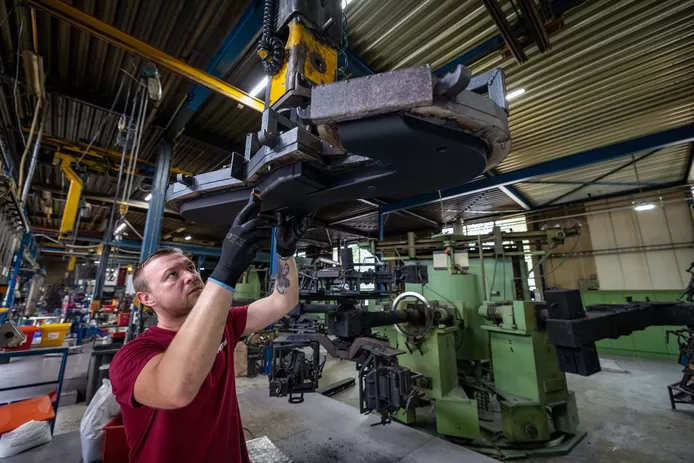
Rotational moulding is a unique production method used to create hollow plastic products. This technique is particularly suitable due to its ability to produce large, durable objects with uniform wall thickness and complex shapes. In this article, we would like to tell you more about the steps involved in the rotational moulding process.
Table of contents
Step 1: Filling the mould
The process begins with placing and filling the mould. Pre-weighed plastic powder, often polyethylene, is loaded into the mould. The powder has a size of 35 mesh, corresponding to a diameter of 74 to 2000 microns. It is important that this is so small because it absorbs heat more efficiently than granules, which ensures faster and more even melting. The consistency of the powder is also crucial, as uniform particle size and good flow ensure a uniform wall thickness.
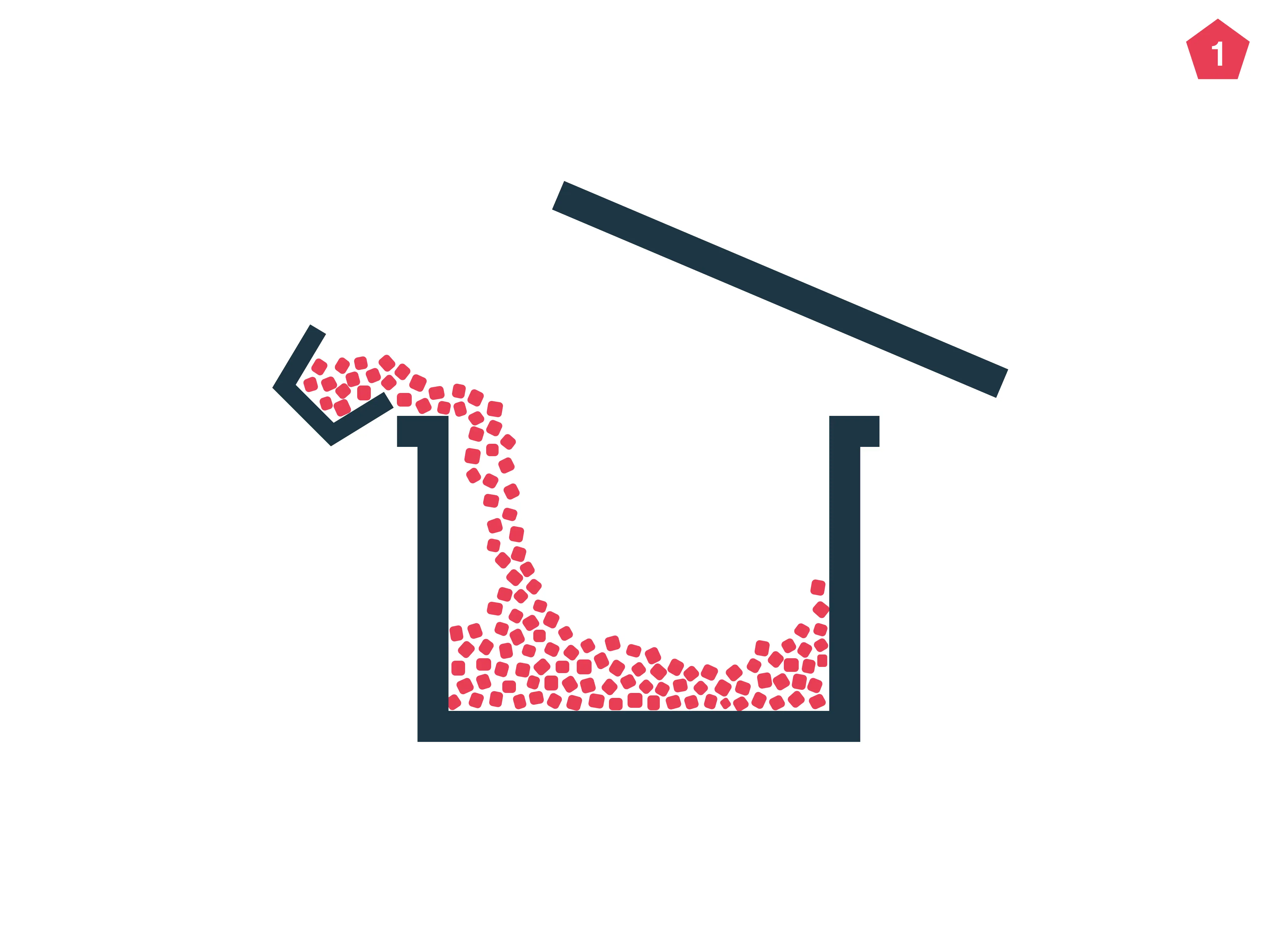
The inside of the mould is also cleaned and must be free of contaminants. Release agents are often applied to facilitate the removal of the finished product and prevent damage to the mould.
Once this is all done, the mould will be carefully closed. Proper closing is crucial to prevent leakage of powder or air. Hand clamps, bolted connections, or advanced automatic pneumatic clamps can be used to close the mould.
Step 2: Heating and rotational heating
Once the mould is filled, it is placed in an oven heated to temperatures between 250 and 300°C. The correct combination of heating time and temperature is calculated in advance and is essential to ensure that the powder melts completely without material degradation. During this phase, the mould rotates slowly over two axes (biaxial rotation, usually 4 to 20 revolutions per minute). This rotation ensures that the material is evenly deposited, creating a consistent wall thickness. The plastic powder melts and adheres to the inner surface of the mould through a process of sintering. There is no external pressure, allowing the material to spread evenly and reducing the risk of internal stresses and defects.
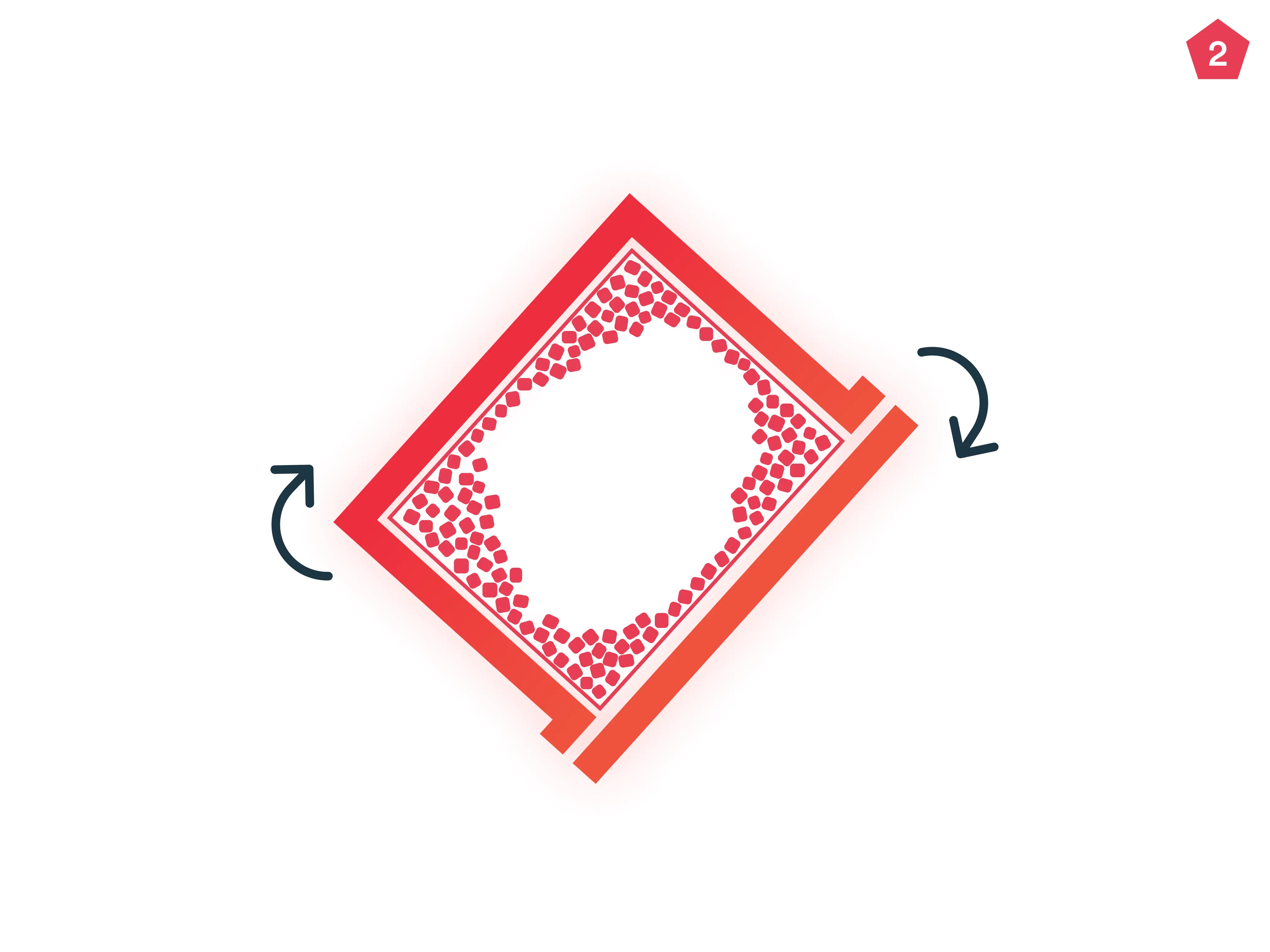
Step 3: Cooling
After melting and forming a uniform layer, the mould is moved to a cooling station. Here the mould continues to rotate while it cools down to approximately 70°C. It is important that the mould continues to rotate during cooling to ensure even shrinkage and cooling. This helps to prevent distortions such as warping and uneven wall thickness. Depending on the material and the requirements of the final product, air or water cooling can be applied. Air cooling is usually slower and more controlled, while water cooling is faster but carries a risk of thermal shock. The thickness of the product also greatly affects the duration of the cooling process; the thicker the wall, the more time is needed to cool. A thicker wall thickness also increases the chance of product deformation.
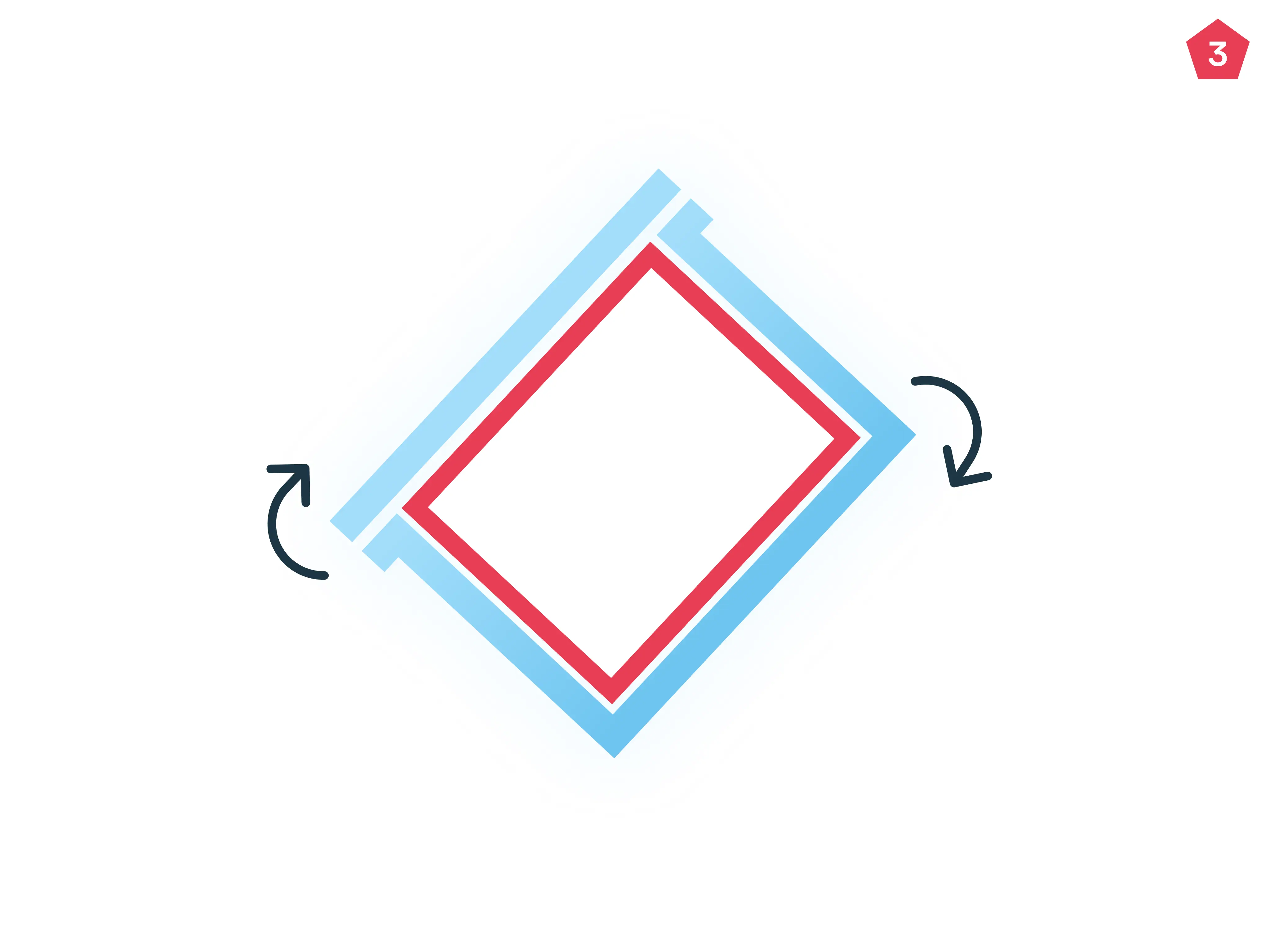
Step 4: Removing the product
Once the plastic has sufficiently cooled and solidified, the mould is opened. We have developed a pneumatic clamping system to speed up this process. The newly formed plastic product is carefully removed from the mould. At this stage, it is important to work carefully to avoid damage to both the product and the mould. The product is then placed in a specially designed support mould to cool further. This support mould helps to maintain the critical dimensions of the product while it fully cools.
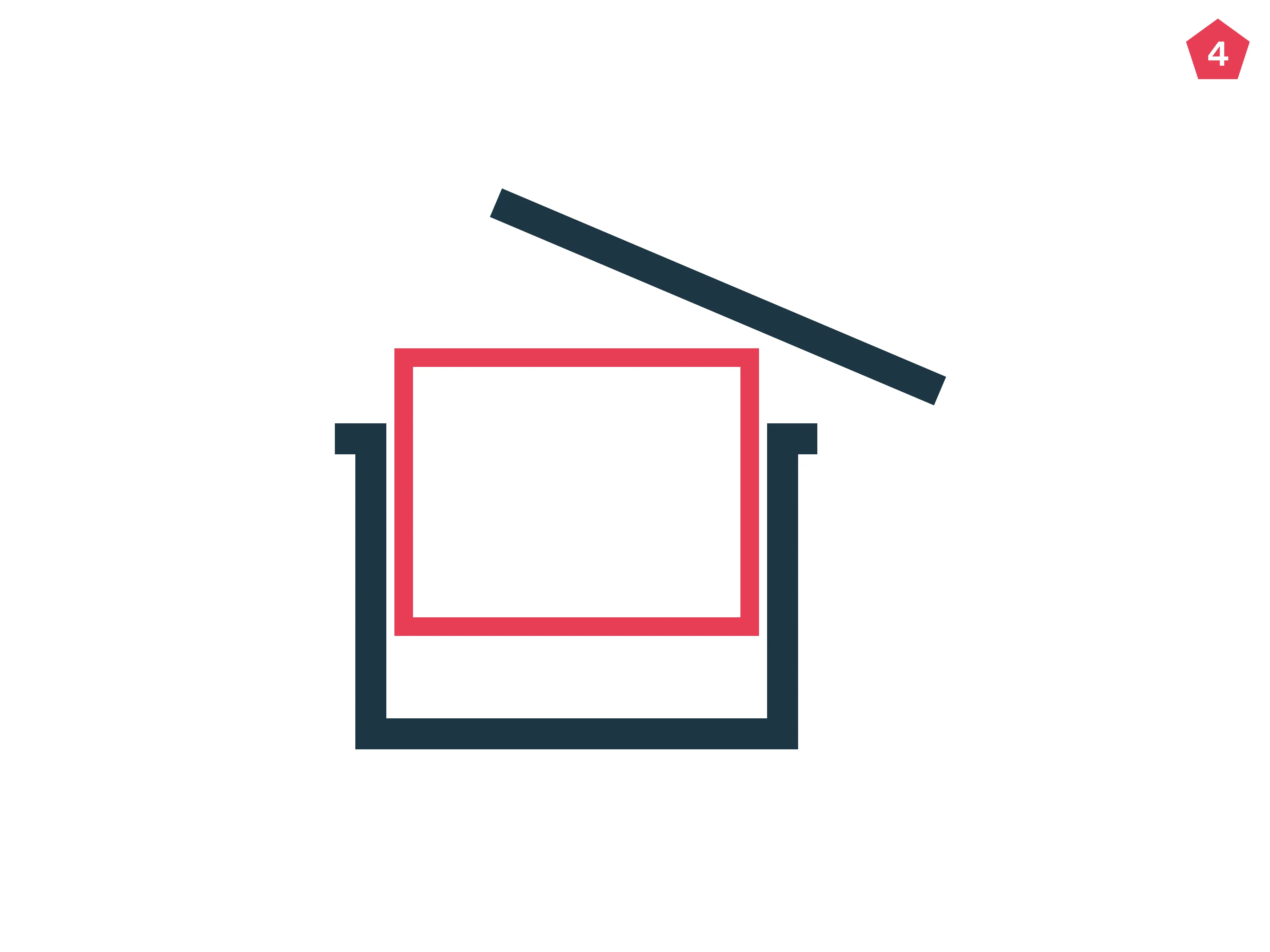
tep 5: Preparing for the next cycle
The final step in the cycle is cleaning the mould and preparing it for the next batch. This preparation includes inspecting the mould for any residues or imperfections and reapplying any release agents. In continuous operation, this cycle can run 24 hours a day, five days a week, maximizing productivity.
Rotational moulding is a versatile and efficient process for manufacturing a wide range of hollow plastic products. From accurately filling moulds to controlled cooling and careful removal of the product, each step is designed to ensure high quality and consistent output. This allows us to deliver reliable and durable products for various applications.